Industry Leader Landglass Lists Knowhow Gathered Over 20 Years In Business
LandGlass talks about product positioning, criteria that determines the correct furnace, different kinds available in the market and ways to make a furnace more profitable among others.
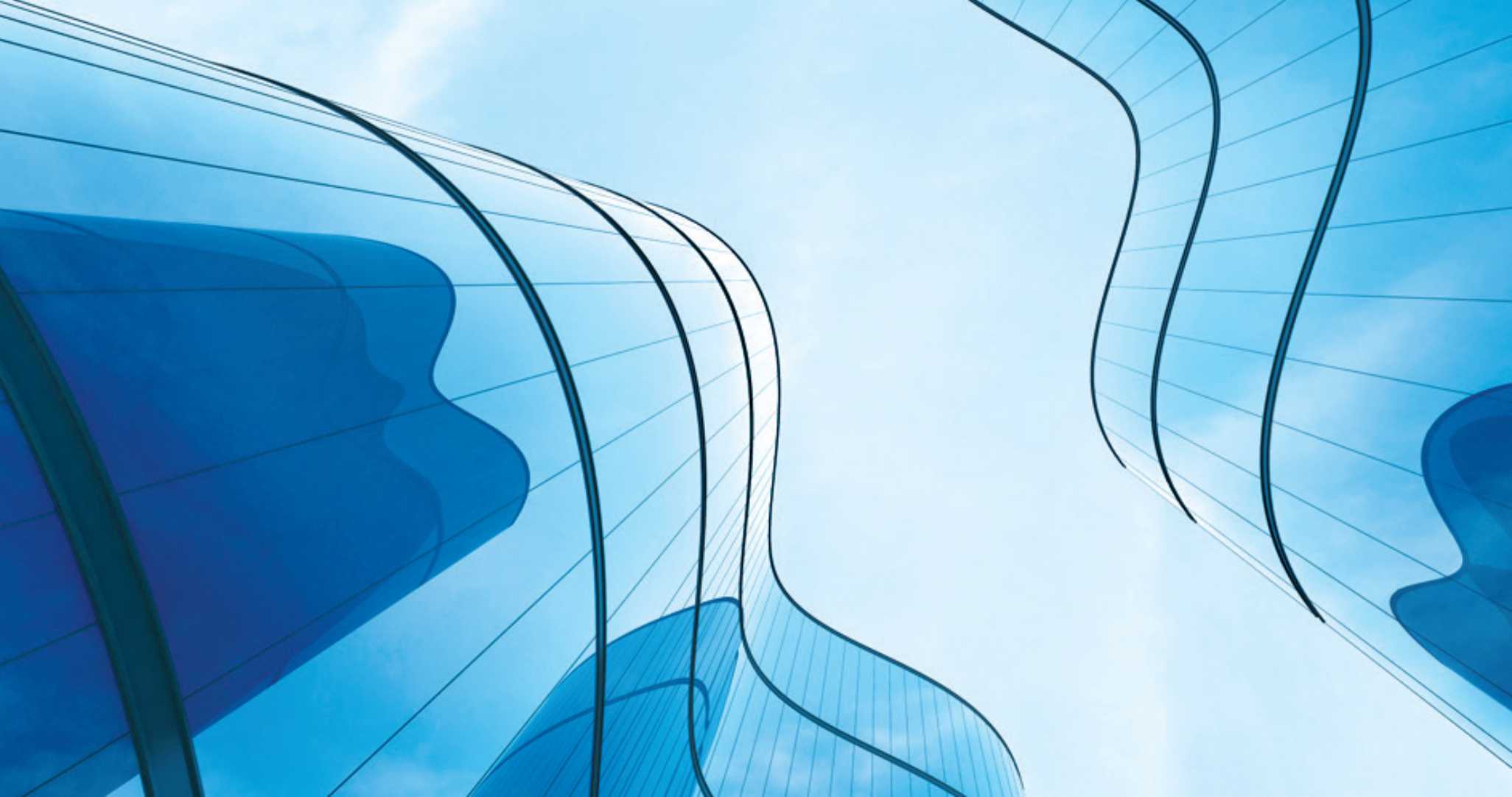
It could determine an enterprise’s market value, the distribution of customer base, and overall profitability.
Being in the glass processing machinery business for more than 20 years, LandGlass has seen numerous successful cases of investment in glass tempering furnaces. This article intends to help those who plan to invest in glass tempering machines to properly evaluate the operating environment and their own situations before making a purchasing decision.
Before purchasing a glass tempering furnace, have a clear view of the product positioning.
The customers of the tempered glass market can be divided into Type B customers (who place more regular orders) and Type C customers (mostly are small and irregular orders). Type B customers place engineering orders including glass for doors, windows and curtain walls. These products generally have standard specifications;
Type C customers refer to the customers in the home improvement market that can be further divided into customers for high-end system windows and for general household windows.
Among them, both Type B curtain wall and Type C system windows have very high requirements on optical quality and glass surface quality. As such, the requirements for machine configurations are also high. Customers should choose the glass tempering furnace with the appropriate configurations according to their product positioning.
What are the criteria typically used to determine the right tempering furnace?
Capacity matching: The capacity of the glass tempering furnace should match the estimated annual overall production output. Take LandGlass A2850 glass tempering furnace as an example, to produce 5mm Low-E glass (E=0.08), the production capacity is 15-18 loads/hour. The annual output is approximately 1.50 million square meters of glass.
An enterprise may calculate the required capacity according to the estimated annual output and select the appropriate model of the glass tempering machine.
Floor space: Different types of glass tempering furnaces, such as flat glass tempering furnace, bent glass tempering furnace, flat and bent bidirectional glass tempering furnace, combined tempering furnace, and continuous tempering furnace have very different longitudinal sizes.
Customers should take into consideration the actual space available when choosing their models. Besides, the space for the temporary storage of unfinished glass products needs to be reserved in advance.
Power load: Different glass tempering furnace models need different installed power. Take 5mm clear glass as an example, the installed power of the A2850 single chamber is about 1300kw while the installed power of a combined glass tempering furnace is approximately 2400kw. Enterprises should consider the installed capacity of their existing transformer and the possibility of expansion when choosing the machine models.
Machinery the competition uses: In line with the consideration of competitive differentiation, the capacity of your glass tempering furnace generally should be larger than that of your competitors’ in the region. For instance, if your competitor is equipped with a glass tempering furnace for glass size 2.4mx5m, you should consider a glass tempering machine for glass size 2.4mx6 m or 2.8mx5m.
Forced convection glass tempering furnace or radiation glass tempering furnace?
When it comes to forced convection, we have to talk about Low-E glass.
Low-E glass is known for its low-Emissivity properties. In short, it reflects a lot of radiation heat, making it difficult to heat up quickly with radiation heating. When using a radiation glass tempering furnace to heat the Low-E glass, the radiation heating takes too much time and the uneven heating between the upper and lower glass surfaces seriously affects the quality of glass.
While forced convection glass tempering furnaces take the air convection approach, directly blowing heated air to the glass surface, overcoming the reflection of Low-E glass in radiation heating. Therefore, when the volume of coated glass tempering accounts for more than 30% of an enterprise’s orders or there is a great variety of glass tempering tasks, it is recommended to choose a convection glass tempering furnace.
Even for clear glass, the performance of a convection tempering furnace is significantly better than that of a radiation tempering furnace. Hence, it is recommended that enterprises should buy forced convection glass tempering furnaces.
Are all convection technologies the same? No, they are not the same
Three key factors to consider when evaluating the convection technology:
- The proportion and efficiency of convection heating
- Whether the heat is distributed evenly
- Whether the temperature control is accurate
At present, there are primarily three convection technologies in the industry: pipe convection, chamber convection, and OptiFlow convection.
As a basic technology, pipe convection is the transitional technology between radiation furnace and convection furnace. Chamber convection is an upgraded technology based on pipe convection.
OptiFlow convection is a further upgrade from the chamber convection, effectively improving the heat exchange efficiency and heating uniformity in the furnace for a better result when tempering double-silver and triple-silver Low-E glass. In addition, for true convection heating, the heating elements should be located in the positions where the convection system blows air, not the positions where the air returns.

Top convection glass tempering furnaces use air convection in its top part to heat the upper surface of the glass. The bottom part still retains the conventional radiation heating method. It will work well for those who have fewer Low-E glass orders.
Full convection tempering furnace adds convection devices to the bottom part to enhance the bottom heat transfer. This will avoid the spherical bending problems caused by the situation where the heat transfer rate of the upper glass surface is significantly higher than that of the lower surface when heating largesized glass or coated glass thinner than 4mm in a top convection glass tempering furnace. It ensures that the top and bottom surfaces of the glass are heated simultaneously for better heating quality and higher productivity. Meanwhile, the full convection glass tempering furnaces can better heat Low-E glass with complicated coatings.
In an era where quality dominates, the touchstone for tempered glass is anisotropy and flatness Anisotropy, also known as the iridescence, is a common defect seen on tempered glass in the curtain wall industry. It directly destroys the overall aesthetic effect of a building, may even result in product return.
A good glass tempering furnace will minimize anisotropy through appropriate structural configurations and manufacturing processes, improving the quality of building curtain walls.
Flatness is also an essential indicator of tempered glass. Laminated glass in particular has a higher requirement on flatness.
The national standard has clear definitions on how to measure glass flatness, especially the overall bow and the waviness. At present, advanced glass tempering furnaces can achieve overall bow≤1 ‰, center waviness≤0.05/300mm, and edge waviness≤0.10/300mm in 6 mm clear glass mass production, far higher than the national standard.
Customers should consult the actual machine users or do the field research before buying the machine rather than relying merely on advertising.
How to make your glass tempering furnace more profitable?
Generally, glass tempering furnaces account for the largest proportion of a factory’s total electricity consumption.
Good integrated energy-saving technology adopted in the glass tempering machine can save you a lot of money. For 4mm or thicker glass, the main energy consumption unit of the glass tempering furnace is in the heating section.
The amount of heat required to heat the glass is constant. Reducing heat loss during machine operation is a good approach to save energy. Heat loss in the heating section is primarily from the furnace walls and in the convection structure. LandGlass’ glass tempering furnace adopts ThermoLock technology, Labyrinth sealing, and grid-structure insulation to minimize heat loss and reduce operating costs.
How not to spend money in vain when purchasing a glass tempering furnace?
The quality of the tempered glass products and the reliability of the tempering furnace will determine the development and profitability of the enterprise in the next 5-10 years. Therefore, the reliability and product quality are far more important than the price of the machine.
The success of the enterprise is dependent on the high quality of your tempered glass products. Reliable machine and a complete maintenance plan can effectively reduce the frequency of machine failure and downtime. If the purchase of cheap machine leads to a substantial increase in annual maintenance time, additional labour costs and possible penalties on delayed delivery could add up to millions. As such, low cost may save you money for the moment. However, the resulting product quality issues, additional operation expenses, and increase of maintenance could cost an arm and a leg in the long run.
How to choose your long-term partners to win the future?
Brand strength: Major brands often have their own R&D, design, and manufacturing teams. Their products have been proven in the market and quality is guaranteed. In addition, LandGlass has the ability and experience to offer tailored design, manufacturing, and commissioning based on your actual needs to better meet your requirements for product quality. When you buy glass tempering machine from brand manufacturers, you also receive their brand support, which may directly determine your pricing power and influence on the market.
Innovation strength: Companies that have powerful innovation strength are highly sensitive to the market. They can clearly identify market changes and update or upgrade their products accordingly. Partner with them may better assure the technical life of your glass tempering machine. Enterprises should focus on their core competitiveness and work with the right partners to win the future.
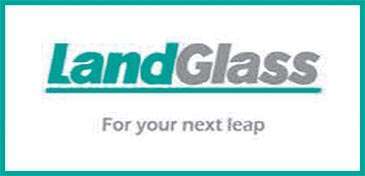