Developed Specifically To Increase Production Capability With Structural And High-Strength Laminates
Convection Control system makes processing complex laminates feel more like working with standard ones which means glass processors will be able to reach higher capacity and yield.

More and more regulations require safer products, and the number of applications mandating safety glass is booming, too. At the same time, architects are looking to maximize the transparency of their buildings while making their designs unique.
Greater demand for high-strength laminates
One of the products increasingly required by the market is highstrength/ structural laminate.
Originally this demand started from special applications, such as structural laminates (that can replace load-bearing structures such as pillars in buildings, perhaps the most famous example being the Apple Store in New York) and hurricane-resistant glazing.
But with ever-increasing safety demands for products, high-strength laminates are rapidly making their way to traditional applications such as railings, as well.
While these type of laminates offer often superior performance for the application, they also are more complex to process. This leads to a situation where glass processors are facing a demand to produce these products in increasing quantities, while struggling with yield and capacity. When this is combined with the fact that structural interlayers are typically more expensive than traditional ones, being able to ensure high yield is of utmost importance.

A narrow operating window (range of optimal process temperature) is the main reason for these difficulties. In general, the more complex the laminate is in terms of size, shape, glass type or laminate composition, the narrower the range of optimal temperature is for the process. As a result, quality can be impaired.
One of the most common quality issue seen in the laminating process is bubbles at the trailing end of the laminate. In practice what the bubbles mean is that there is too much air left inside the laminate. While there can be multiple reasons that are causing this, with high-strength laminates the reason is often overheating of the edge areas of the laminate. The same phenomenon happens regardless of the heating type used, and it happens on every edge of the laminate (leading, left, right and trailing). The issue is predominantly seen on the trailing edge as that’s where most of the air gets pushed during pressing.
New convection technology cracks the challenge
The good news is that an efficient solution for the issue has been found.
Glaston’s patented Convection Control technology has been developed specifically to increase production capability with structural and high strength laminates.
Until now, glass processors have had to be very precise to achieve good quality with complex laminates while struggling with yield. With the new convection control system, processing these products becomes more like working with standard laminates.
In practice this means that glass processors will be able to reach higher capacity and yield with complex laminates.
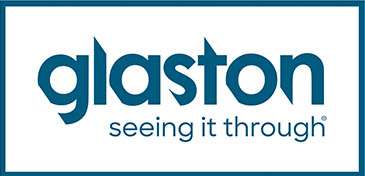
Website: www.glaston.net