Sr HEGLA Executive Shares Insights On Perennial Topics About The Sector
Improved efficiency, more automation and user-friendly processes are perennial topics in the glass processing industry. In this connection, Senior Product Manager for Vacuum Lifting Equipment at HEGLA Holger Brechtelsbauer answers a few questions.
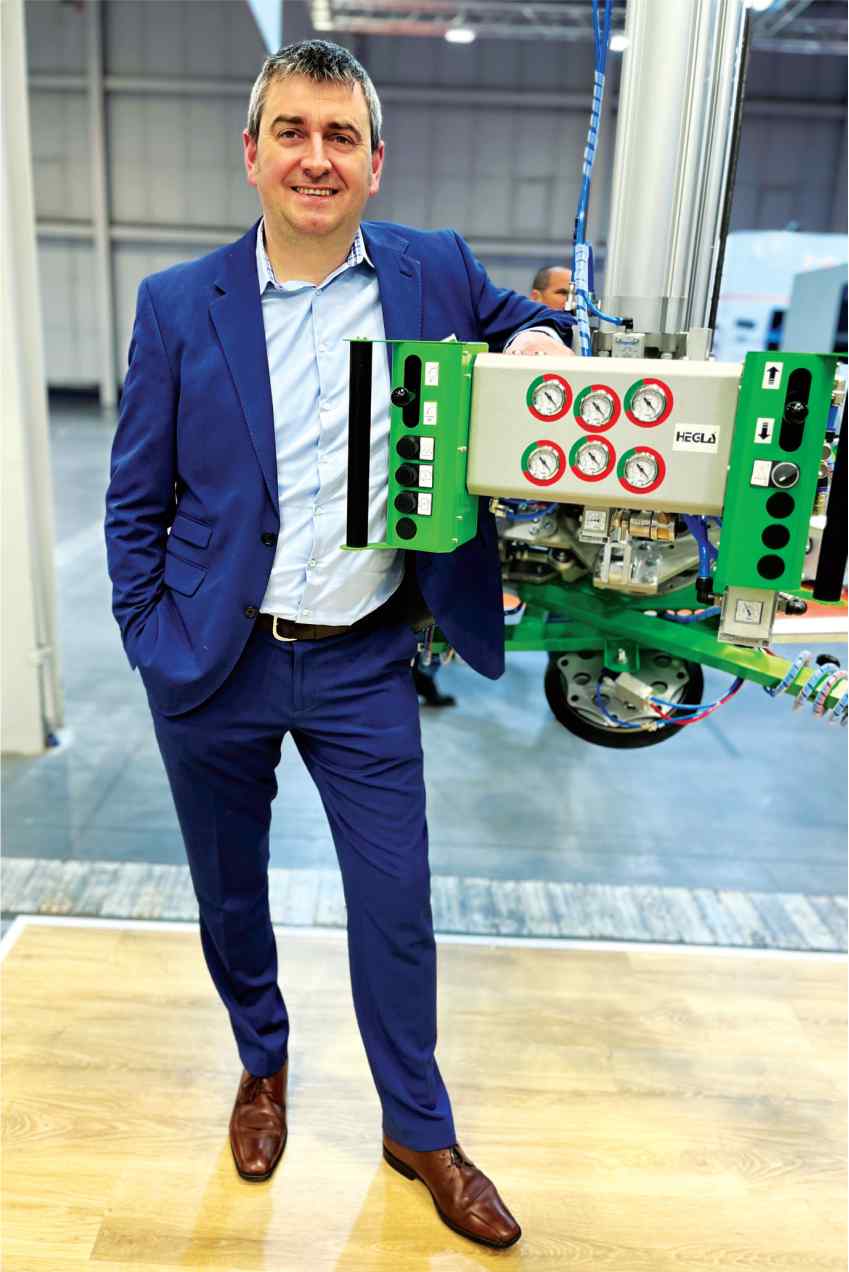
– What contribution can vacuum lifters make? What considerations do you recommend in advance?
With modern processing equipment, off-peak times are already optimised for maximum efficiency and costeffectiveness.
To ensure that the full potential of the systems can be exploited, when making an investment or reorganising it is valuable to take an early look at the overall processes and dependencies, including during handling. The approach is similar to those in other industries.
Together with the customer, we start considering what a system can achieve under the best conditions.
For handling, we then consider which pane formats need be processed and what the resulting weights are.
Experience shows that some operating companies are reluctant to deviate from the maximum sizes and are inclined to cover the entire spectrum with large and therefore, oversized, vacuum lifting equipment.
Evaluations indicate, however, that in everyday operations, small glass units generally dominate. The aim should thus be to rapidly move exactly this 85 to 90 per cent of panes onto the system or back onto the glass rack.
Lifting devices can then be chosen to carefully match this requirement, ensuring they are ergonomically and optimally integrated for these tasks and are not oversized.
Combined with a suitable lightweight craneway, for example, this lays the foundation for meeting the possible cycle times of systems.
The remaining 5 to 10 per cent of large panes are not ignored in this design either. There is often an indoor crane which can be linked up with an additional lifting device for the heavier units.
Alternatively, lightweight craneways can be designed with multiple crane bridges. In any event, it always pays to supplement a processing system with adapted vacuum lifting technology.
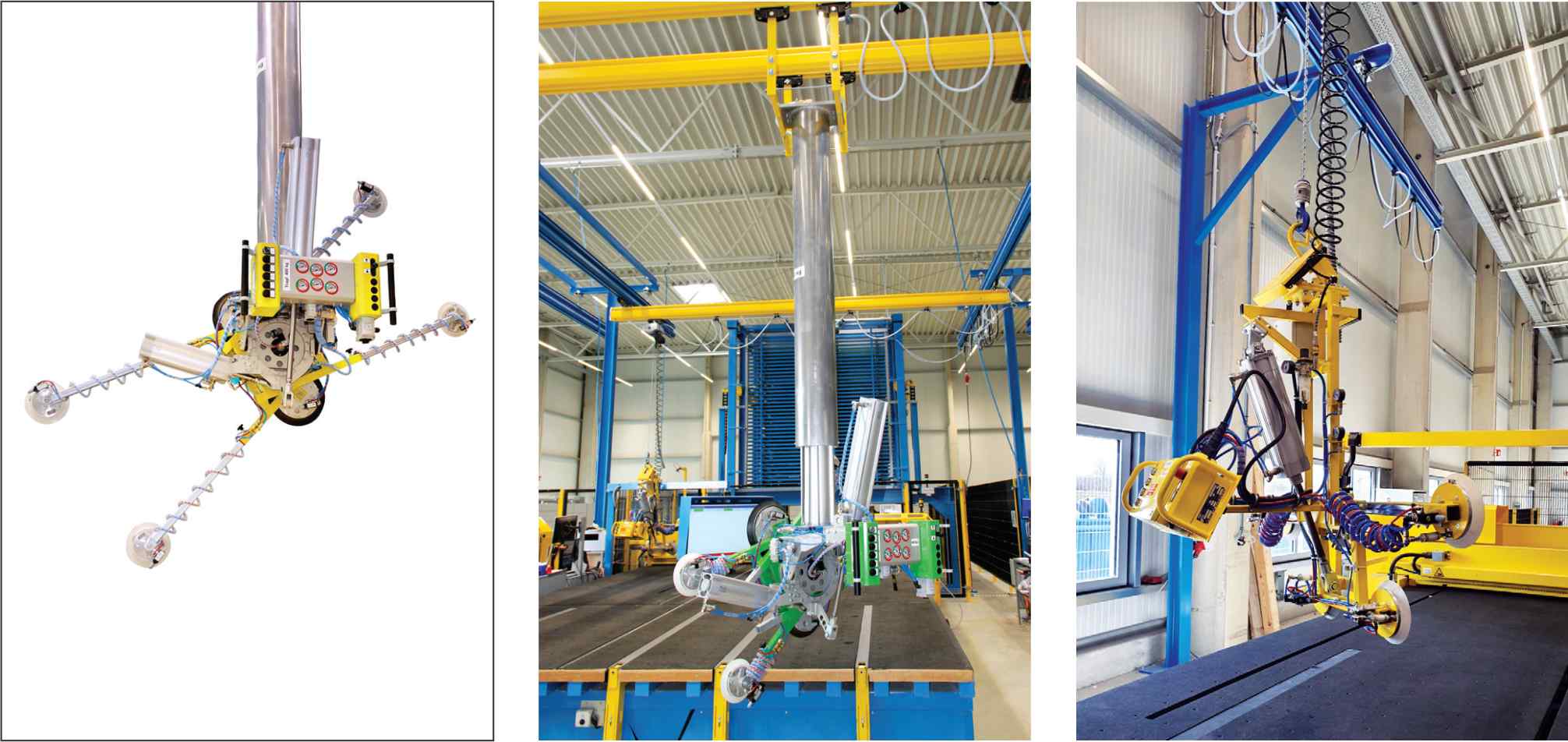
“Traditional handling equipment and operators will continue to have their place in increasingly digital and automated production processes. There will certainly be an increasing number of applications in which robots could be used as an alternative. However, glass weights and formats are increasing and becoming more varied at the same time, so there are limits.”
– The glass processing industry has to handle increasingly heavy and large panes, which is often a challenge to machine operators. What needs to be considered when choosing a handling device when it comes to safety and user friendliness?
Operator safety is obviously the first thing you need to consider when choosing a vacuum lifter. It’s also nonnegotiable.
On top of that, ergonomic functionality should confirm at all times to employees that they are entirely safe and flexible when working with the handling device.
The German load handling directive implementation law states that heavy panes start at a weight of 15 to 20 kg. The handling devices for these weights can usually be moved manually in a lightweight craneway and provide support. The load control of the suction device has a key influence on both ergonomics and operator convenience.
The current trend is towards pillarguided vacuum lifting equipment, where a torsion-resistant aluminium pillar ensures high motion stability, load control, positioning accuracy and maximum employee protection.
– Where do you think the future demands on handling equipment with respect to increasingly digital automated production are heading?
First things first – traditional handling equipment and operators will continue to have their place in increasingly digital and automated production processes. There will certainly be an increasing number of applications in which robots could be used as an alternative in order to further boost automation.
However, glass weights and formats are increasing and becoming more varied at the same time, so there are limits. We are also seeing more transfer stations with shuttles and self-driving systems between different processing stations. But in existing buildings, this is often unfeasible due to space limitations. With this in mind, I can foresee intermediate steps of digitalisation. By scanning laser markings or labels, the individual panes and racks can be registered.
The handling device will then be integrated into the communication flow as a direct and decisive link, contributing to an integrated overview and dynamic, flexibly adaptable overall processes.

Email: carsten.koch@hegla.de
Website: www.hegla.com