Brings Wide Range Of Processing Machines, From Cutting Tables To Double Edgers & CNC
To keep pace, raise productivity and stay competitive, companies must invest in new equipment, but re-shape the workshop production flow.
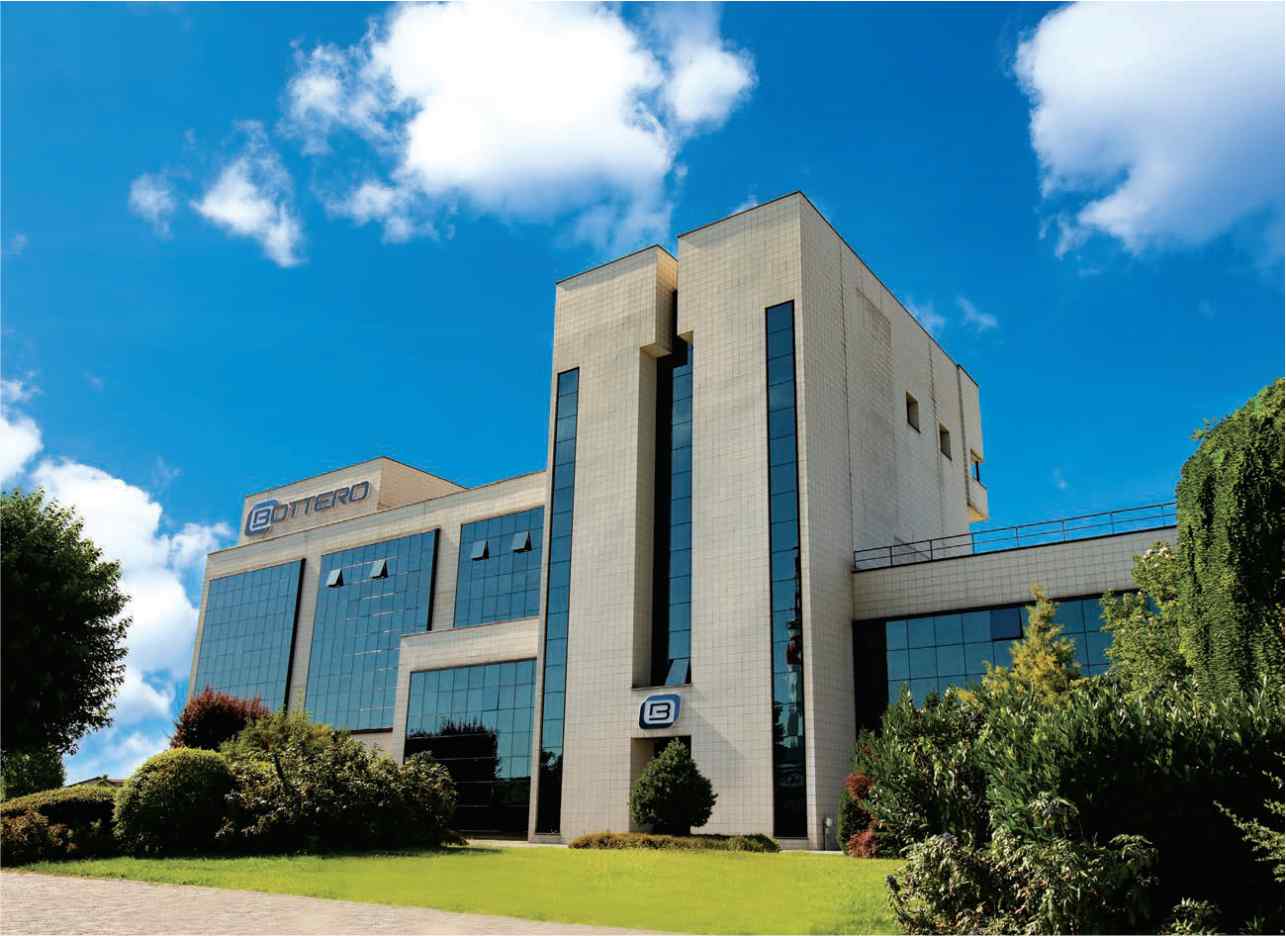
The new challenge for glass makers is to keep pace, raise productivity and stay competitive. This means investing in new equipment, but mainly reshape the workshop production flow following lean principles.
Bottero S.p.A. has solutions ready to go for all these challenges, based on three main pillars:
- Modular machines and platform concept.
- Integrated systems tailor-made to customer needs.
- Bottero 4.0: a comprehensive suite for machine learning and artificial intelligence.
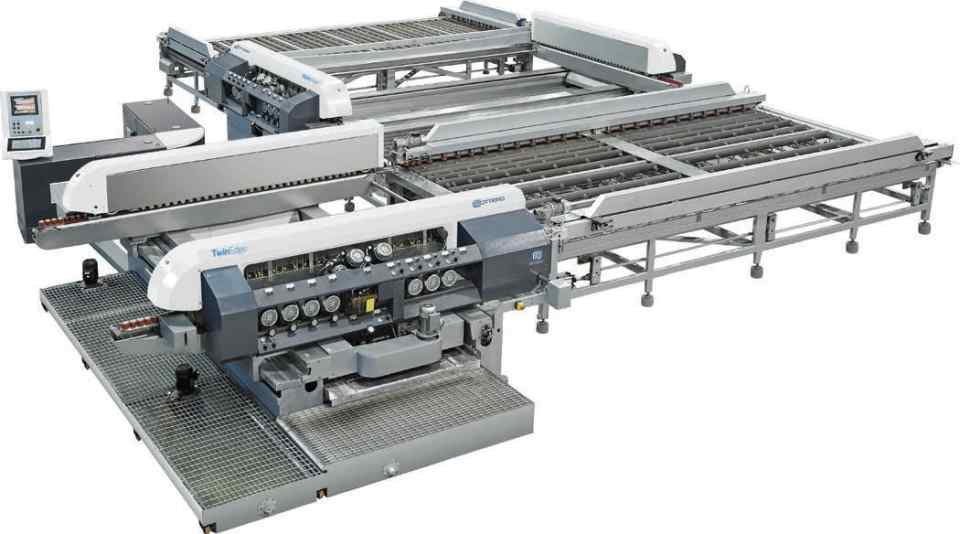
With more than 200 glass production equipment items and more than 50,000 processing machines installed around the world for any type of glass, Bottero is an unmissable partner for everyone who wants to cut a piece of glass.
Its product range in cutting (BKM, BCS and EVO) is the widest and most in-depth available today in both stand-alone and dual-line with a laminated glass cutting table, or within an integrated line with stock management systems such as crane loaders or shuttle systems.
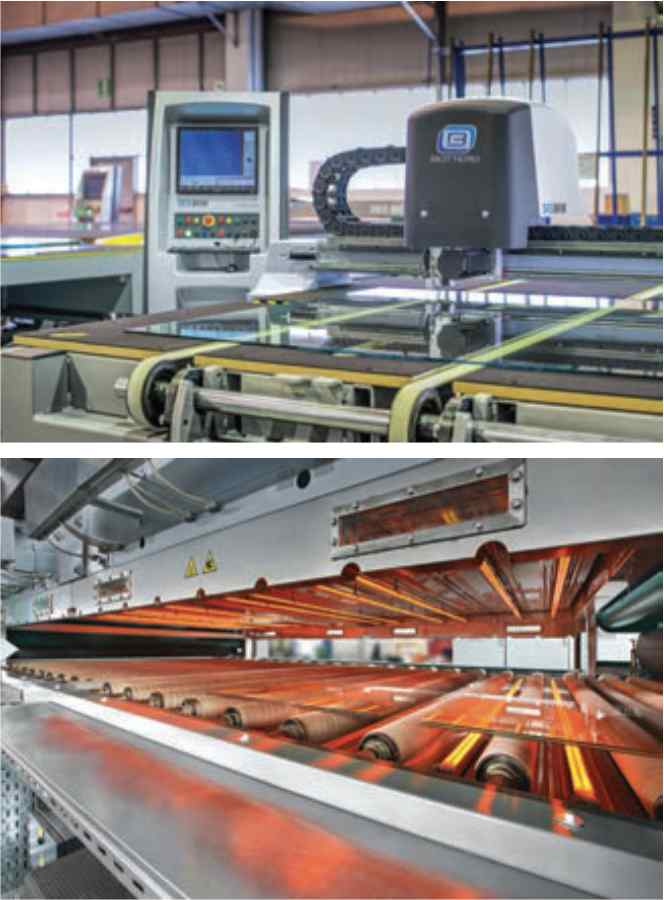
Every Bottero cutting table gathers more than six decades of experience and know-how in the glass sector, ensuring not only perfect cutting quality and a user-friendly approach but also remote support and preventive maintenance tools.
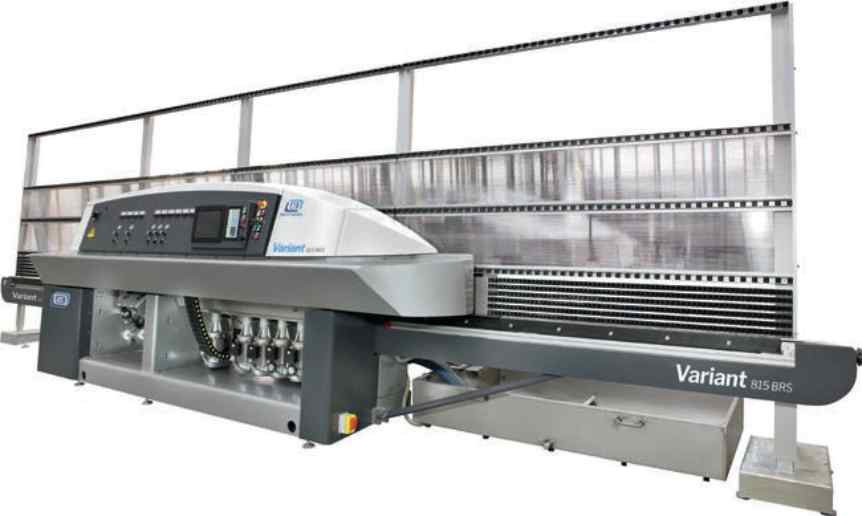
Bottero offers a wide range of solutions for laminated glass processing scalable in terms of modularity and automation level, suitable to process laminated glass with PVB (acoustic and/or refrigerated), EVA and special antihurricane interlayers.
Its R&D department is continuously working to innovate its laminated glass product range to ensure that the company remains the undisputed leader in this field.
The company’s most advanced equipment is the 548LAM, a fully automated table that can process different laminated glass types with reduced cycle time and energy consumption.
Thanks to a great number of patents, Bottero’s PVB heating system focuses energy on the PVB without heating the glass, thus reducing cycle time by 30%, saving up to 40% of energy costs and reducing the number of glass breakages.
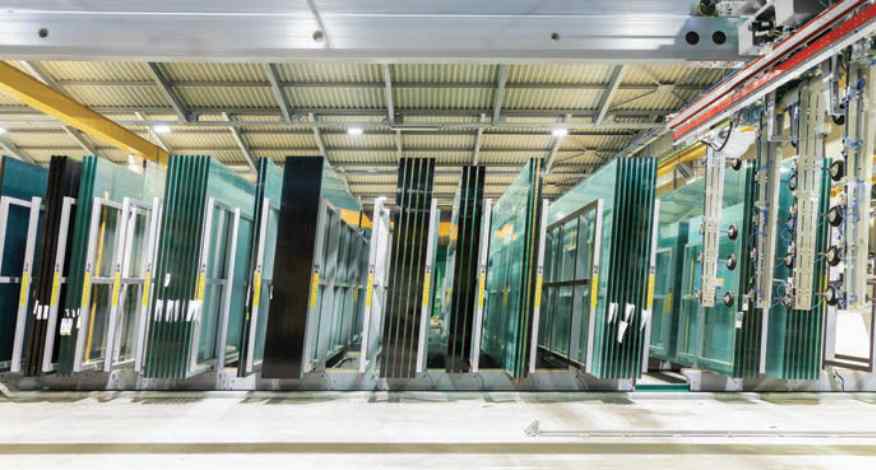
Operator manual intervention is eliminated thanks to the patented squaring device for glass positioning and rotating, as well as by means of automatic loading and unloading arms.
With regards to laminated glass production, Bottero is currently a market leader in the assembly line segment with a full range of solutions ranging from entry-level, with manual loading and unloading, up to fully automated with automatic PVB unwinding and trimming with an output cycle time of 38s per JS plate of up to 6,000 x 3,300 mm.
Bottero Flex Lamilines can manage shaped glass from 200 x 200 mm up to XJS glass of 12,000 x 3,300 mm in multiple layers of up to 100 mm thickness.
Thanks to a great number of patents and more than 25 years of experience worldwide, Bottero offers state-of-the-art nip rolls and furnace areas for laminated glass production, suitable for a huge variety of glass sizes and dimensions.
Modularity and scalability are also applied to Bottero’s wide range of horizontal double edgers and vertical edgers.
While double edgers represent the best solution when high grinding and polishing quality is required, vertical edgers are more flexible and can be easily integrated with robots for loading, unloading and glass rotation.
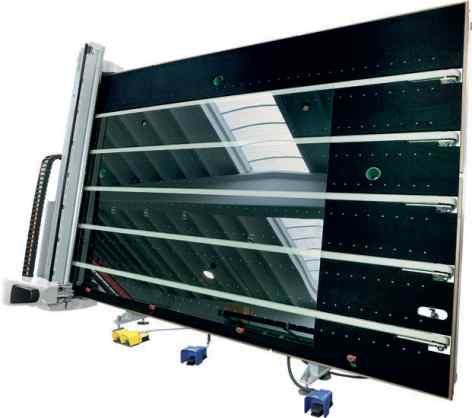
Of course, double edgers ensure perfect parallelism, squareness and multiple profile finishing, including arrises, engraving and polished radius corners. With Bottero’s new Flex Edge, customers can really customise their machines with up to 17 spindles per side, with an unlimited range of dimensions up to 12,000 mm opening width.
Remote service, cloud connection and preventive maintenance tools are the basic tool set of Bottero edgers.
Bottero is and has been since 1957, customer-centric
The company’s Pre-Sales and Sales Department pay special attention to understanding customer expectations and limitations to develop the best proposal fitting customer needs and reducing Total Cost of Ownership (TCO).
Fewer manual operations and more automation have allowed many of its customers around the world to improve their competitiveness and market leadership.
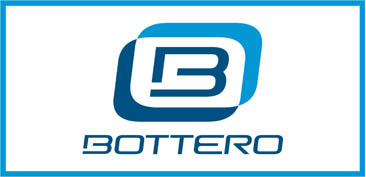
Email: marco.bellino@bottero.com
Website: www.bottero.com