‘Switching To Glaston Brought Operators Much Better User Experience’
Still running strong with upgrades, the company’s all three plants throughout Germany have Glaston tempering furnaces.
References include windows and safety glass for high-speed ICE trains and yachts, along with glass for the world-renowned The Shard in London, the Microsoft office in Munich, the prominent Axel Springer building in Berlin and many more. A key to the company’s success has been its commitment to ongoing improvements in the performance and energy efficiency of its equipment.
“We feel upgrades are the best way to keep running strong,” said Martin Werner, Technical Manager at FLACHGLAS Wernberg GmbH., who joined the company in 2017 and now heads up the technical department. “Our machines are older, but all are still efficient and running strong because of the continual upgrades and care.”
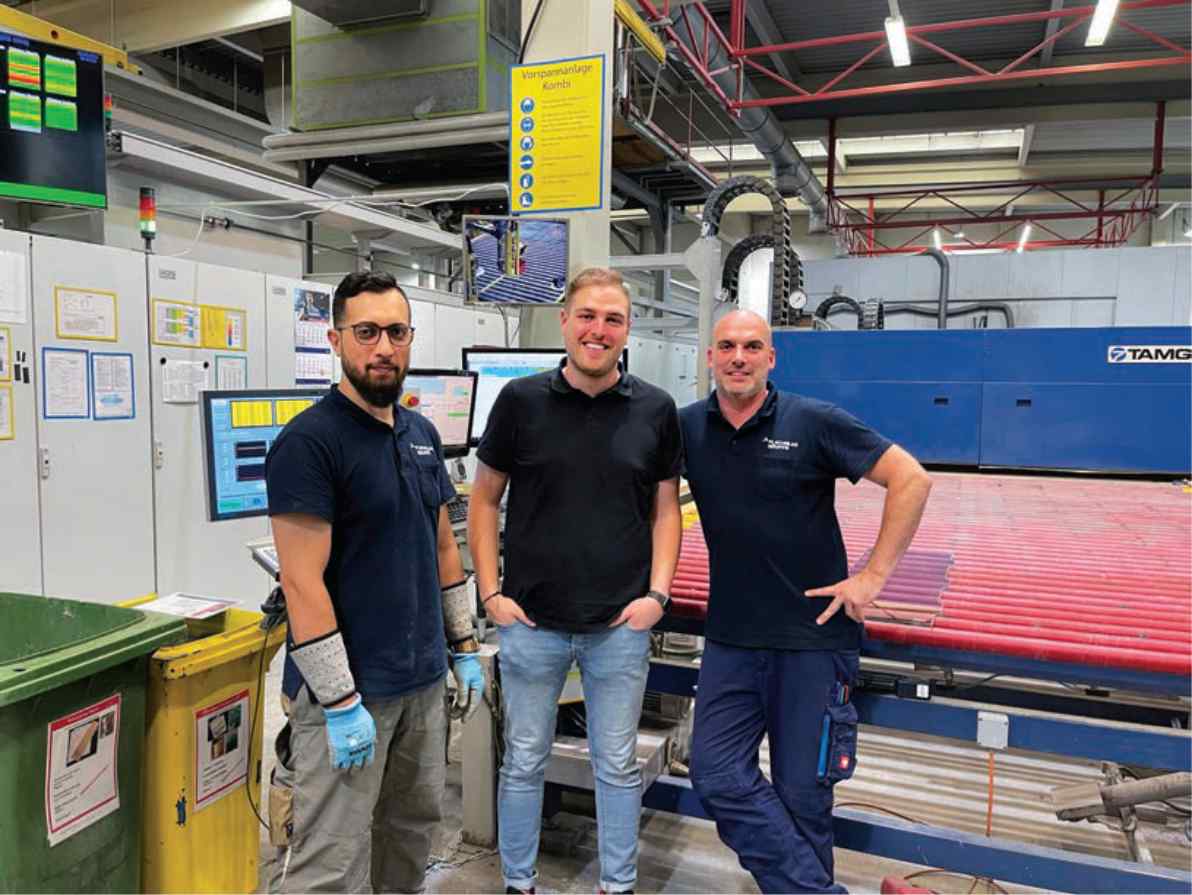
Upgrade list keeps growing
Some of the key upgrades include the 2015 modernization of a 2004 Glaston ProE machine with the latest Glaston iControL automation system and bottom Roller Heat Control (RHC).
“By changing the bottom heaters and replacing the bottom convection, ProE could better handle the new coatings. Also, switching to Glaston iControL gave our operators a much better user experience,” Martin said.
“For our HTF Combi Convection furnace, we had issues with the availability of spare parts. So, we completely upgraded the electronic parts with the iControL, and now we are very happy,” he added.
Latest blower inverter modernizations
At the time, the only part not upgraded on those two furnaces was the blower inverters.
“In Germany, energy prices have been very high,” Martin explained. “I was in touch with Glaston to make calculations about the payback of upgrading the blower inverters. We also found out we could get financial support from the German government for improving the energy efficiency of the inverters.”
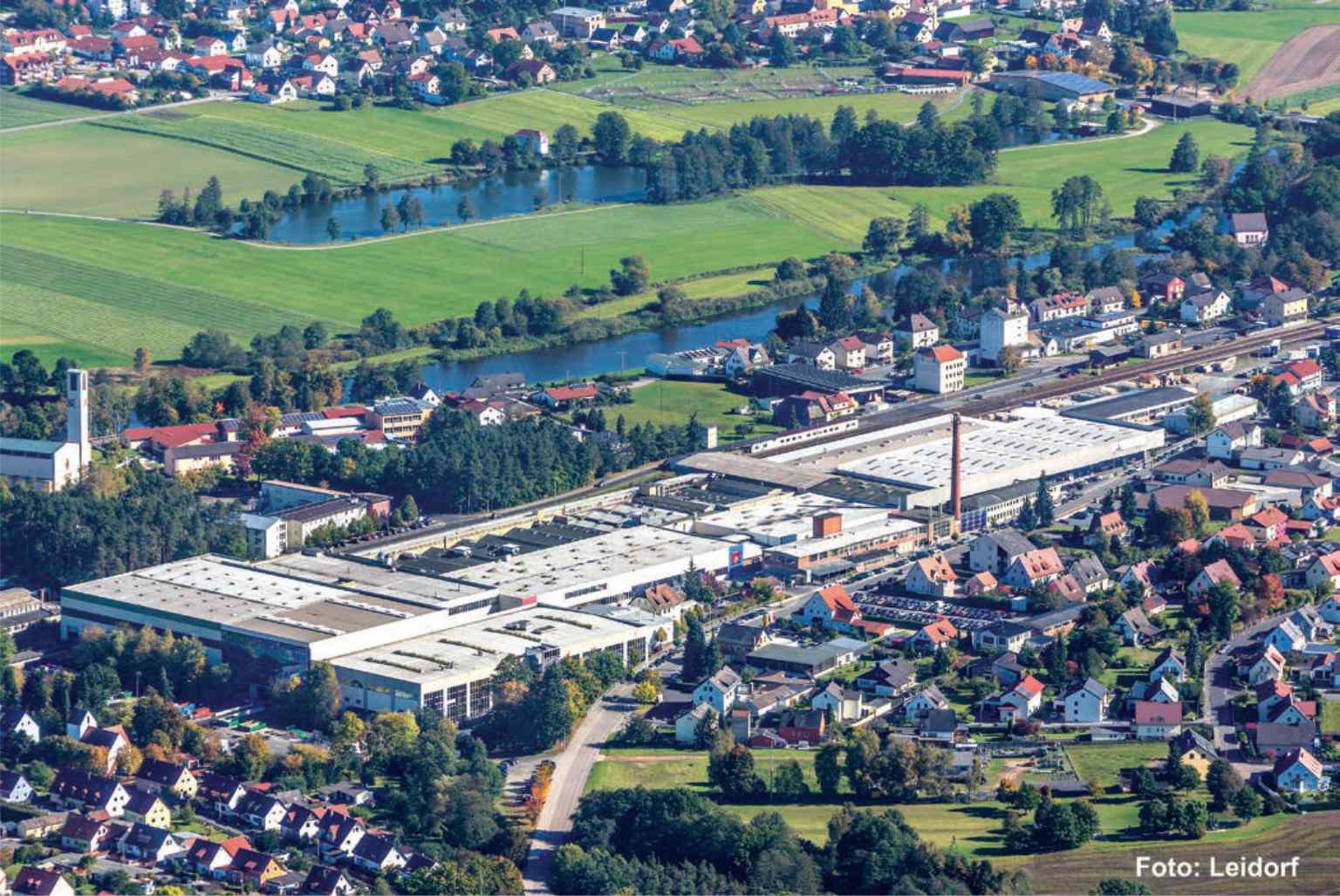
Martin and his team decided in the spring of 2022 to upgrade both the ProE and the HTF by modifying the blower drive with Glaston’s Variable- Speed Blower Control System (S™) and the Integrated Blower Vibration Monitoring System (BMON).
“We chose the Variable-Speed Blower Control to reduce energy consumption. We no longer need to wait for the blowers to stop to reset the blower mode when changing from 4-mm to 8-mm glass. This enables our production to be more flexible, cost-effective and faster,” Martin says.
The reason for the Vibration Monitoring system is to improve blower reliability and to avoid any crash of the blower wheels.
The furnaces were shut down in February 2023 for a total of five days for the work. “We experienced a few small issues, like the chiller profiles being more precise, so we needed to change the programs. This was unexpected both for us and Glaston. Still, it was a very good project overall,” Martin said. “In the end, we lowered the total annual amount of kilowatts we use in production with these projects – and now save money.”
FLACHGLAS already has its next upgrade project planned for January 2024, when it will modernize an existing lamination line with a Glaston ProL-zone.
Improving overall energy management
“These upgrades have helped us maintain and even expand our strong market position in Europe – despite the coronavirus crisis and intensifying competition,” he said.
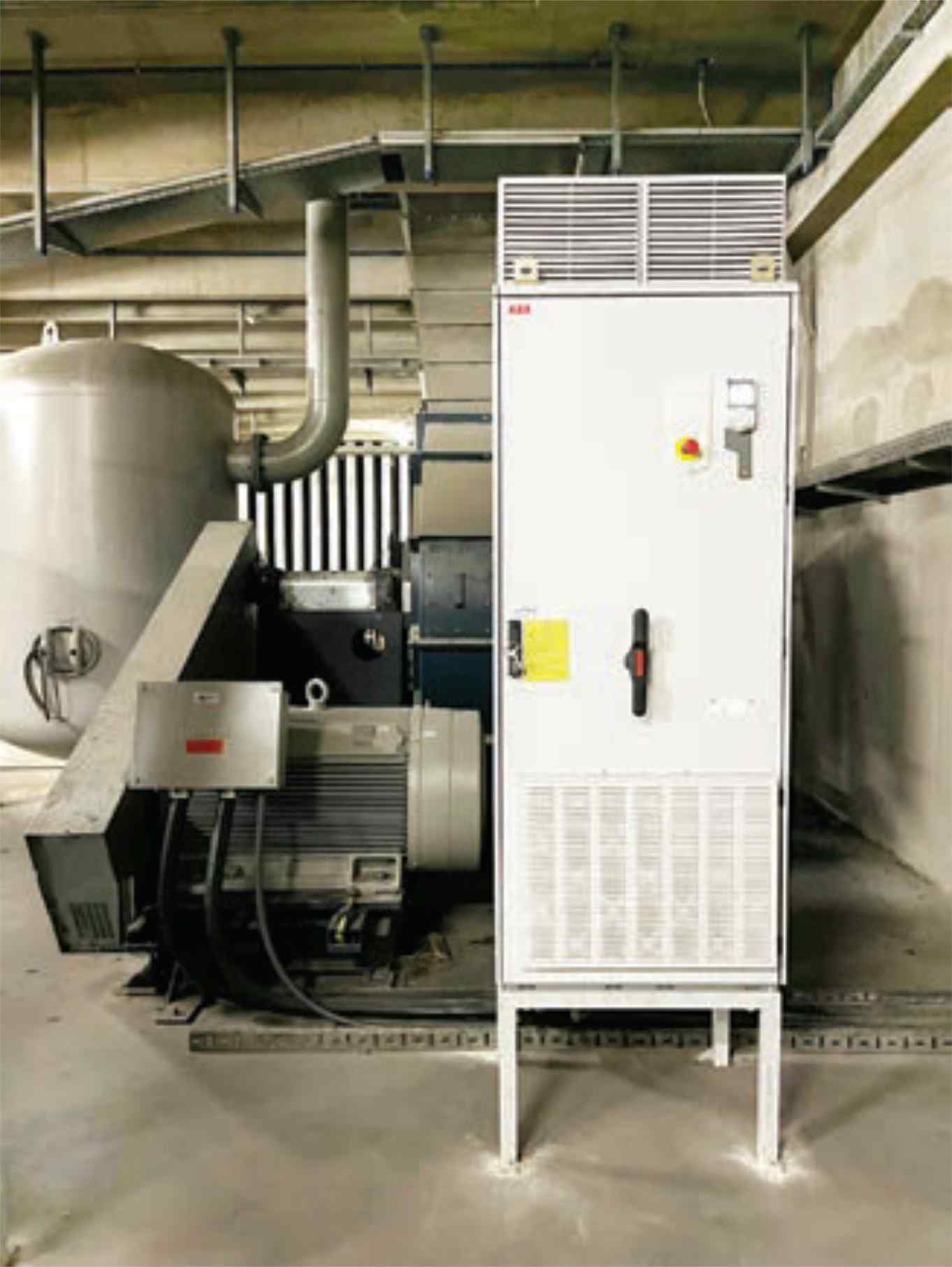
“Upgrades are a very good opportunity to improve energy consumption. By just changing the furnace or adding new components, we have gained better process quality. We can also do something good for the environment by running our machines longer. And, most importantly, upgrades help us save money,” he summed up.
About the company
Glaston is the glass processing industry’s innovative technology leader supplying equipment, services and solutions to the architectural, automotive, solar and display industries.
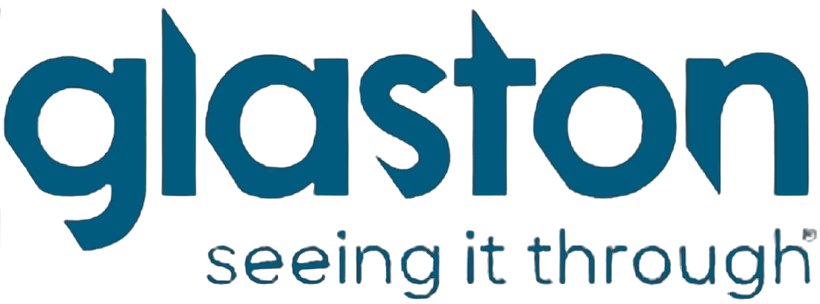
Email: info@glaston.net
Website: www.glaston.net