Breakthrough In Glass Recycling With HEGLA’s Innovative Technology
Revolutionizing recycling, HEGLA automates insulated glass separation, boosting sustainability and resource efficiency in building materials.
The amount of glass on buildings continues to increase: be it transparent facades and multiple IGUs on new buildings, or windows and panes that are replaced on existing properties at the end of the product life cycle. For many years, mixed glass containers were the go-to variant for glass disposal, but rising energy costs and society’s growing awareness of sustainability have increased the incentive to recycle.
With the IG2Pieces assembly line technology, HEGLA has developed a solution that can automatically separate insulated glass.
At the same time, the company offers a handling concept that retains the purity of the raw material and improves revenues or enables panes to be reused as such.
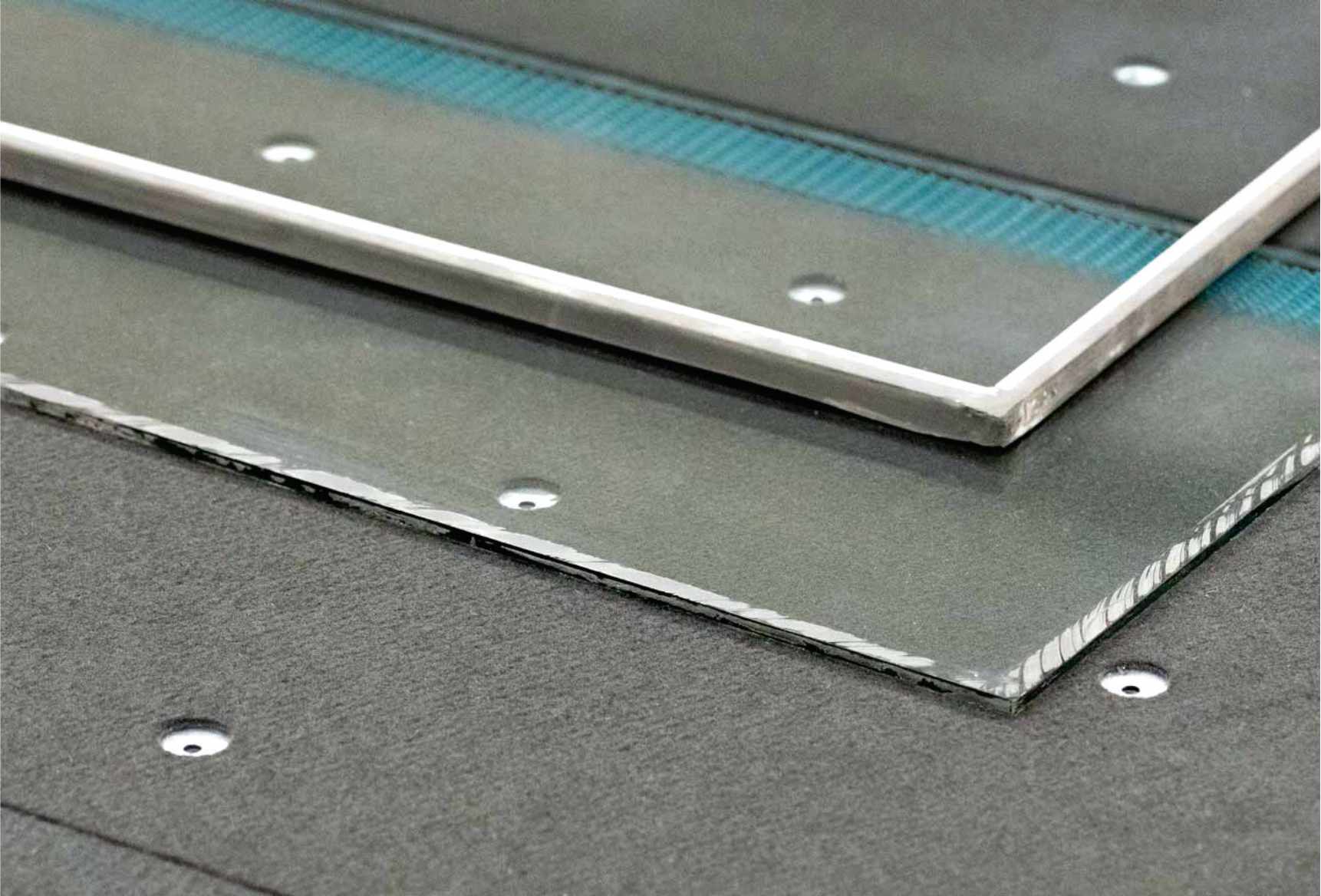
With IG2Pieces, HEGLA offers a system solution that can separate glass from an IGU, cleanly and without damage.
Dealing with imperfect panes and used glass sustainably
“Our development work was based on the question of how it is possible to deal with imperfect panes and used glass in a way that conserves resources and is efficient at the same time,” said Heinrich Ostendarp, Managing Director of HEGLA. To ensure that the glass panes remain usable for a range of applications, the aim was to release the individual panes from the spacers reliably, cleanly and without damage, while maintaining high productivity.
“Thanks to a newly developed separation method, the automated process leaves only a minimal amount of sealing compound on the surface of the pane,” added Dr Ostendarp.
The measurement of the ISO dimensions and the insulated glass structure is fully automated. Once the glass has been removed from the laminate, it can be recycled without any loss of raw material quality. Just like the panes, the unimpaired spacers, including the intact desiccant, are conveyed to a separate system for disposal or recycling.
Type-specific float glass yields financial advantages
Separated recycling of the individual types of glass yields advantages, compared to mixed containers. When panes are professionally separated, this generates added financial value.
The impact on the environment is also positive: the panes find their way back to the float tank to close the material circuit while preserving the quality of the raw material. Further, one kilogram of floatglass that is produced from used glass generates around 0.3 kilogram less CO2, compared to a classic glass mixture
Reuse and repair
Alongside type-specific recycling, the reuse of undamaged panes is yet another option that increases the recycling rate. “Separation and repair make particular sense for newly produced, large-surface and high-quality IGUs, if this is done productively and safely,” explained the managing director.
If, despite all precautions, there are impurities or surface defects in a freshly produced insulated glass laminate, the individual pieces can be cleanly removed and the defective pane can be disposed of, if necessary.
The remaining glass is available for further processing. This method can be economically attractive for special coatings, toughened glass, or laminated safety glass panes in particular, as well as complex and large attachments. “With our system, we accelerate and simplify a process that takes place manually in many companies and depends on the skill and know-how of the employees,” remarked Dr Ostendarp.
If repairs cannot be made during the ongoing production process or if no special-purpose cut is available, there is a third option. The clean application of butyl and sealing of separated glass can be planned for follow-up orders and cut to smaller dimensions. Applications here include LSG, high-quality, refined glass, or special-purpose glass that is no longer available.
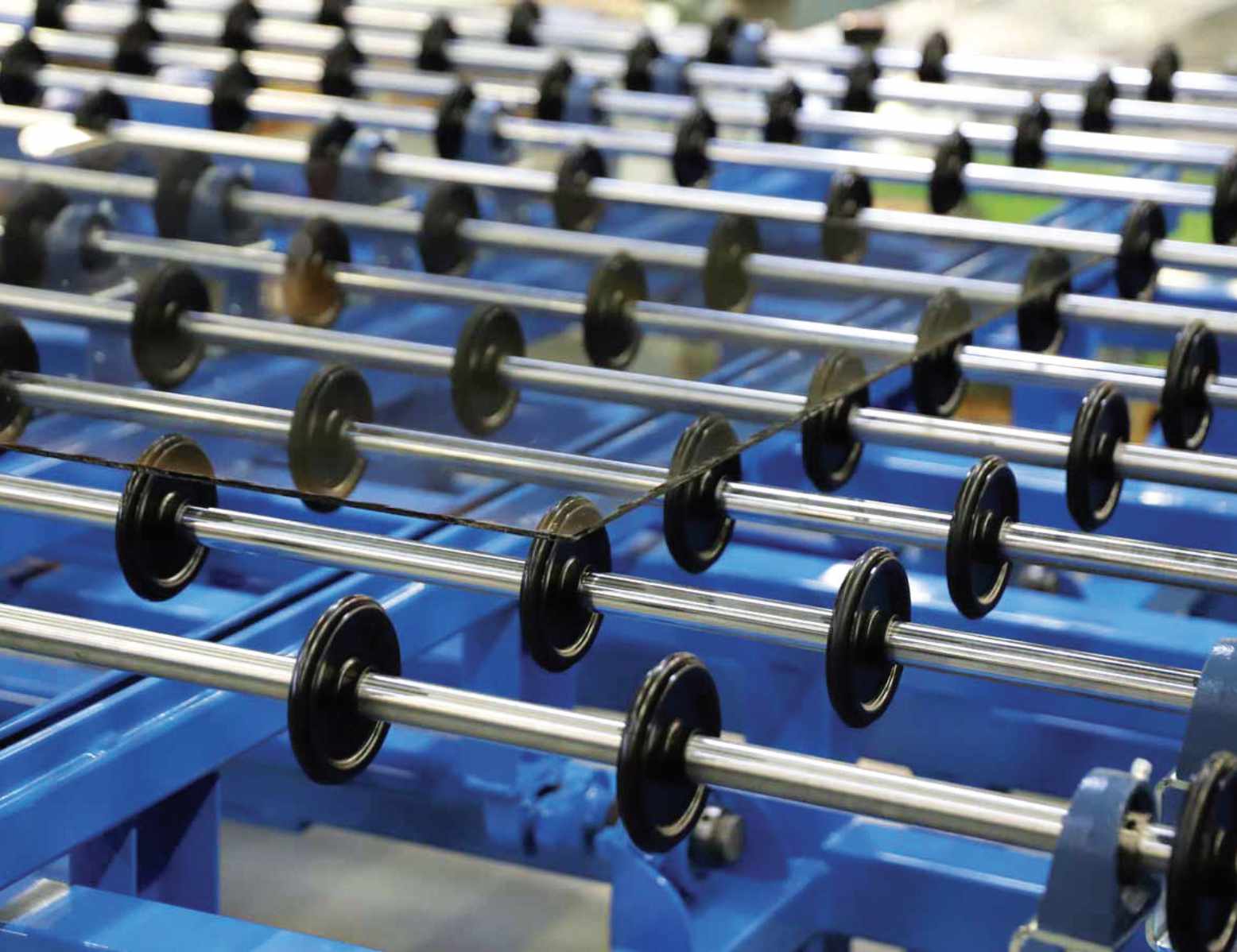
Once the pane has been removed from the insulated glass laminate, the IGU can either be reformed with the available glass or it can be used for other orders.
Three questions about separating insulated glass
Q: The separation of IGUs is a process that many glass processors have avoided until now, due to the time and effort involved. To what extent has the situation changed?
Dr Ostendarp: Automated separating technology will change the initial situation. Alongside higher productivity and safety, the separation quality is higher. This results in cleaner panes, while the spacers and their desiccant remain unaffected. As panes are becoming ever larger and the proportion of special-purpose glass is growing, the separation of insulated glass is becoming more financially attractive in and of itself. For a small glass unit with two single float panes, the cost and benefits must still be individually evaluated.
However, if it contains an LSG pane, a special coating or toughened glass, separation is increasingly attractive. This also applies if the repair of a unit involves an extra pane, which would result in longer delivery times or higher costs. Firstly, the effectiveness of the system depends on the cycle. Automated separation must be done so quickly that both the environment and the company’s budget will benefit. With the increase in carbon pricing, this ratio will continue to improve. Secondly, repairs or type-specific recycling saves carbon and contributes to achieving the climate goals.
Q: you emphasise the sustainability and resource conservation aspects. Would you explain these in more detail?
Dr Ostendarp: Climate protection goals are more relevant than ever.
There are now calls for tender in which concepts for recycling and improving the climate footprint are required. As a result, separating insulated glass can be very attractive for reasons of corporate image.
Further, recycling saves CO2 and reduces the costs of the CO2 certificate for float glass producers. Ultimately, the commitment must also pay, which can be reinforced by financial incentives.
Q: While the separation of insulated glass is not widespread, the topic is generating considerable interest. What do you expect for the future?
Dr Ostendarp: In the future, I can imagine that new interest groups will examine the issue. In some cases, IGUs will then be separated directly on the construction site. Suppliers and buyers will come together via software platforms. I also envision new glass products, including IGUs made from fully recyclable panes. In terms of energy prices, melting will become more attractive –the demand for type-specific shards for the float tank is already high today.

Carsten Koch
Email: carsten.koch@hegla.de
Website: www.hegla.com