Revolutionising Insulating Glass Production With Precision & Efficiency
Forel brings Thermoplastic spacer applicator to complete the range of solutions dedicated to the production of insulating glass.
First of all, a high-performance heated Graco pump ensures a continuous flow of material by feeding a storage reservoir, thereby facilitating uninterrupted extrusion even during drum changes.
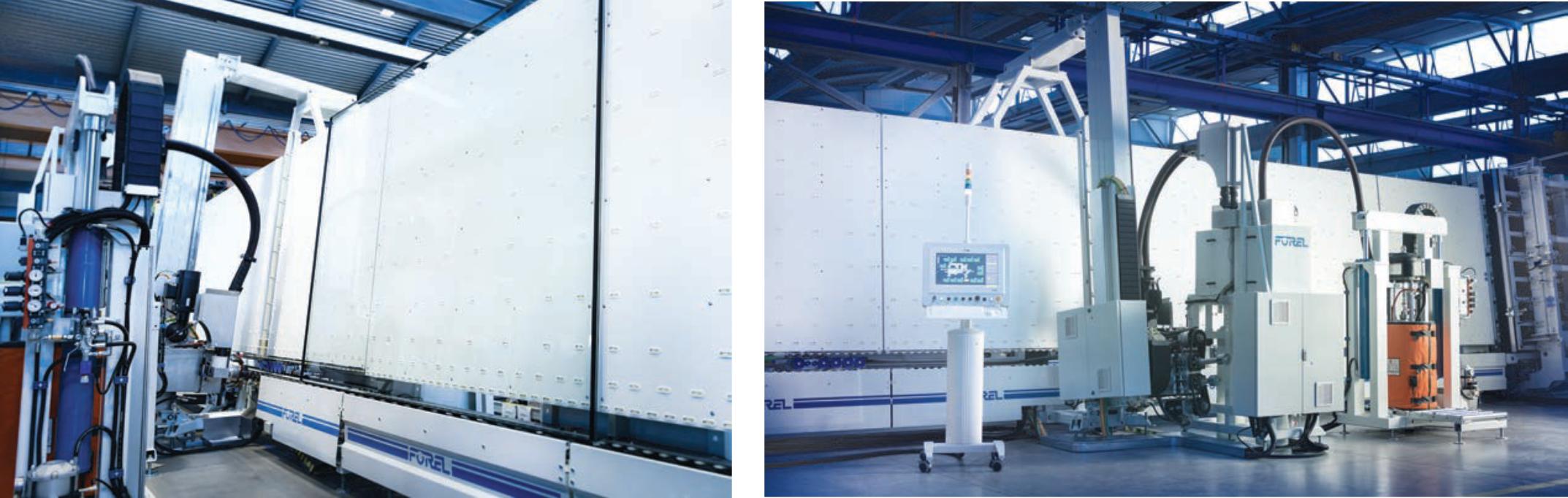
Also, a precise multipoint heated delivery system is implemented, maintaining the material at an optimal application temperature ranging from 120°C to 130°C. CNC-controlled application, with three-axis movement, allows for precise and programmable application patterns tailored to specific requirements.
Finally, the integration of a synchronized, dynamic suction cup mechanism ensures a controlled conveyance of the glass plates during the application process, enhancing precision and consistency.
Together, these elements form a sophisticated applicator system capable of delivering precise, high-quality application of Thermoplastic material onto glass plates, meeting the stringent standards of the industry.
The pumping system for thermoplastic employed by Forel is integral to the manufacturing process, ensuring precise and efficient application onto glass surfaces. Here’s an overview of its components and functionalities: The main Graco Pump System, with a robust 200-litre capacity stock, serves as the primary component, securely affixed to Forel’s pneumatic/hydraulic frame and barrel support structure. This system provides the necessary force to pump the thermoplastic material through the production line.
The heated thermal drum jacket, integrated directly into the machine, plays a crucial role in maintaining a consistent and optimal temperature for the thermoplastic material stored in barrels. This ensures smooth extrusion and application onto the glass plates.
At this stage, the main drum pump channels the Thermoplastic material directly into the onboard reservoir system, ensuring a continuous and steady supply during the production process.
Comprising two 7-litre cylindrical storage containers linked to a hydraulic pump, the reservoir pump system serves as a backup, providing a total reserve capacity of 14 litres. This setup allows for approximately 30 minutes of continuous material extrusion under typical operating conditions, ensuring uninterrupted workflow.
Characterised by precision and accuracy, the dosing system consists of two 0.6-litre cylindrical storage containers driven by servo motors.
This system precisely controls the volume of Thermoplastic material dispensed, ensuring consistent application onto the glass surfaces.
Directly connected to the application nozzle, it facilitates smooth and controlled material flow, resulting in high-quality finishes.
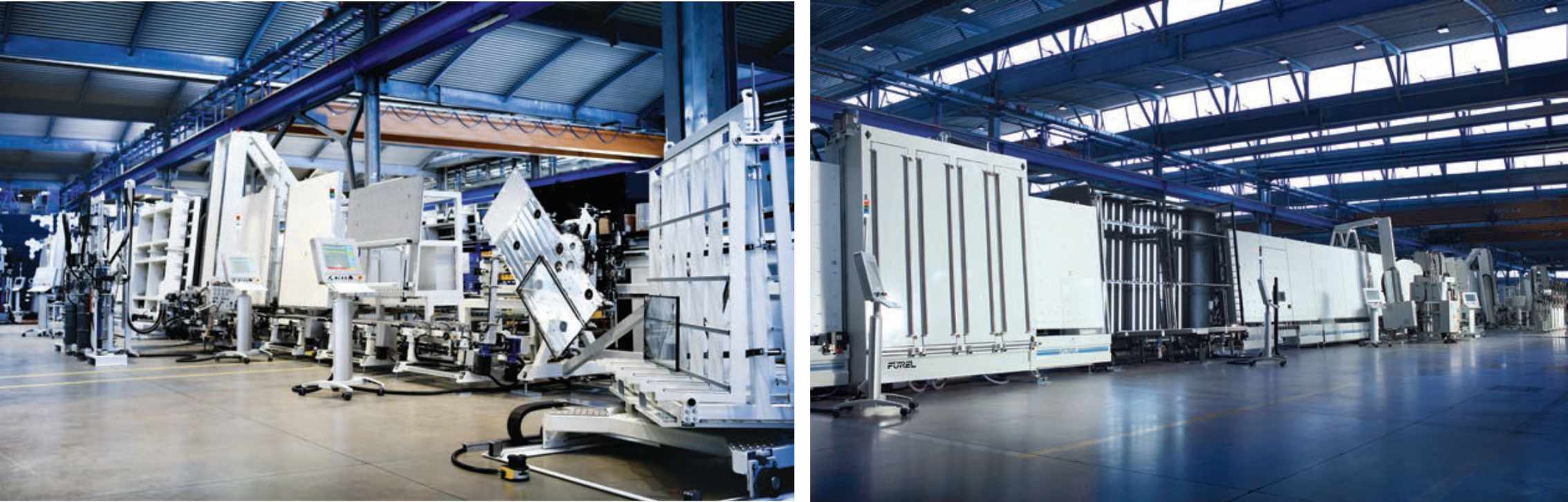
Achieving a hermetically sealed start and finish point for the spacer application is paramount to ensuring the high quality and durability of the thermoplastic Insulated Glass (IG) unit. Here are the key features and benefits of the sealing process: The joint closing process utilizes a well-established wedge joint method, ensuring a gas-tight seal that remains secure throughout the lifespan of the IG unit. This minimizes the loss of gas over time, contributing to its longevity and performance.
With no requirement for secondary touch-ups, the sealed joints maintain their integrity without the need for additional interventions. This reduces maintenance efforts and enhances operational efficiency.
The sealing process delivers consistent reliability and aesthetic appeal, with no tooling marks or inconsistencies. This results in a uniform and professional finish that meets stringent quality standards.
Versatility: The sealed joints can be positioned in corners or offset on edges, offering flexibility in design and application to suit various architectural requirements and preferences.
Moreover, the nozzle design enhances efficiency and assembly times: Material Reduction: Compared to typical standard nozzles, the nozzle design reduces material usage, optimizing resource utilization and minimizing waste. This contributes to cost savings and environmental sustainability.
Reduced Assembly Times: Assembly times are significantly reduced by over 20% compared to standard IGU equipment from Forel, thanks to the nozzle’s innovative design and improved efficiency.
Width and Radius Optimization: The nozzle widths and corner radius are optimized to improve sightlines and reduce the spacer profile height to 5.3 mm, enhancing the aesthetic appeal of the IG units while maintaining structural integrity.
Overall, the sealing process and nozzle design represent advancements in thermoplastic IG unit technology, offering improved performance, efficiency, and aesthetics for the flat glass and insulated glass industry.
For enquiries on Forel products in India, please write to Thorngate Sales Corp at sales@thorngate.in
Website: www.forelspa.com