Haigela glass factory, is located in Chengdu, Sichuan, covering an area of 8,000 sqm,daily output of tempered glass is 2,500sqm every 16 hours. The factory has high quality and high productivity to keep a high competitiveness in the market.
This marks another successful case for MAA-YUGONG in Sichuan, establishing one more benchmark in this region.
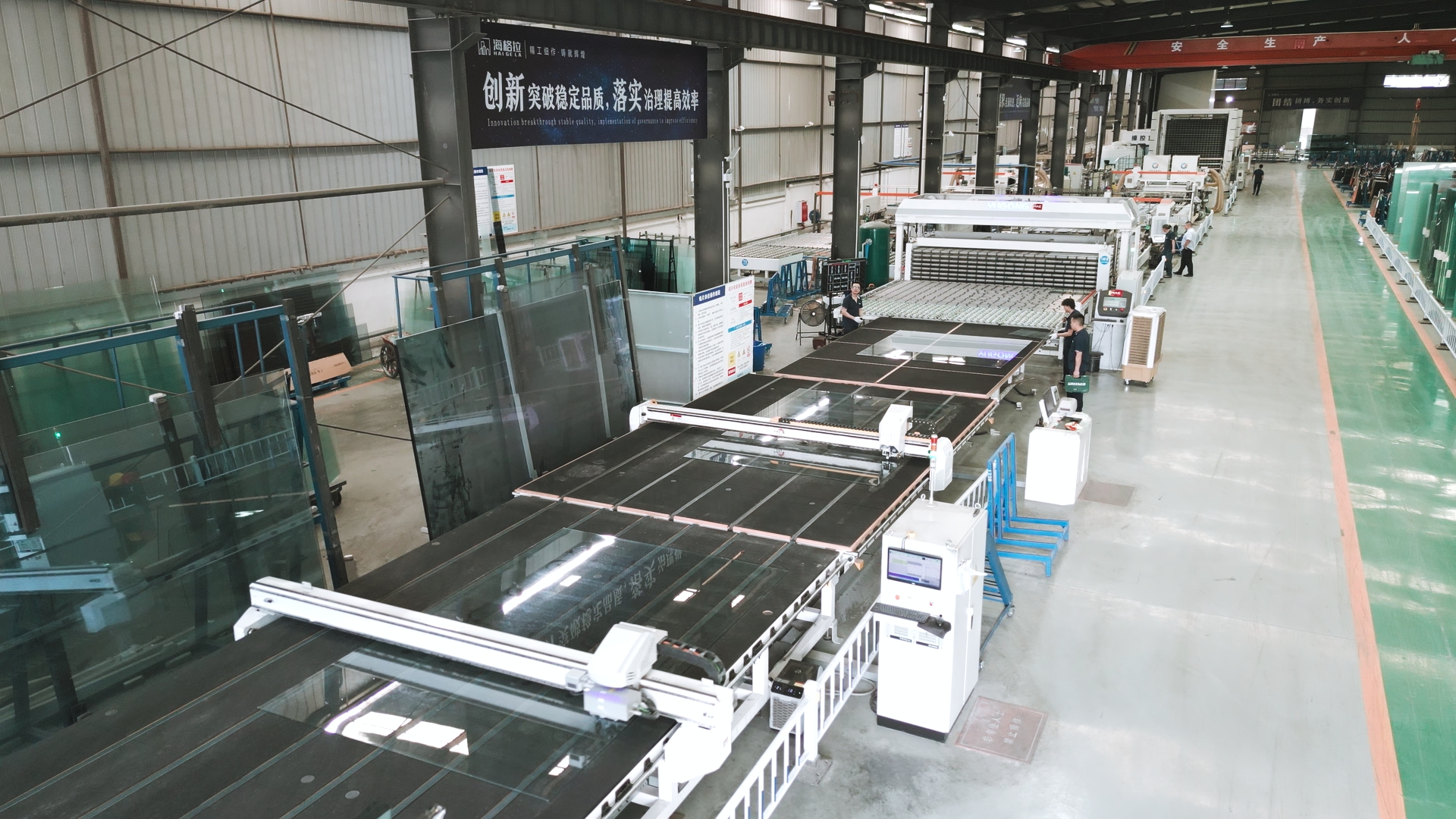
- an online cutting line and a laser marking,
- a 9 layers horizontal sorting system in between cutting and double edger,
- two double edgers,
- a 35 layers horizontal sorting system,
- a double chamber tempering furnace,
- two IG lines,
- a PVB lami line.
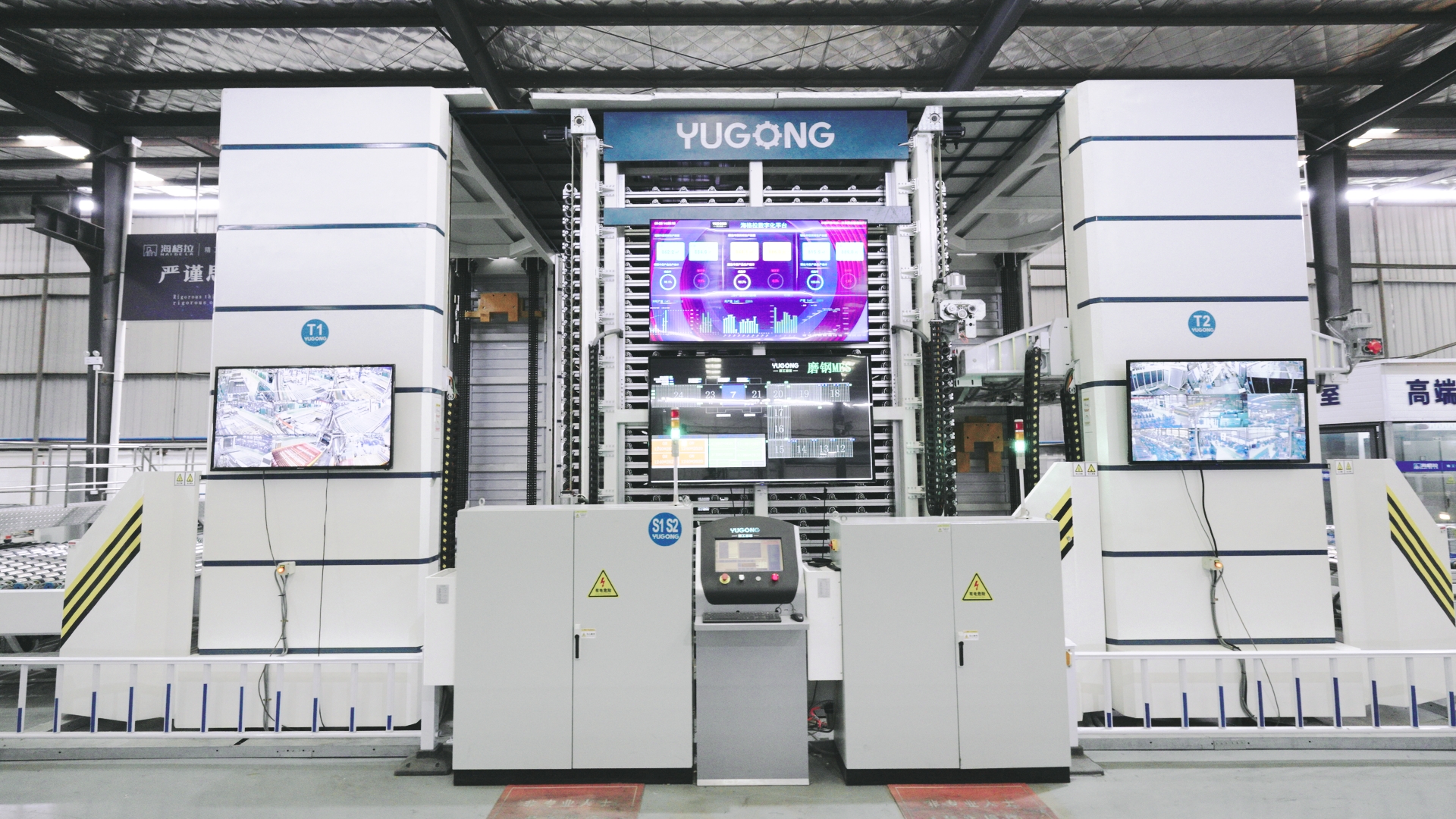
1. In software, MAC-YUGONG ERP generates optimization packages for cutting and laser marking machine. This innovation allows the optimization work to be completed in office, rather on cutting line.
2. Before cutting. The efficient Laser Marking assigns a unique ID to every glass, except QR code, it can also print 3C, logos, and other custom marking at any specified position according the orders.
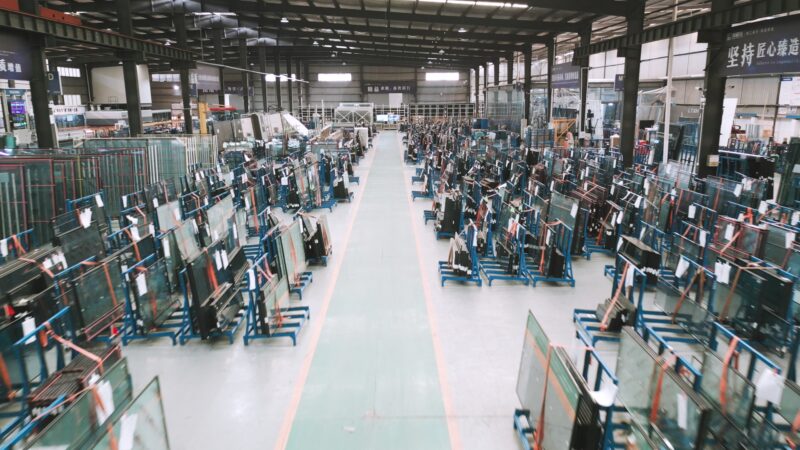
4. The 9 layer horizontal sorting system plays an important role to make a seamless connection between cutting line and edging machines. Especially, when a cutting line is connected to two double edgers, the glass moving flow will be managed by MAC-YUGONG MES, to achieve the best the production rhythm between cutting and edging process while adjust the edging sequence for optimize efficiency.
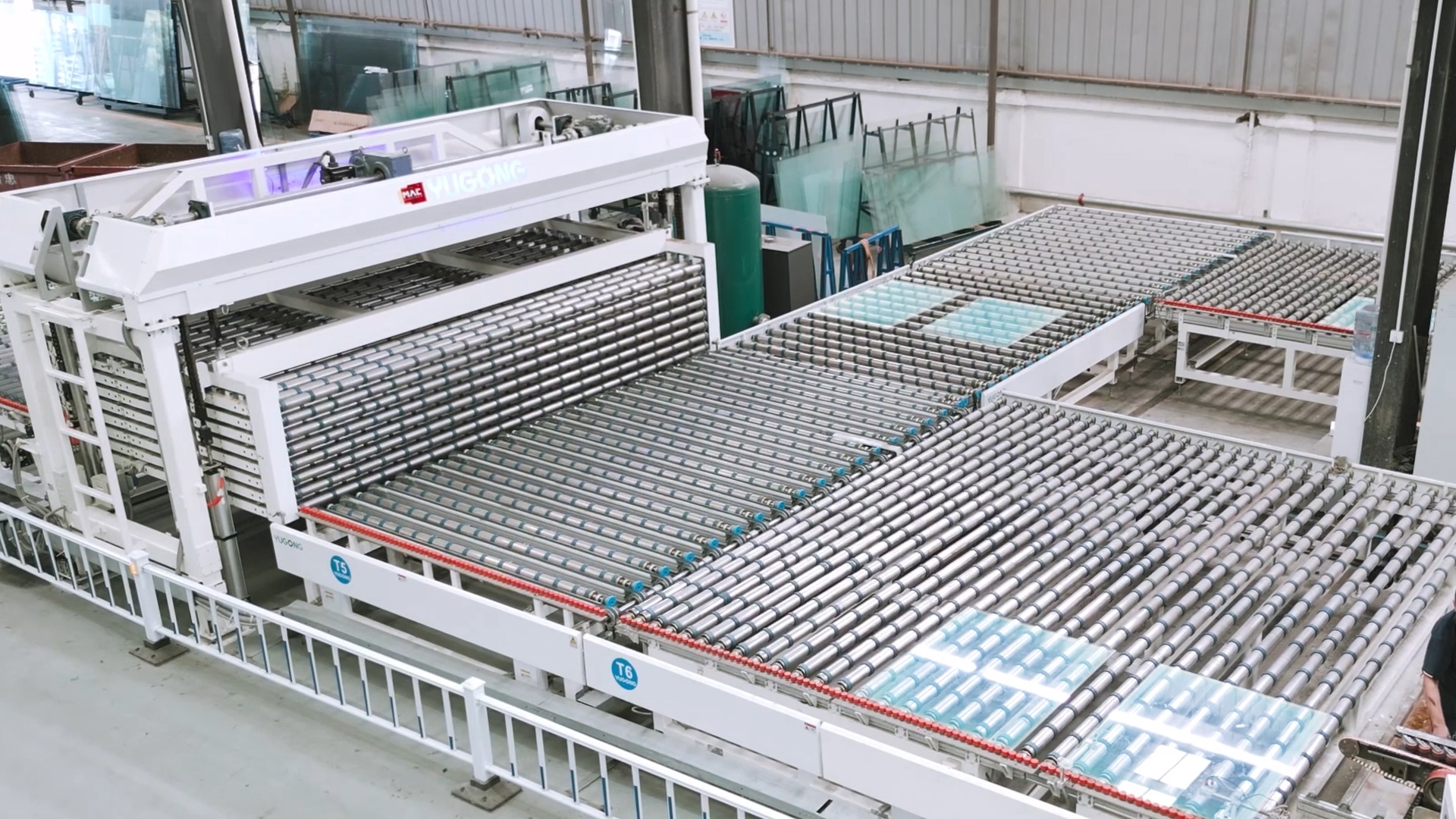
6. After edging is completed, the glasses are transferred through a 90-degree rotation table. Again, the smart MAC-YUGONG MES determines the rotation of glass based on its advanced algorithm. This ensures that the glasses are completed pre-batching before entering the horizontal sorting system.
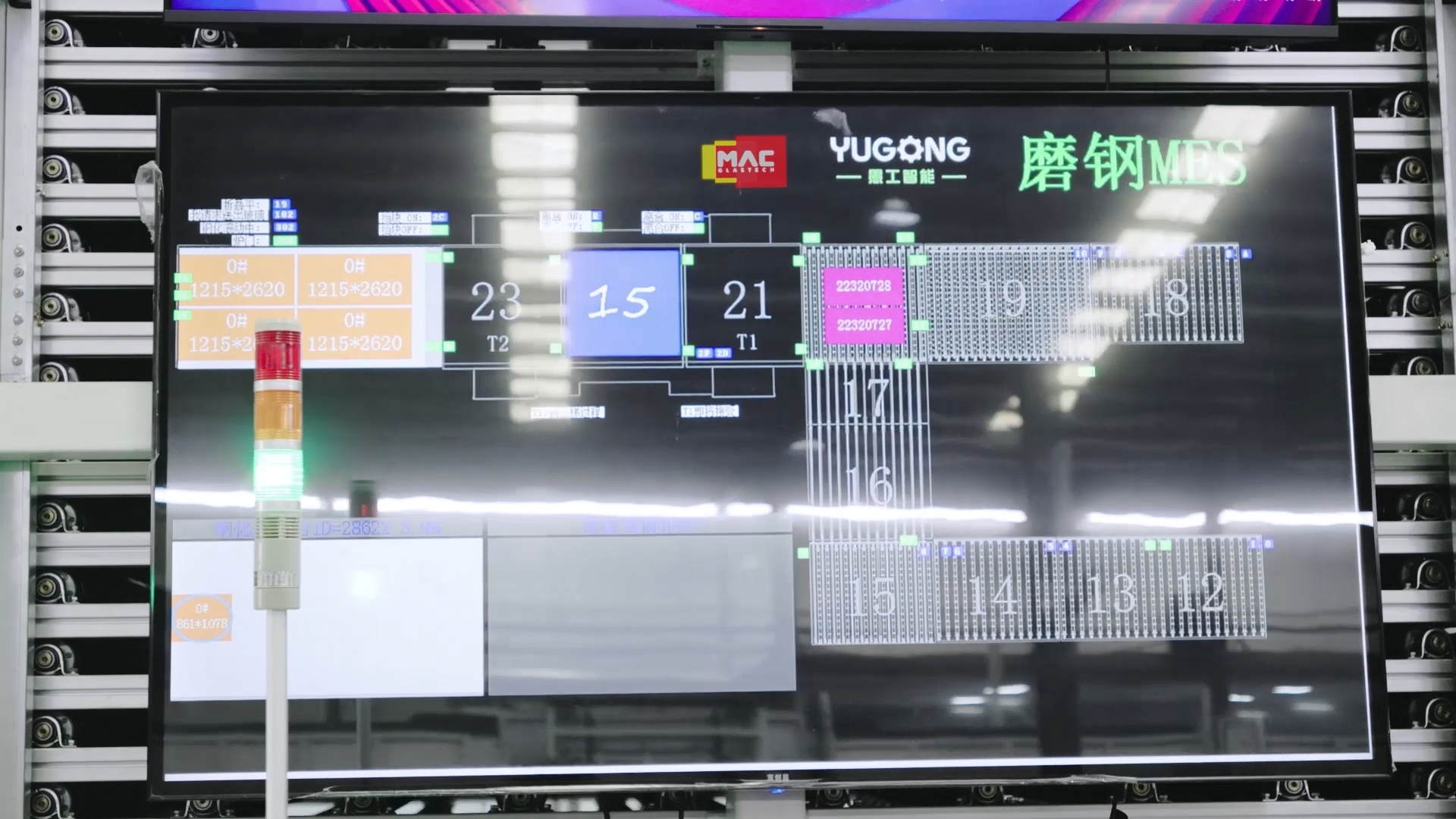
7. 35th floor horizontal sorting system takes. Enter stage
Lifter #1 transfers the glasses into the sorting system. Based on the glass size, multiple pieces can be stored on the same layer to achieve optimal storage efficiency. The glasses are precisely batched on X/Y/Z 3-dimensional table, following optimized patterns to maximize loading capacity for different sizes.
The final batching table organizes the glasses like a game of Tetris to achieve the highest loading efficiency. The logic behind this arrangement is determined by factors such as max tempering loading capacity or order priority or quality priority. MAC-YUGONG MES accurately calculates glass layout to achieve the best possible results.
8. After batching, the glasses transferred tempering furnace. Once tempered, each glass is scanned again by CCD before entering the Vertical Glass Sorting System. This ensures precise tracking and seamless transaction into the next step of production.
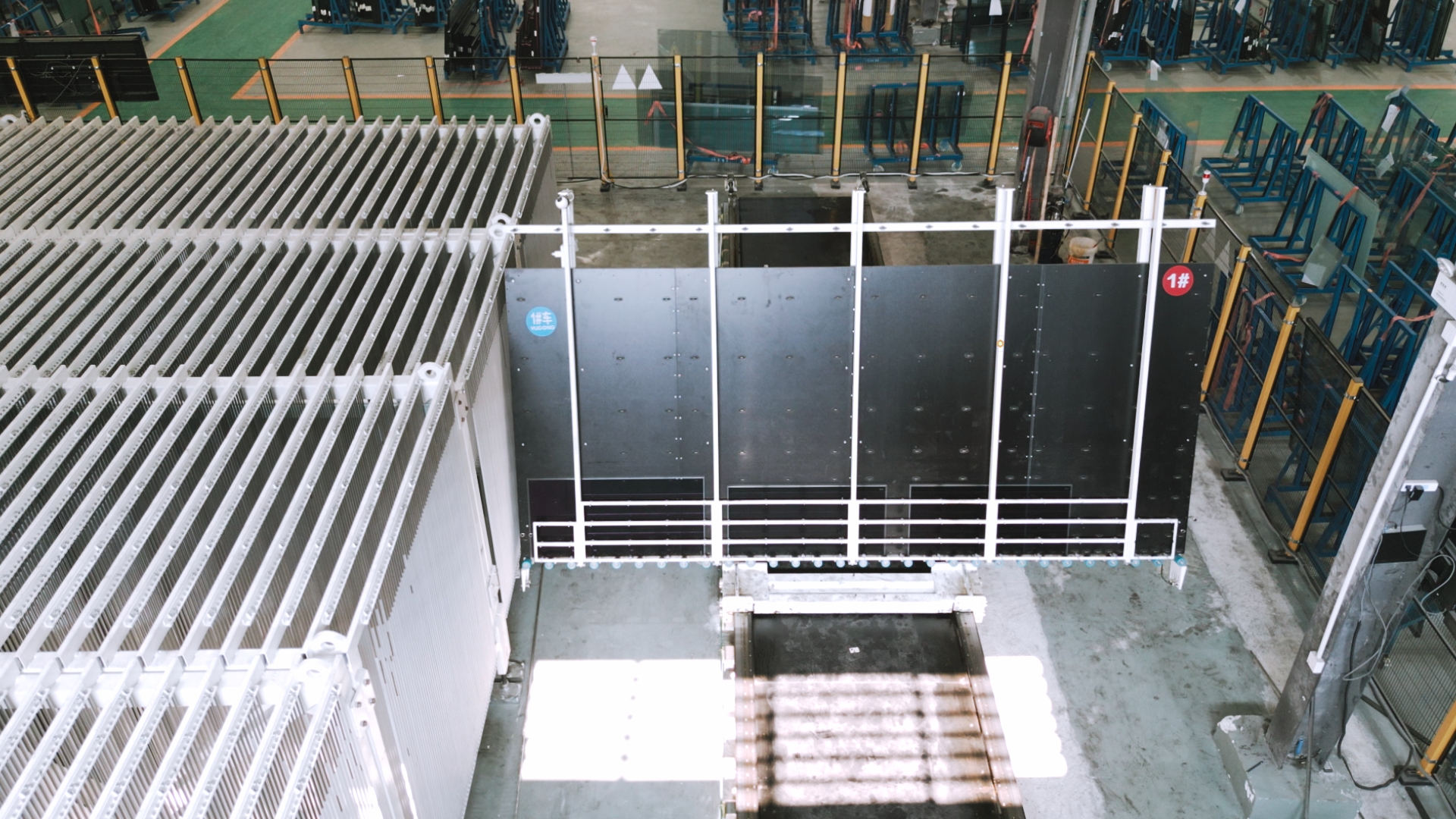
Vertical sorting system for IG line simplifies pairing process for Insulated Glass Units(IGU) and even Triple Glass Units (TGU) pairing. It eliminates the need for manually pairing A/B, A/B/C glasses, so that making IGU production much easier and efficient than the traditional model. This system supports flipping multiple glass sheets of different sizes at once, improving production efficiency. Bases on order requirements, MAC-YUGONG MES system assists in sorting glass in different slots and Each slot holds multi glasses, enhancing storage efficiency. The efficient and smooth shuttle conveying enhances the speed of IGU pairing.
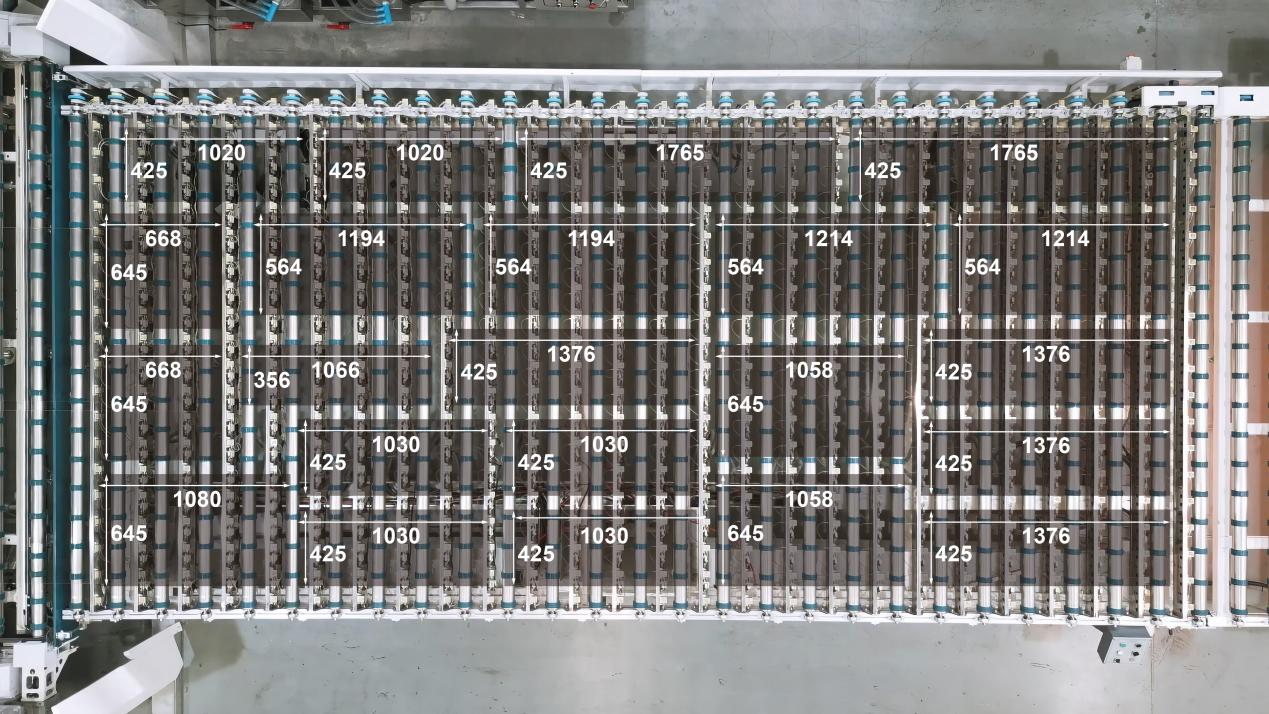
10. The 90-degree rotating conveyor efficiently transfers the paired glass panels into the IG line, ensuring a smooth and seamless conveyance process.
Now we can see that with MAC-YUGONG intelligent automation solution, the glass processing can be very different and transformed entirely. Not only collecting production data on time and accurately, but it also simplifies and secures the glass logistics. Thanks to the high automation level, the number of labors are reduced significantly across the entire factory.
In this factory setup, glass racks will be mainly for finished product rather than any middle stages. Laborers no longer need to manually carry glasses from one station to another, instead, they focus on monitoring the full production line.
MAC-YUGONG empowers every glass processor to achieve a more organized factory, efficient production , and a safer environment.