Convection Process Is Based On Radiation Heating, But It Was Not Known For Quite Some Time
In the end of 1980’s the most popular and famous tempering furnace was the HTF series of Tamglass Engineering Oy. It had a very accurate heating profile with C-C distance of heaters 120 mm.
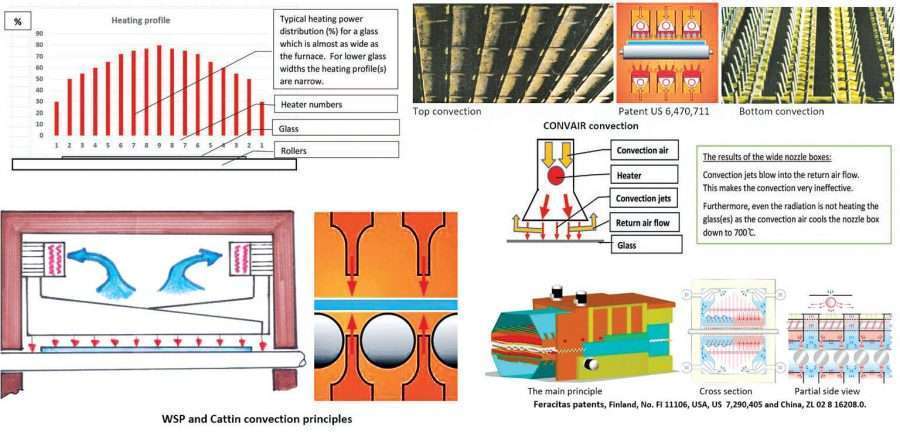
However, it had no matrix heating system. The heater lengths were as long as the heating length. Another alternative was that the heaters were divided into 3 lengths; longer in the middle of the furnace and shorter heaters at the ends. The heaters were difficult to change and also expensive.
Also a known problem in radiation heating was cooling of rollers with continuous loading of full batches. Also the rollers were too hot when the furnace was empty. This caused breaking of glasses in the furnace and other operational and glass quality problems. Teaching of radiation was forgotten Other known glass tempering machine manufacturers were English EFCO and Swiss Cattin. They already used short, open resistors so they had a matrix heating system. EFCO planned convection heating as low emissivity glasses entered into the market early 1990’s.
However, Cattin and German company WSP made convection furnaces. Cattin and WSP blew uniform temperature convection air onto the glass as the convection air heaters were before the blowers.
They did not have any heating profile and no matrix heating even for radiation. They did not maintain roller temperatures stable. Both were poor for all glass types, but had high heating speed. Simple things are difficult to realize, but simple ideas can make wonders, too.
Italian IANUA made the first effective convection process in 1996
Tamglass HTF (HTBS/HTS) technology was used for the machine. Also for control system. The convection air was blown “through” the heaters. This is why the heating control configuration of HTF was transferred into the convection air.
Another handicap of radiation heating was also avoided. The convection onto the rollers kept the roller temperature stable and the bottom glass temperature followed the top heating configuration.
The heating and the furnace were called “CONVAIR”, CONvection, and IRadiation. The fact is, that it included only slight radiation as the furnace temperature was below 700 °C.
The secrets of the high capacity are:
- heating of the convection air by the heaters,
- narrow nozzle boxes and
- some other little details
IANUA patented expensive and unnecessary things; nozzles machined into the radiation plates. IANUA should have patented how to heat the convection air by the heaters located all over the heating area. This alone would have made CONVAIR an unbeatable convection heating machine for over 20 years!
GLASSROBOTS RoboTemp experience:
Because of IANUA patenting mistake it was possible to copy CONVAIR. Minor differences were made. The idea was to make a really superior capacity furnace. That should have been possible with almost doubling the convection air volume. However, the capacity was finally almost the same as in CONVAIR. GLASSROBOTS had to add nozzles all over the top convection. This and narrow nozzle boxes made the design expensive.
A Chinese company experience of copying and modifying RoboTemp:
The company tried to make it cheaper by very wide nozzle blocks. They also installed nozzle boxes into the angle compared to the glass travel direction.
Other cost reduction method as shown below:
These systems do not meet low emissivity glass requirements since:
- The radiation matrix heating does not works for low emissivity glass
- They have very low capacity for low emissivity glass
- Their convection coverage is about 33% of the heating area and/or the convection is weak
However, for example the system shown on the right side has high capacity clear 5 mm glass, about 22 loads/hour. It is obtained by high radiation heating intensity of about 90 kW/m² of the heating area added with convection. For triple silver glass 5 mm glass the capacity is just 12 loads/hour.
The above systems just circulate convection air in the furnace but not heat it. This is the main reason for low capacity with low emissivity glasses. These systems really work like radiation heating furnaces. The radiation heating furnaces have lower yield and they have more glass quality problems like edge kink.
Another problem with this type of the furnaces is that the thermocouples are affected by the radiation, the return air flow of various matrixes, mix of the convection jets and the return air flow. This is why the thermocouples do not give the correct reading matrix by matrix as they should.
How the convection problems and expenses can be tackled?
Feracitas convection unit and its applications. Number of units depend on the heating length.
Comment A:
Box convection eliminates nozzle boxes and excessive ducting. Over dimensioning of heating power and convection blowers is not necessary when the convection return air flow is correctly arranged. The patent US 7 290 405 has expired but can be used. However, not with nozzle box convections.
Comment B:
The heaters are inside of the convection unit. In CONVAIR, RoboTemp and other good “pure convection” methods they are inside nozzle boxes.
Comment C:
The patent US 9,624,120 protects the idea for the return air space. A small under pressure at the top of the furnace sucks the return air flow through the return air space back to the blowers. It works according to the Bernoulli effect from the 16th century. The pressure loss is only 4 – 7 % and working range very large, secure. The benefits:
- The convection coverage can be 100% of the heating area and
- The convection jets do not hit into the return air flow
- These are the key factors to the effective heat transfer and high capacity.
The new patent applications
- FI 20200015 adds radiation into the convection heating. Convection heats the glass surface only. The radiation enters into the clear glass. This is why clear glass tempering and lamination should have radiation, too. Furthermore, the heater change is easy and manufacturing cost is lower.
- FI 20200035 is for annealing and continuous tempering furnaces. The heaters can be changed from outside of the furnace.
Notes:
- The process in all alternatives remains the same. Only the return air flow is different. Nothing is missed from comments A and C.
- Even comments A and C and the 2 patent applications can be combined into the same package. However, if the 2 patent applications are combined together, an extra cost applies.
- All the convection embodiments can be fitted into the same furnace body and software with minor changes in them.
The economic effects
The glass tempering can waste up to 80% labor wages when tempering 5 mm triple silver glass. This is due to the waiting time, which is needed for the glass to be hot enough to temper it. This waiting time is the biggest contributor to energy waste, too.
These wastes can only be reduced by high heating speed. In high labor cost countries this is huge money every year. In some countries energy cost savings are more important Naturally also investment cost and payback time are important.
All can be calculated by a simple EXCEL sheet by inserting local costs expenses and glasses divided into clear glass and triple silver glass. This is an example for 2 shift work in a high labor cost country. 2/3 of the glass is triple silver glass and 1/3 clear glass. Payback time is 7 years.
This does not include breakage, which is higher with the convection processes, which function like radiation heating furnaces. Also proper convection heating furnaces produce better quality glass.
About the Author
Risto Nikander, MD of Feracitas Oy, has 30 years’ experience in safety glass processing. He concentrated first in bending and tempering technology. Later, he involved himself in flat glass tempering and convection heating. His experience in convection heating covers almost all the time of the existence of low emissivity glasses. He has several patents in both technologies.
For More Information:
Email: feracitas@gmail.com
