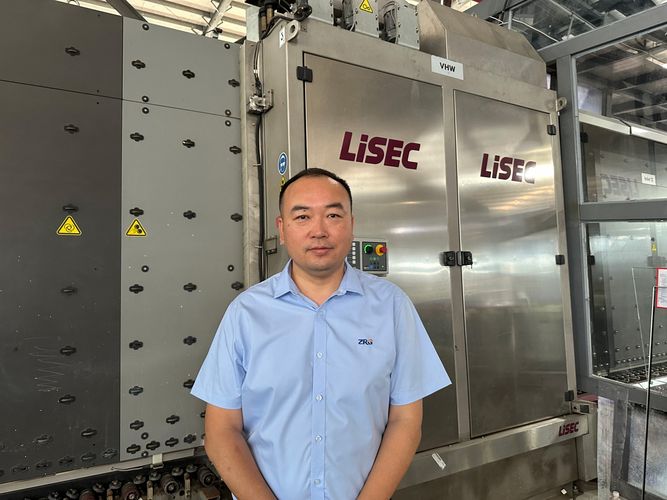
ZRG: Focus on quality and customer satisfaction
ZRG boasts a total annual production capacity of around 890,000 units, 70% of which are distributed across the Chinese market. ZRG caters to various product requirements within the Chinese market. Their product portfolio extends from insulating glass through digitally printed and fire-resistant glass to tempered and laminated glass.
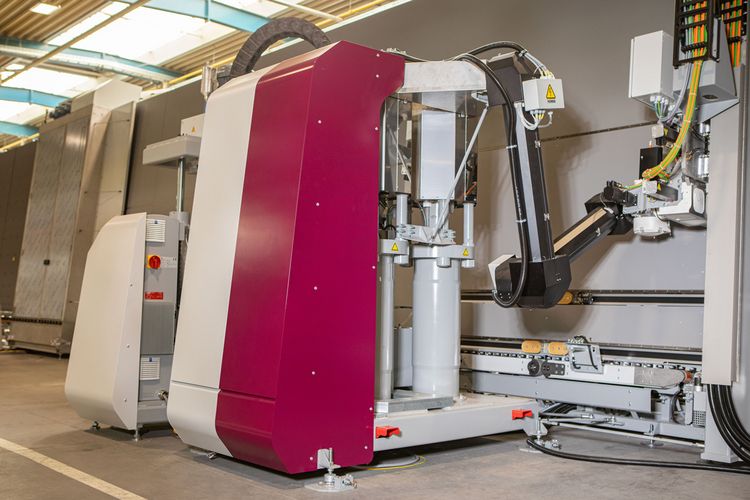
Partnership based on quality and trust: ZRG and LiSEC
Gao Jiang, Managing Director of ZRG, and Qiao Chi, LiSEC Head of HUB Region China, enjoy a long-standing business relationship centred on trust and the development of joint solutions. The Chinese company has been reaping the benefits of LiSEC machines since its first investment in a LiSEC machine in 2018.
“The higher level of development and superior quality that LiSEC’s machines produce in the individual process steps was the decisive factor in our partnership with LiSEC, says Gao Jiang.”
“There is also a competent team on site, something that shouldn’t be underestimated. In the same way that we have to respond flexibly to customer requests – sometimes even after planning has been finalised – to satisfy our customers, we also expect the same from our suppliers. Throughout the years of our collaboration, LiSEC has convinced us that they are always on hand with help and advice for service requests and take our problems seriously. We recognise how hard the LiSEC team works to resolve all our concerns and the level of seriousness and focus with which they approach the matter.”
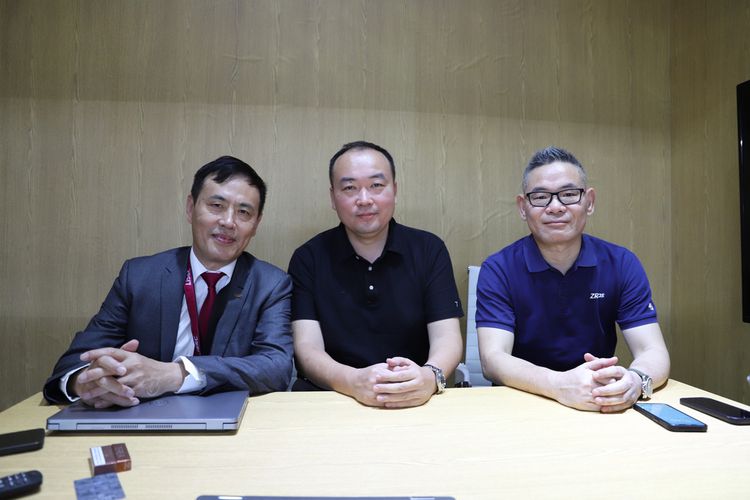
Competitive benefits through flexibility and quality: ZRG relies on LiSEC technology
The Chinese market is extremely sensitive to price and highly competitive. Two key competitive advantages in addition to quality are short delivery times plus the aforementioned flexibility in planning. If you have the ability to change plans at short notice to suit the customer thanks to your own production facilities and can offer both short delivery times and exceptional quality, you are one step ahead. This also means, however, that the low price elasticity on the Chinese market requires expensive investments such as a LiSEC machine to run stably and efficiently to ensure that the costs incurred pay off.
Managing Director Gao Jiang at LiSEC is convinced of this return on investment: “We took a close look at the machines and the manufacturing process in advance, not just at trade fairs in Düsseldorf, but also directly at the Austrian plant and even live with other customers. The LiSEC machines certainly deliver what they promise. The fact that LiSEC is able to supply everything from a single source and that you only have one point of contact naturally also makes LiSEC interesting in the future which was one of the factors that prompted us to invest in a new LiSEC machine this year: An insulating glass line for thermoplastic spacers. LiSEC also maintains a good reputation in our market, meaning that our customers also see processing on LiSEC machines as a major USP!”
Marketing Manager Wu Lin anticipates a future trend in the constantly improving quality of the sheets on offer in the low price segment. Good finishing of the sheets is becoming increasingly important. The LiSEC TPA insulating glass line will continue to safeguard the company’s positioning, the gentlemen at ZRG agree.
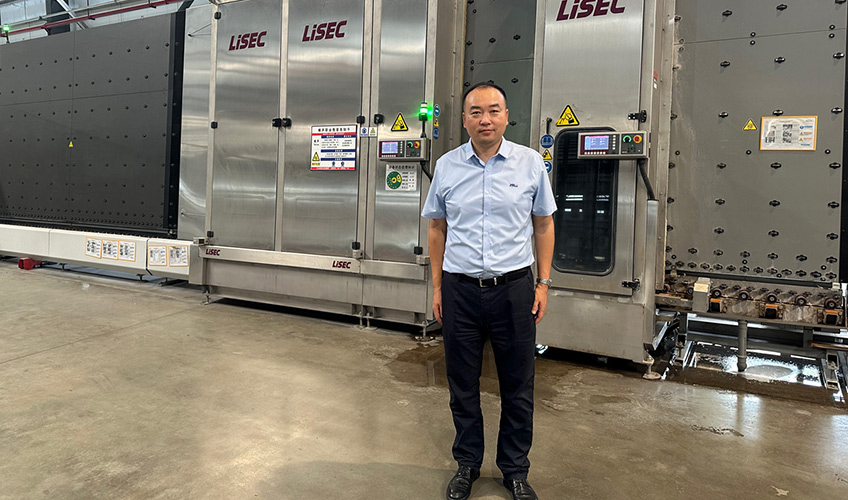
As a modern glass processing company boasting production facilities meeting the highest technical standards and covering a total area of more than 100,000 square metres, ZRG has four production sites, of which three are situated in Guangdong Province (two in Foshan, one in Zhaoqing) and the fourth in Hainan Province (Haikou), with approximately 360 employees.
A LiSEC PKL glass storage unit and a LiSEC SBL are used in production. The unique feature of this glass storage unit lies in the design of the glass supports, which allows two sheets to be lifted down at the same time using the suction bridge. This means that not only jumbo sheets can be fed into the LiSEC ATL, but in particular split sizes, since these are very frequently used on the Chinese market.
There is also a LiSEC GFB as well as a manual breakout table in the production halls of ZRG: this is where an operator breaks out the sheets, then pushes them over an air cushion table onto a positioning table and finally on to the LiSEC KSR+KSV seaming system (belt seaming) in the direction of the tilting table.
Following the LiSEC KSR and KSV, the sheets are washed by a LiSEC VHW and are then conveyed to a compact ASM sorting system with input and output transport shuttle and 4-slot storage magazine (4 boxes). A tempering oven is connected after outfeed from the sorting. The sheets come out of the sorting process in hardening sequence and are moved from the vertical to the horizontal position with a tilting table. After the tilting table, an operator removes the sheets from two air cushion tables with belts and transports them to the tempering oven infeed.
There is also a flexible sorting and buffer system at the start of the 2.50 m x 2 m insulating glass line for the fully automatic storage and retrieval of glass sheets (BFS). The sheets are placed in the inlet, the storage unit moves and the loaded sheets are retrieved from the insulating glass line in a sequence optimised for production as soon as the storage unit is fully loaded.
The insulating glass line for rigid spacers has a LiSEC VHW washing machine, a LiSEC frame mounting station, a LiSEC FPS-U 2 press and a LiSEC VL-1N sealer.
The new investment: a LiSEC TPA insulating glass line
ZRG has invested in a new 6.5 metre long LiSEC insulating glass line for thermoplastic spacers as a supplement to its insulating glass line for rigid spacers. This takes the fed-in sheets to the LiSEC washing machine. An inspection zone then follows, which could also be used as a frame mounting station for frames with a maximum dimension of up to 3.80 metres. The screen is normally inspected for quality in the inspection zone. Following this inspection station is the TPA applicator with corner seal and the LiSEC FPS-A press as well as a calibration unit for the TPA units, allowing the overpressure in the sheet to escape. The sheets are then sealed with LiSEC VFL 1F sealant for max. 6.5 m sheets.