How do I reduce my CO2 footprint as a manufacturing company? The industry working group Research & Technology conveyed various approaches that can also be implemented in glass machinery manufacturing.
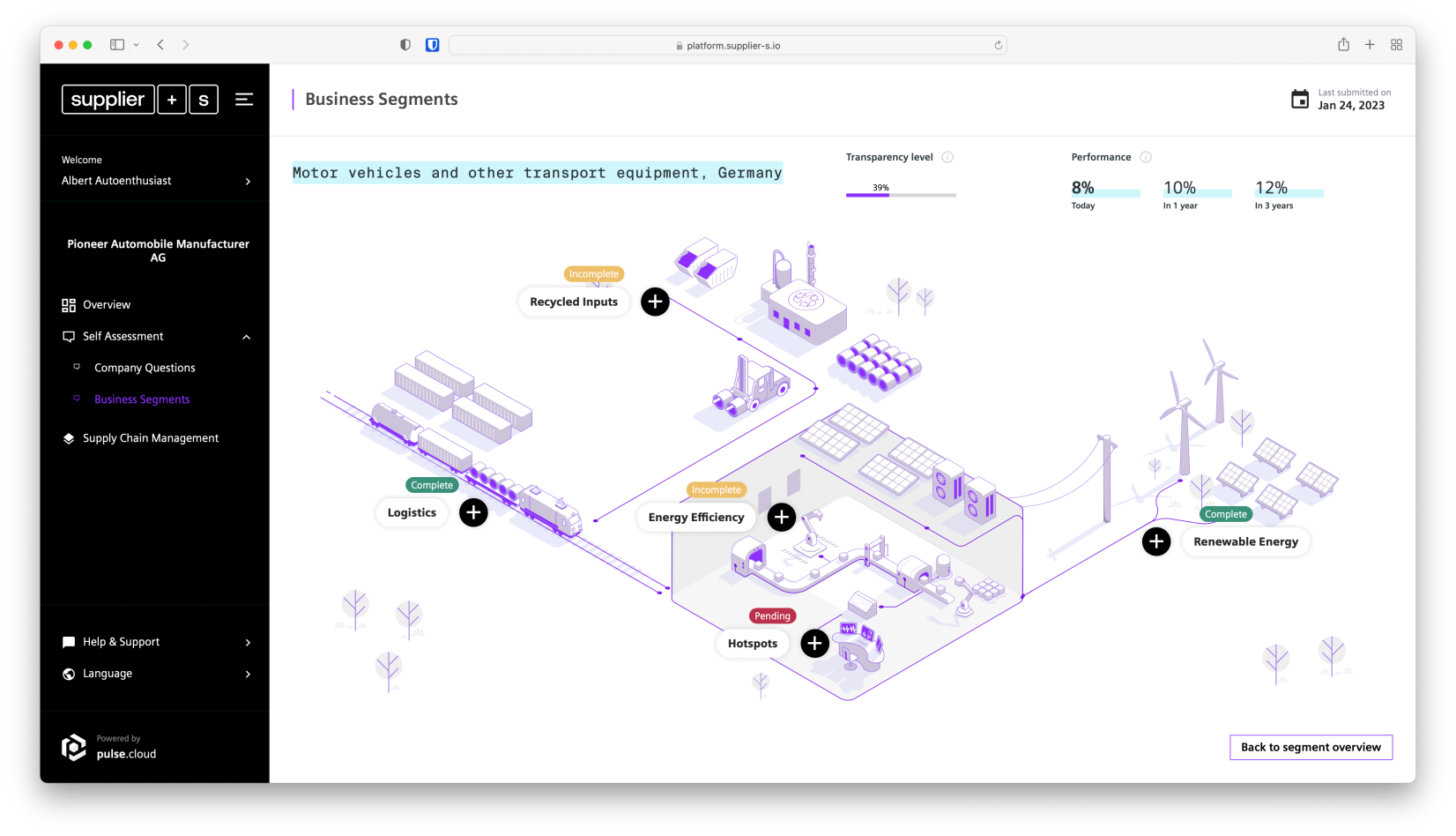
According to the Greenhouse Gas Protocol – a recognised international standard for accounting and reporting greenhouse gas emissions – reporting for companies distinguishes between direct emissions from own combustion (Scope 1), indirect emissions from the purchase of grid-bound energy (Scope2) and other indirect emissions from processes and products caused directly or indirectly by the company (Scope 3).
More transparency via software
Not only the company’s own production, but also the climate footprint of its suppliers plays a decisive role (Scope 3) – especially with regard to the European Supply Chain Act. Siemens AG, a global corporation with 66,000 suppliers in 145 countries, is mastering this challenge with a software tool that Siemens developed together with the company ctrl+s. Suppliers go through an assessment that influences the company’s purchasing decision. By 2030, Siemens wants to reduce its upstream CO2 footprint (Scope 3) by 20 per cent and be climate neutral by 2050. The aim is not only to evaluate primary data supplied by suppliers, but also to make suggestions to the supplying business partners as to what steps they can take to improve their own CO2 footprint.
Two years ago, Siemens launched the carbon-reduction@suppliers programme. With the help of the Carbon Web Assessment Tool – now renamed “supplier+s” – Siemens asks its suppliers about categories ranging from energy efficiency, green electricity, economic options for low-carbon electricity and low-carbon heating and cooling, energy-efficient processes, logistics and the use of recycled products to business travel. Suppliers can enter both current values and target values for subsequent years. The system calculates an overall rating in percent from the individual entries and shows the deviation from the industry average. Since not every supplier already knows his processes so well that he could provide detailed information on them, the tool allows adjustments and updates at any time. The system uses model graphics, for example, to illustrate where further optimisation possibilities exist are and provides suggestions. In this way, it helps companies to continuously improve their carbon footprint and develop a Net Zero strategy. Siemens makes the assessment tool available to its suppliers free of charge.
To enable other companies to manage emissions in their own supply chain, Siemens transferred the rights to the company ctrl+s at the beginning of 2023, which now offers “supplier+s” on the market.
Picture: ctrl+s
Reduce the power consumption of machine tools
In the production of parts with machine tools – also in glass machine manufacturing – the focus is increasingly on electrical energy consumption according to Siemens Digital Industries. Not only because the associated CO2 emissions have a negative impact on the manufactured components. The rising costs of electrical energy are also making the production process more expensive. Reason enough to take a closer look at the savings potential here. The focus here is on the auxiliary units of the machines. According to a study by the Technical University of Darmstadt, these account for 80 per cent of the energy consumption over the life cycle of the machine. Therefore, the automatic shutdown of the auxiliary units during breaks already brings noticeable energy savings. Adjusting the speed of the auxiliary units to the respective machining situation by means of a frequency converter is another important lever. Finally, all measures to avoid “non-cutting” times of the machines – in addition to maximising productivity – also automatically lead to minimising the consumption of electrical energy. Digital twins for the “offline” creation of CNC programmes or features for quick machine set-up are thus further adjusting screws. The decisive prerequisite for taking concrete measures is not least the visualisation of energy consumption.
With direct current to climate neutrality
Making production plants more energy-efficient and CO2-neutral is another building block for a successful energy transition. DC grids enable a technological leap towards climate neutrality, resource conservation and grid stability. The latter is essential to ensure a reliable energy supply, even when using renewable energies. Factory-internal DC grids can compensate for their fluctuations, absorb peak loads and make energy generated in-house from renewable sources available with a time delay.
Weidmüller Interface GmbH & Co. KG was a partner in a cooperation project with 35 companies that looked at the possibilities of using DC technologies. The company offers system specifications as well as components and solutions for the construction and operation of DC networks.
So, what does it mean to set up such a grid? The energy supplier continues to supply the company with energy in AC technology, which is converted into DC at the transfer point in the production plant. Adjustments are necessary for feeding in the energy, for switchgear technologies and protection concepts as well as some other components. Then an energy bus routes the transformed energy on to the consumers such as machines, vehicles or the technical equipment in the building. For years, some machines, for example injection moulding machines, have already been operating internally with DC technology. Furthermore, in-house systems for energy generation and storage can be integrated more easily (for example photovoltaic systems or battery storage). This automatically reduces the power that has to be fed into the grid from the energy supply company for production. Other advantages are that valuable copper is saved, and the cross-section of the cables is reduced. Since the company can decouple itself from the disposal company, the internal network is much more robust and stable, storage systems provide the balance and dealing with EMC becomes easier.
VDMA guideline as a practical guide
The VDMA supports companies on their way to climate neutrality. The practical guide “Climate-neutral production – recommendations for action for mechanical and plant engineering” is available from the association (available in German language). It describes in eight steps how companies can basically achieve climate neutrality. The starting point is first the Corporate Carbon Footprint (CCF), which illuminates the current situation.
Based on this, planning and adjustment of future emissions takes place by investing in more energy-efficient production facilities. At the same time, a switch in supply from renewable energy sources can take place. In the long term, it is important to map the transparency of the CO2 footprint in the entire supply and value chain (Scope3 – emissions). In the future, the digital product passport will store all information on the life cycle of a product so that customers and end consumers can retrieve and understand the production conditions. The VDMA has developed a guideline for determining the PCF, which is currently in the consultation phase.
For more information, visit www.vdma.org.
Important links:
https://vdma.org/glass-technology
Do you have any questions? Gesine Bergmann, Glass Technology Forum,
Phone +49 69 6603 1259, gesine.bergmann@vdma.org, will be happy to answer them.
Press contact: Martina Scherbel, martina.scherbel@vdma.org, +49 69 6603 1257
The VDMA represents more than 3,600 German and European mechanical and plant engineering companies. The industry stands for innovation, export orientation and SMEs. The companies employ around 3 million people in the EU-27, more than 1.2 million of them in Germany alone. This makes mechanical and plant engineering the largest employer among the capital goods industries, both in the EU-27 and in Germany. In the European Union, it represents a turnover volume of an estimated 860 billion euros. Around 80 percent of the machinery sold in the EU comes from a manufacturing plant in the domestic market.
