Glimpse Into What The Globally Renowned Glass Processing Technology Company Is Bringing To Milan
For Glaston, it is time to focus on energy efficiency, quality and automation with every piece of glass processed
In flat glass tempering – AI and automation
Glaston is developing advanced heating and cooling technologies for the best glass quality, outstanding energy efficiency and reliable automation. Its tempering lines with advanced heating control make it possible to increase loading efficiency and decrease energy consumption without sacrificing quality. With the latest technology solutions, quenching energy can even be optimized.
Glaston FC Series EVO, the newest addition to the FC Series family, represents a smart, energyefficient and flexible solution for today’s developing glass market. FC Series features the most advanced circulated-air convection technology to process any glass type with the highest energy efficiency on the market.
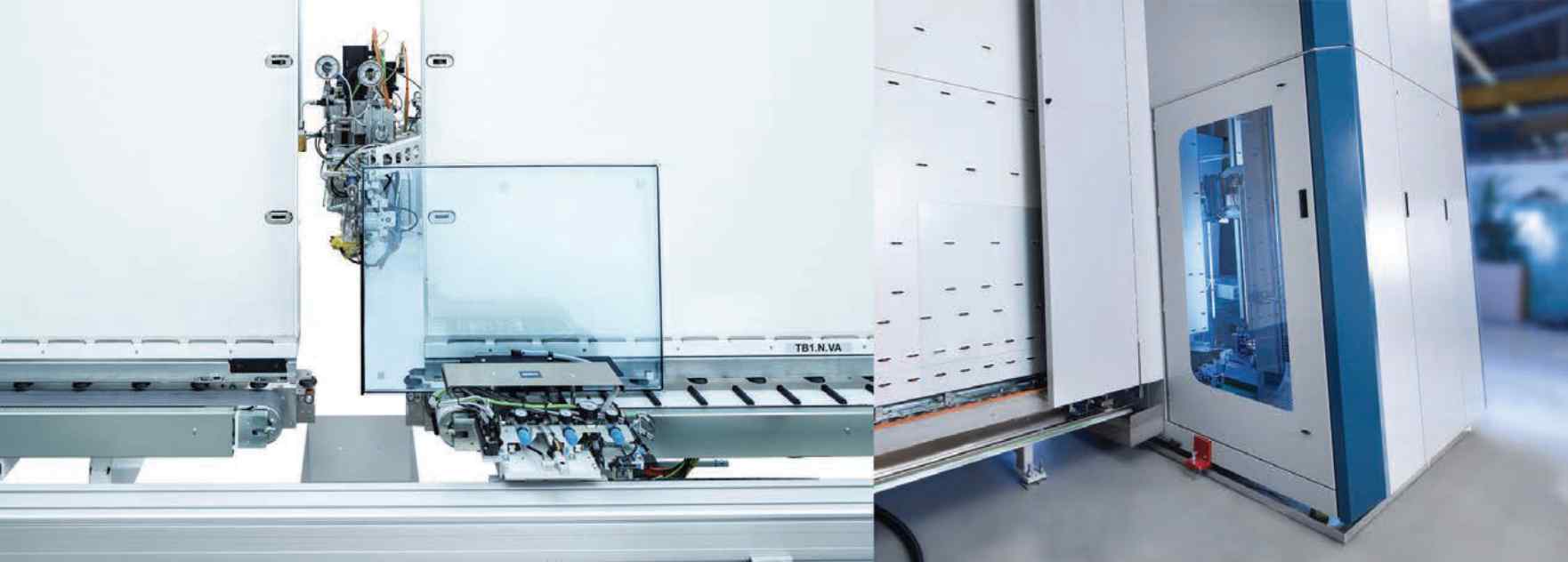
Glaston Autopilot reduces the need for operator input and offers process control without parameters.
The tempering process autopilot automatically sets all necessary parameters based on the glass sheet placement on the line. Minimizing operator input to just selecting the correct thickness and glass type significantly decreases the probability of human error, time spent on training and overall costs.
The online stress calculation solution is one of Glaston’s latest innovations to automate flat tempering.
It uses measured process data to calculate temperature and stress distribution in the quenching part of the tempering process.
The White Haze Scanner is the first AI-based solution to provide a high-quality visual indication of white haze on processed glass. The unique system instantly notifies users of an issue, allowing glass processors to react immediately when an unacceptable haze is detected.

The Glaston ProL flat glass lamination line provides unprecedented flexibility for mixed production. The ProL convection heating chamber makes switching between glass types and different glass sandwiches easier than ever. The whole line – from glass handling to the latest PVB cutting technology – has been designed for flexible operations.
The most recent trend in flat lamination is the growing use of structural interlayers. To process this type of glass, Glaston has introduced new convection control technology that offers a significantly wider operating window, even with complex laminates.
A higher degree of automation is also on the agenda for the laminating process. With our lamination process autopilot, the furnace learns to achieve the most optimal way to run, instead of having operators make adjustments manually.
The easiest way to save energy when laminating glass is to upgrade from a traditional infrared heater furnace to full convection technology. Energy losses are minimized, as the same air is recirculated inside the furnace. The right amount of energy stabilizes the furnace temperature. Processors often report energy savings of at least 50% after a heating technology upgrade.
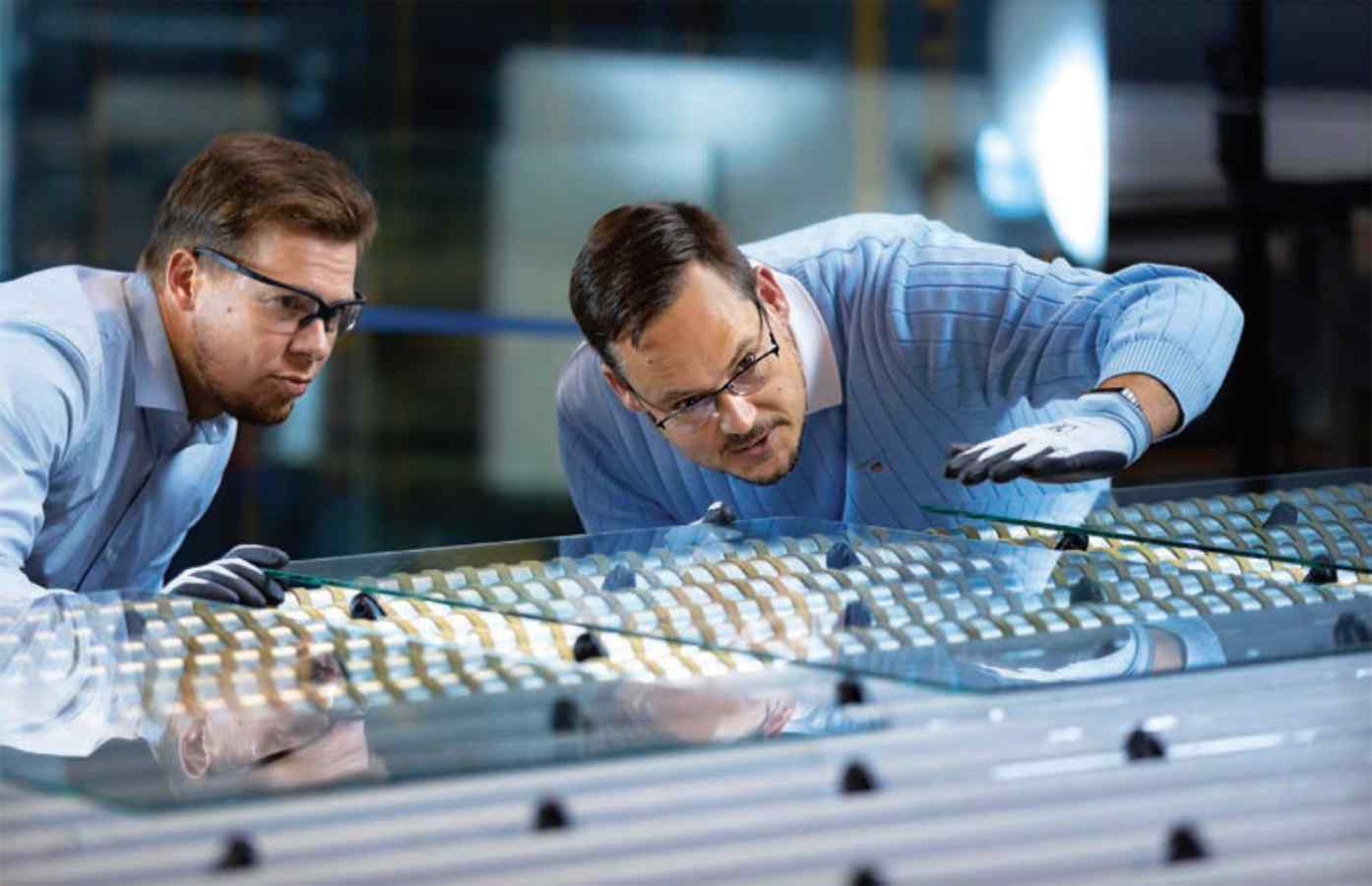
Glaston‘s new automatic sealing robot ACTIVE‘SEALER is an ideal entry-level solution for the automated sealing process. Thanks to the advanced gear pump dosing technology, ACTIVE‘SEALER offers high material dosing accuracy. This volume-controlled dosing function precisely determines the sealing depth and width and then applies the exact amount of sealing material required, ensuring excellent sealing quality. Targeting the mid-range market segment, the new ACTIVE’SEALER processes double and triple glass units.
The sealing robot features air cushions and a new conveyor system, consisting of individual belts with integrated and easily exchangeable support bars for safe and clean glass transport.
Glaston MULTI’ARRISSER is a 3-in-1 solution for the highest quality, economical glass edge arrissing, flat edge arrissing and corner dubbing.
These benefits come with the proven Glaston cup wheel technology that uses only one worn part. Glaston MULTI’ARRISSER is the fastest single-head machine in the world with a maximum arrissing speed of 60 m/ min.
TPS® is not just a machine. It is an ingenious system solution for highly efficient insulating glass manufacturing. Glaston is the inventor of this technology with more than 150 installations worldwide. With TPS®, production is significantly simplified, since the Thermo Plastic Spacer material can be applied directly onto the glass plate. This eliminates the need to stock different spacer profiles and connectors.
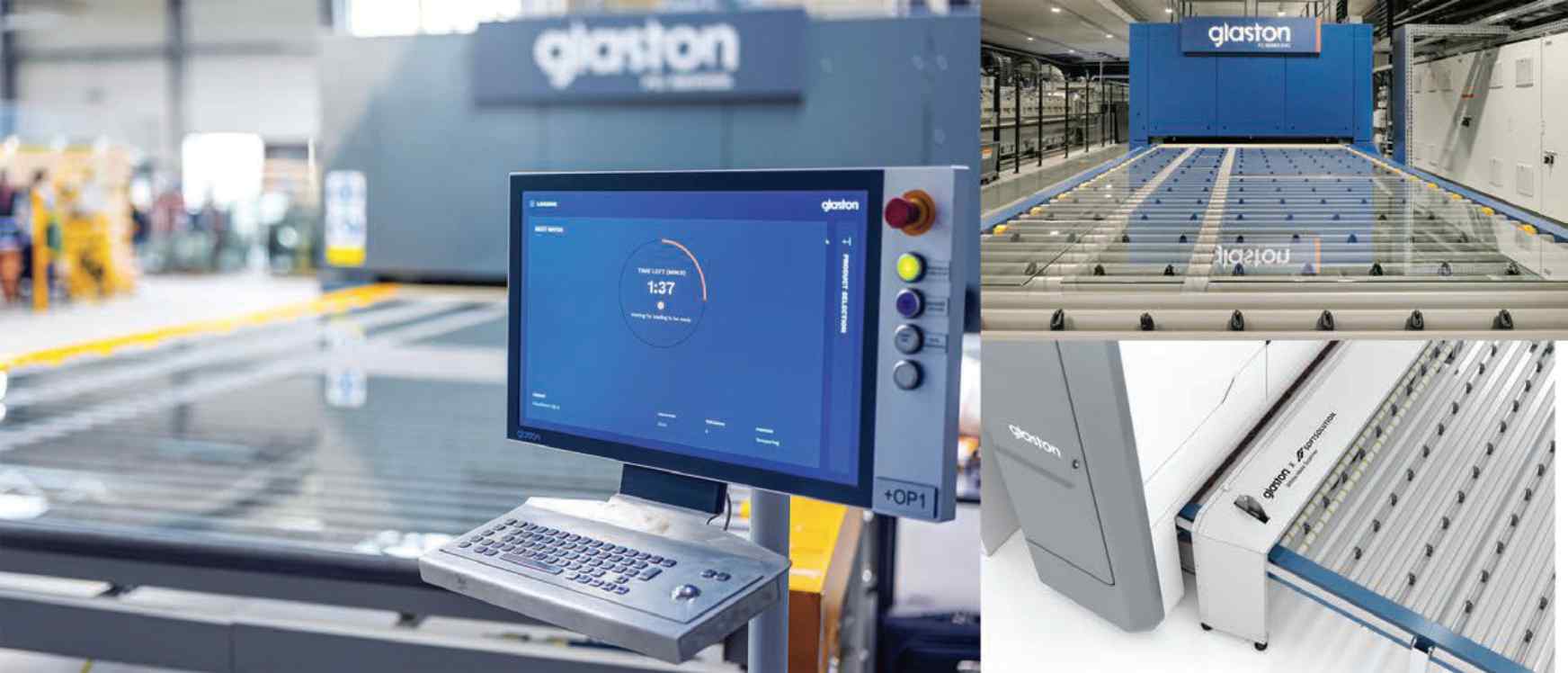
Glaston CHAMP EVO represents the latest evolution in the CHAMP automotive glass preprocessing line.
The newest CHAMP EVO generation includes high-precision features in a grinding machine. Maintenance costs, wear and tear have been reduced considerably with energy-saving, state-of-the-art linear drives that are accurately adjustable. A freely moveable glass holding system shortens changeover times. The optimized cell also features lighter-weight moving parts, such as the cutting bridge and grinding table, plus many other technological advancements.
The new Glaston MATRIX EVO automatic bending furnace is now available to revolutionize the way automotive windshields and sunroofs are bent to perfection. The line is specifically designed to meet the most challenging requirements in today’s automotive industry. It offers the best optical quality even for the most complex shapes and applications, including advanced driver assistance systems (ADAS), heads-up displays and coated glasses.
Boost energy with upgrades
In services, Glaston’s latest developments include new upgrade possibilities for glass heat treatment, insulating glass manufacturing along with automotive and display glass processing.
Upgrading an existing glass processing line with the latest technology leads to significant energy improvements without investing in an entirely new line. Most of our latest technology is available as an upgrade.
This makes it quick and efficient to increase capacity, reach better output quality and yield, reduce maintenance and improve uptime.
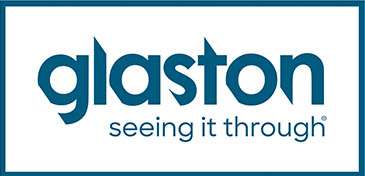
Email: info@glaston.net
Website: www.glaston.net