At FLACHGLAS, a culture of operational excellence fuels continuous modernizations. “The latest Glaston ProL-zone upgrade for our 50-year-old lamination line has helped us raise performance, save energy and automate production with the push of a button,” says Martin Geiss, Technical Manager at FLACHGLAS Wernberg.
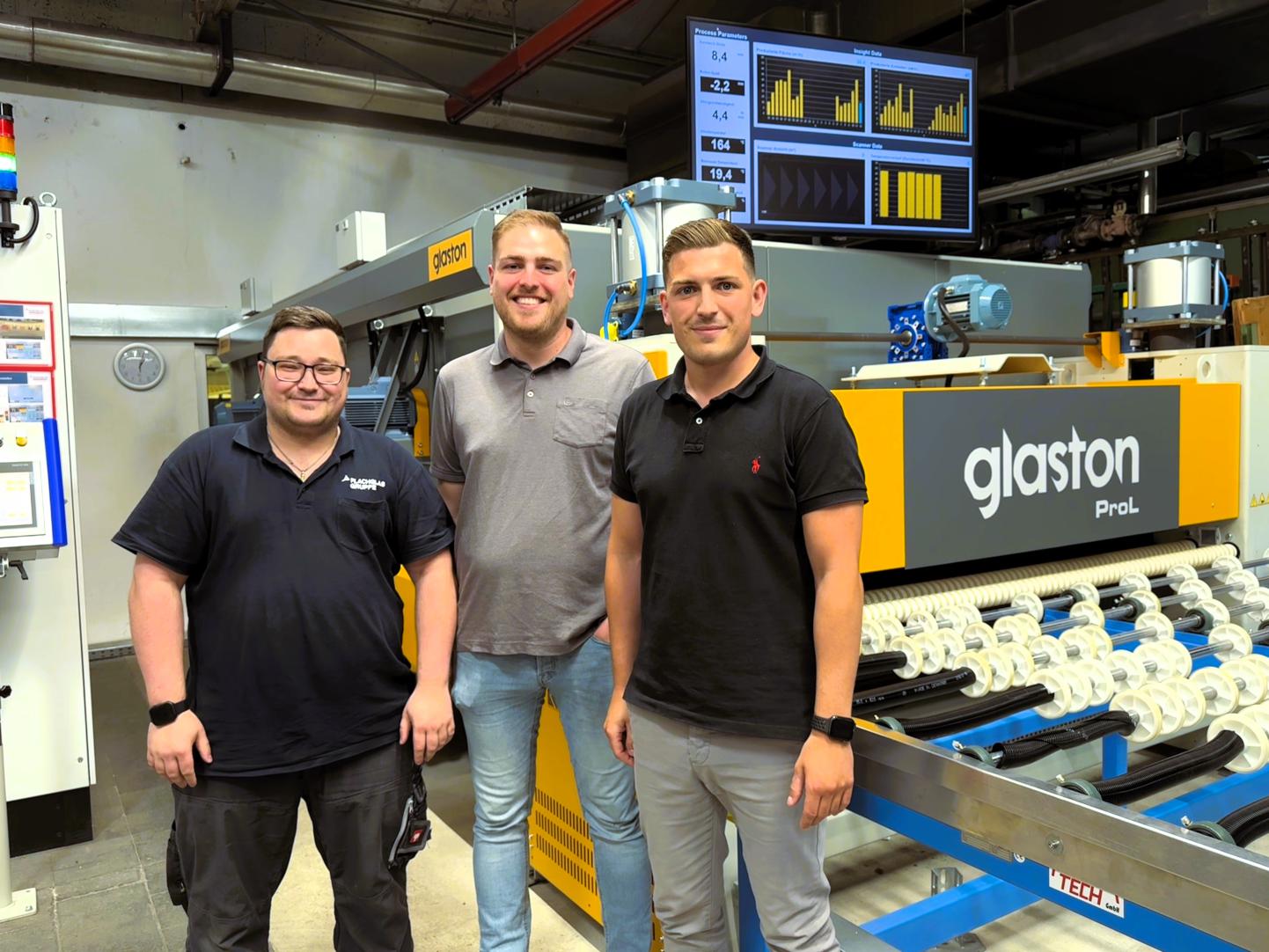
The FLACHGLAS Group has continuously invested in emerging technologies at its three locations in Germany. Along this journey, long-time partner Glaston has actively supported the company’s modernization initiatives and supplied equipment.
Even before the previous joint project to upgrade FLACHGLAS’s two tempering lines was finalized in February 2023, planning for the next upgrade at the company’s Wernberg site in Bavaria was in full swing.
This time, the focus was on the company’s old lamination line, a cornerstone of its operations since the 1970s. The goal was to upgrade it with Glaston’s ProL technology to meet efficiency and sustainability standards while maintaining its unique capabilities.
Back to full operation in 15 days
It took great courage for FLACHGLAS to make any changes to this line. Over the years, the company developed a large number of specialized glass products on this line, requiring considerable expertise. FLACHGLAS wanted to make sure the quality of these specialized products would not be compromised after the upgrade.
The upgrade involved replacing the old heating chambers and both pairs of press rollers with just one heating chamber and one pair of rollers. A reporting system and thermoscanner were added. The results exceeded all expectations.
In January 2024, the line was back in operation in just 15 days – including operator training and even a successful acceptance test with special products.
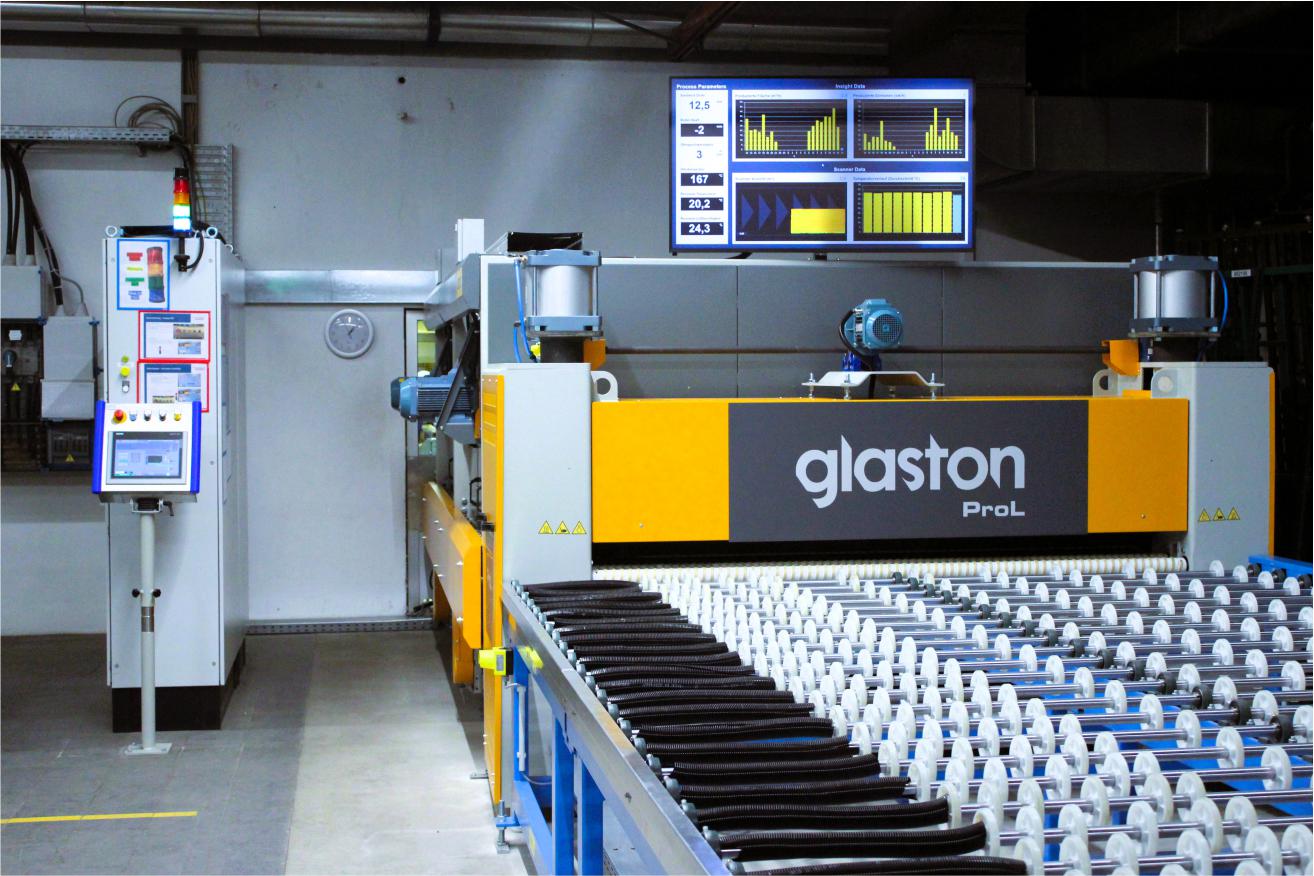
The “split drive,” a game-changing feature of the upgrade, has already paid off. Two drives allow a new sandwich to enter the heating chamber when the previous one has reached the midpoint, even if the sandwiches have slightly different thicknesses. This reduces employee waiting time in the clean room and significantly increases capacity. Presorting according to sandwich thickness is also no longer necessary, eliminating a work step.
Employee intervention in the control and input of process parameters has also been significantly reduced, if not completely eliminated. Employees only need to manually enter the parameters for special products. Most products are produced automatically, with the system setting the proper parameters.
Everyone at the plant is enthusiastic about this. “We simply press a button and no longer worry about the settings. We’re getting consistent and flawless quality at the end of the line,” says Julian Lobinger, Technical Project Manager. “Despite the challenging nature of our products, this mode is 90% reliable and guarantees us consistent capacity and quality.”
Enhanced production capabilities also extend to vehicle and railroad glasses, important sectors for the Wernberg facility. FLACHGLAS can now produce these glasses much faster.
“We have also been able to save 80% in heat costs with our new line. This currently results in an average of 0.02 kWh/kg glass – an absolute peak value,” Julian underlines.
Taking advantage of new solutions
FLACHGLAS’s enthusiasm also extends to the new reporting system and thermal imaging camera. “In the past, we knew little about our production,” says Alexander Frey, Production Level Manager. “With the reporting system, we can evaluate the production data. This also makes troubleshooting very easy.”
He adds: “The thermal images help enormously with quality control as the operators can easily see the temperature of each sandwich. Earlier they relied on occasional manual measurements.”
Eliminating issues of the past
Although the limits of the system are still being tested, FLACHGLAS has already gotten rid of some longstanding challenges. The tiresome issue of bubble formation, especially with coated glass, large sizes and multiple structures, has now been mostly resolved.
Combining different films, another headache, is now standardized without any additional effort. Even multiple superstructures – in fact, everything up to a sandwich thickness of 70 mm – can now be produced as standard and with good quality, greatly freeing up resources.
New line advancements have also enabled the automatic production of laminates with SentryGlas™ interlayers as thin as 0.89 mm. This capability represents a significant leap forward in the process of manufacturing high-performance safety glass.
New project to follow
Given the outcome, it was a no-brainer to upgrade the company’s second laminating line with Glaston, as well.
With the current SentryGlas™ boom for large formats and multi-structures, the new project will also use Glaston’s patented convection control system, dedicated especially for multilayer SentryGlas™ laminates. Producing this glass without vacuuming significantly reduces manual labor and the costs associated with vacuum sealing.
“We know what the line can do, how much energy we save and how easy the process is for our employees. So, it was not difficult to prioritize the new project and get the necessary investment approved by management,” says Martin Geiss, who is already looking forward to its implementation.
Glaston in brief
Glaston is the glass processing industry’s innovative technology leader supplying equipment, services and solutions to the architectural, mobility, solar and display industries. The company also supports the development of new technologies integrating intelligence to glass.
Glaston is committed to providing its clients with both the best know-how and the latest technologies in glass processing, with the purpose of building a better tomorrow through safer, smarter, and more energy efficient glass solutions. Glaston operates globally with manufacturing, services and sales offices in nine countries and its shares (GLA1V) are listed on NASDAQ Helsinki Ltd. For more information visit glaston.net.