Well-Known Safety Glass Consultant J D Pawar Lists Best Practices To Avoid Accidents
On Glass Bulletin’s request, the seasoned consultant with extensive experience in laminated glass production and autoclaves provides in-depth know-how of essential safety measures.
After last month’s devastating explosion at a laminated glass factory in Hyderabad that resulted in multiple casualties, the importance of autoclave safety has once again been thrust to the forefront.
To address these concerns, Mr J D Pawar took upon the task to outline crucial precautions and best practices to ensure the safe and efficient operation of autoclaves, aiming to prevent such incidents in the future.
For laminated glass production, an autoclave is a critical and special equipment. An autoclave is a high-temperature and high-pressure vessel. To avoid any mishap or accident, the autoclave must be used properly.
To ensure the safe and effective operation of the autoclave, it is crucial to verify that all safety devices, sensors, gauges, and electro-mechanical safety interlocks are in place and functioning properly.
Additionally, regular inspections must be conducted at predetermined intervals, in accordance with regulatory requirements. Given the critical nature of autoclave operation, careful attention must be paid to safe loading, unloading, and operating cycle procedures.
To support these efforts, a standard operating procedure (SOP) and written work instructions must be developed and prominently displayed near the workstation, in a language that is easily understood by operators and workers.
Every autoclave is designed with essential sensors, gauges, and safety devices to ensure secure and extended operations.
The following are the important sensors, gauges, and safety devices required for installation within each autoclave:
- Pressure gauge: This instrument monitors the internal pressure of the autoclave chamber while it operates. It ensures that pressure levels remain within a safe range during processing cycles.
- Temperature gauge: This device tracks the temperature inside the autoclave chamber throughout its operational cycle. Maintaining optimal temperatures is crucial for preventing contamination or damage to samples being processed.
- Safety valve: Installed as part of the pressure control system, the safety valve releases excess pressure accumulated within the autoclave chamber if necessary. This safeguard prevents the dangerous build-up of pressure due to faulty equipment or external factors like over-pressuring.
In summary, these three vital components – pressure gauge, temperature gauge, and safety valve – serve as key elements in maintaining the efficiency and safety of autoclaves during their intended use. Proper installation and maintenance of these devices contribute significantly to prolonging the lifespan and reliability of the autoclave unit.
A. Please note and ensure that the following safety interlocks are present with the autoclave and necessary alarms are in place as well:
- High-pressure interlock to prevent over-pressurization inside the autoclave.
- High-temperature interlock to prevent over-temperature inside the autoclave.
- Safety valve to release over-pressure inside the autoclave.
- Door safety interlock to ensure the door does not open while the autoclave cycle is still on.
- Door safety interlock to ensure the autoclave cycle does not start unless the door is properly locked.
Note: Please check and ensure the above safety interlocks are in place and working properly.
DURING AUTOCLAVE OPERATING CYCLE. –
Following points needs to be monitored carefully.
Upon initiating operation of autoclave cycle, when pressure is building inside autoclave, monitor for evident signs of air leakage around the door ring . Any evident air leakage necessitates instantaneous suspension of operations and prompt communication with responsible staff members so they can address this issue efficiently.
In case of abnormalities surfacing relating to the circulation of chilled water supplies or cooling fans throughout the entirety of the autoclave’s operational period, inform the relevant authorities instantly. Timely reporting enables swift troubleshooting and rectification of potential issues.
During Autoclave cycle operation, running condition, the highest temperature inside the Autoclave is about 135 ° C ± 3 ° C, the highest pressure is 1.0 MPa – 1.15 MPa. When the temperature inside is 145 ° C and the highest pressure is 1.2 MPa inside, Autoclave operators should be on high alert, prepare for emergency treatment, and notify the maintenance personnel on duty or the senior responsible authority.
During the operation of the Autoclave, operators must perform regular inspections every 20 minutes. The scope of these inspections includes documenting precise temperature readings within the autoclave compartment, gauging the reliability of its pressure door seals, analysing the flow condition of the water supply employed for cooling functions, compressor operation and assessing the efficiency of various key components crucial to secure and effective autoclave operation.
It is imperative to perform REGULAR INSPECTIONS on the autoclave’s components and systems according to predefined schedules. During these checks, authorized safety personnel should examine various parts as mentioned below to guarantee accurate measurements and efficient performance.
These routine inspections help detect issues early on, allowing prompt resolution before they escalate into serious problems affecting the autoclave’s functionality and overall safety.
Inspections should be documented and results recorded for future reference and analysis.
Regular maintenance and upkeep activities will maximize the lifespan of the autoclave and minimize downtime due to equipment failure. Furthermore, compliance with industry standards and best practices will maintain credibility and compliance certifications needed for continued operation.
B. Routine inspection to be carried out by authorized safety personnel at defined intervals:
- Ensure the autoclave door gasket/sealing ring is intact (not slipping) and fitting in the right slot to ensure an airtight locking of the door. Remove dust and other material particles from time to time.
- Ensure the cooling tower and cold water circulation is proper, the air compressor is functioning normally, and fan cooling supply is also normal.
- Every year, the temperature gauge/sensor should be calibrated.
- Every year, the pressure gauge/sensor should be calibrated.
- Every year, the safety valve should be calibrated.
- After every three years of autoclave operation, check all welding joints and edges for cracks, deformations, rust, etc.
- After six years of autoclave operation, check all welding joints and edges for cracks, deformations, rust, etc.
- It is recommended to replace the old autoclave if used more than the design years (please check autoclave design life with the supplier) because of metal fatigue due to long years of heating, cooling, and pressurizing.
C. CARE to be taken while operating autoclave cycles:
- It is strictly forbidden to have inflammable and explosive materials in the autoclave, as mentioned below:
- PVB film residues
- Wooden blocks/wood particles
- Plastic
- Papers
- Gloves, tapes, etc.
- The autoclave operator and all supporting personnel are strictly prohibited from carrying inflammable and explosive items such as lighters, cigarettes, and notebooks in their pockets.
- The loader shall ensure that the glass is neatly arranged in the glass loading trolley and firmly loaded. When the height of the glass exceeds 1.5m, high-temperature rope/fine wire shall be used to bind the glass on the loading trolley to ensure a firm bind.
- Non-working personnel are strictly prohibited from staying in the autoclave working area.
Most important:
- Get a safety check – test certificate with design life declaration from the autoclave manufacturer at the time of purchase.
- Get a routine maintenance/preventive maintenance manual from the manufacturer.
- The autoclave operator should be a trained engineer.
- A standard operating procedure of the autoclave should be available in writing near the autoclave.
- Work instructions should be displayed near the autoclave in language understandable to workmen.
- Ensure to follow routine inspection without fail as per the defined frequency.
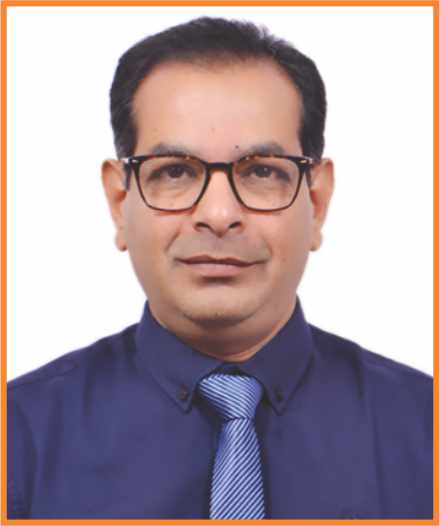
Author:
J D PAWAR Consultants
EXPERT IN SAFETY GLASS PROCESSING PLANTS
3112jitendra@gmail.com