At glasstec 2024, Glaston Will Present Solutions To Speed Up Success Without Compromising Quality
Glaston offers to tailor a plan that matches clients’ specific targets to help them quickly reach their highest glass processing goals.
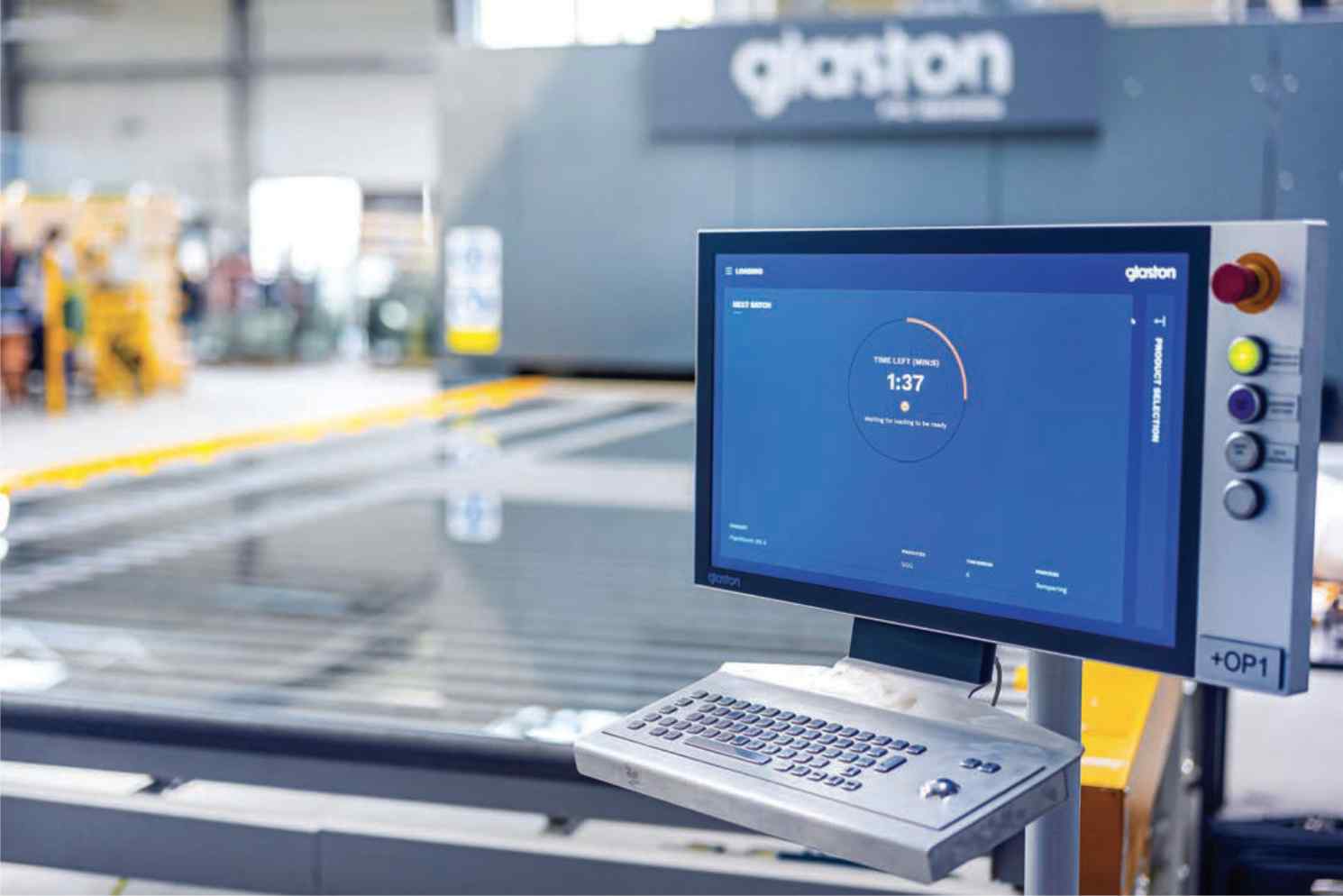
Interested in reaching 30% higher profitability? Glaston’s overall equipment efficiency cuts costs, giving you higher productivity and better bottom-line results. You can experience effortless production line operation with flawless accuracy and consistent quality through our advanced automation solutions. And you can extend your machinery lifetime with high uptime using our comprehensive services
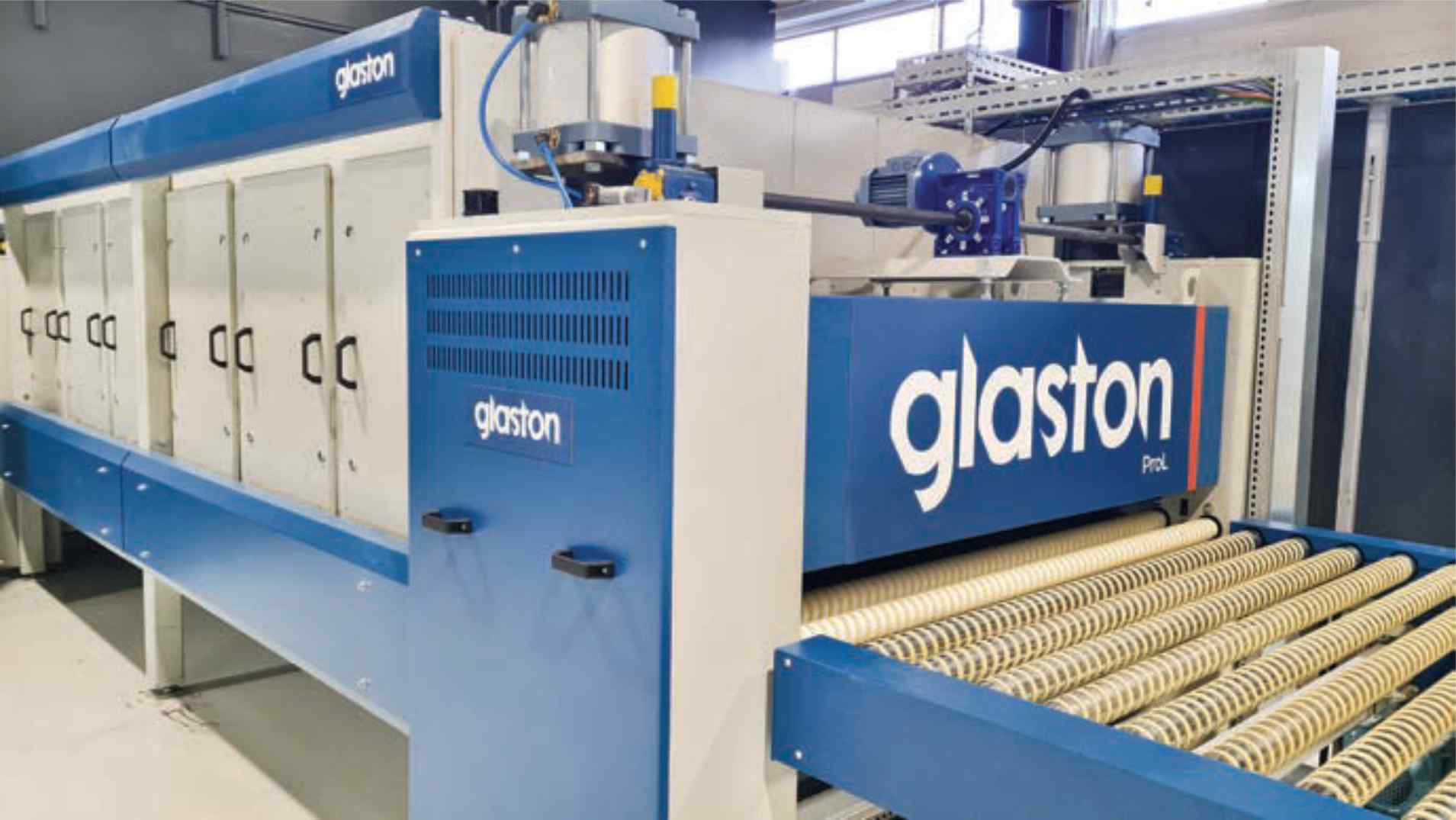
Below is a sneak peek at what Glaston will be showcasing at glasstec 2024.
In glass tempering:
Glaston’s latest-generation RC and FC Series tempering line technologies underscore its commitment to continuous development and customer satisfaction. Since their first introduction to the market in 2010, Glaston’s RC and FC Series have undergone substantial evolution. Today, it proudly present the 7th generation, tailored to meet your specific needs with our “fit for you” approach. These newest-generation lines are further boosted with our pioneering automation solutions designed to accelerate operation across all production stages.
Glaston Autopilot is the company’s latest innovation for higher speed, continuous quality and reduced waste in glass tempering. The solution automates the operation of Glaston’s glass tempering machines, minimizing operator input in the process and offering process control without parameters.
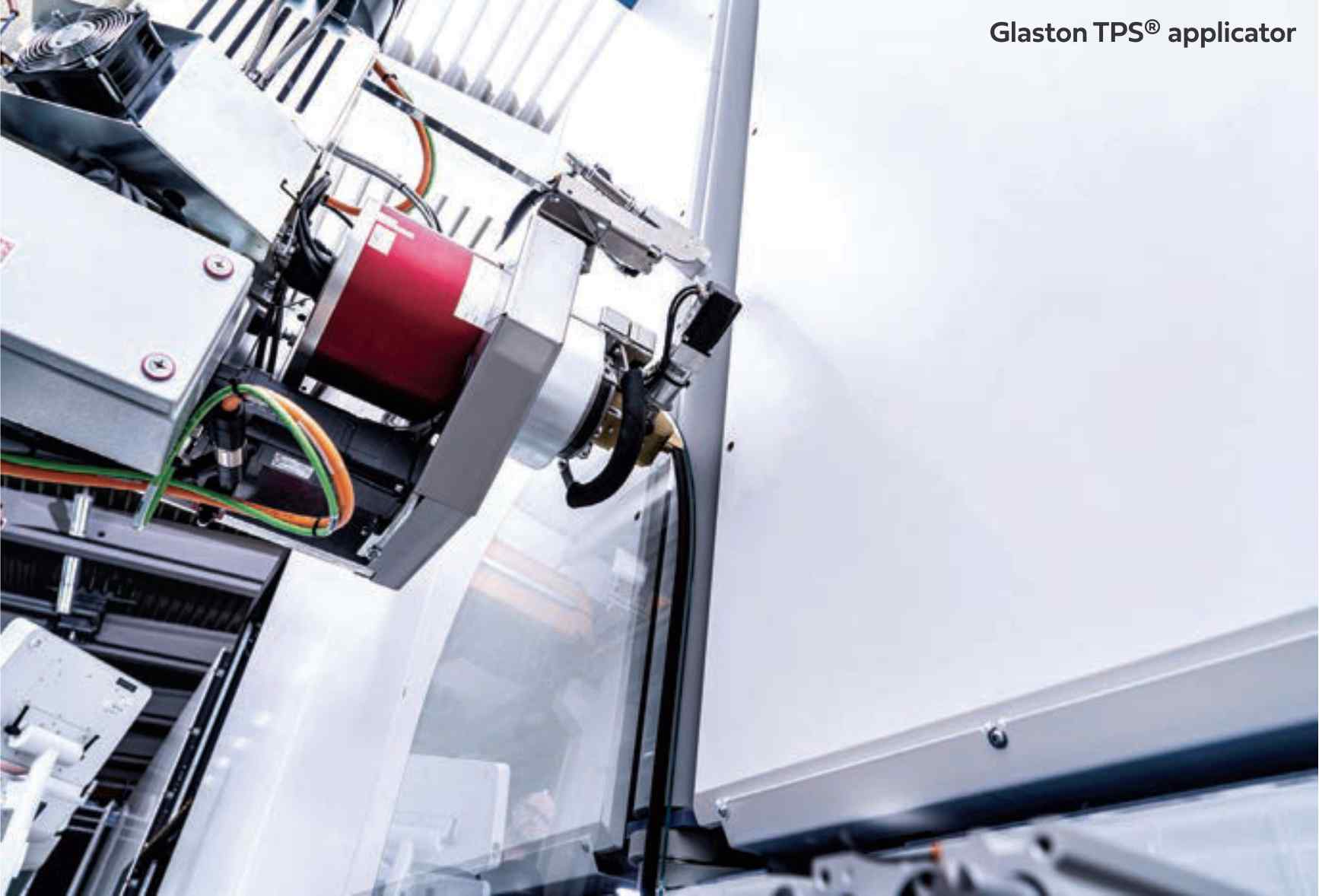
In glass lamination:
Glaston ProL flat glass lamination line provides greater flexibility for mixed production. The ProL convection heating chamber makes switching between glass types and different glass sandwiches easier. The whole line – from glass handling to the latest PVB cutting technology – has been designed for flexible operations.
The ProL Convection control technology is Glaston’s new solution to address the increasing demand for structural interlayers. It offers a significantly wider operating window, even with complex laminates. An automated trimming system precisely cuts the foil, eliminating the need for manual work and further increasing accuracy and efficiency.
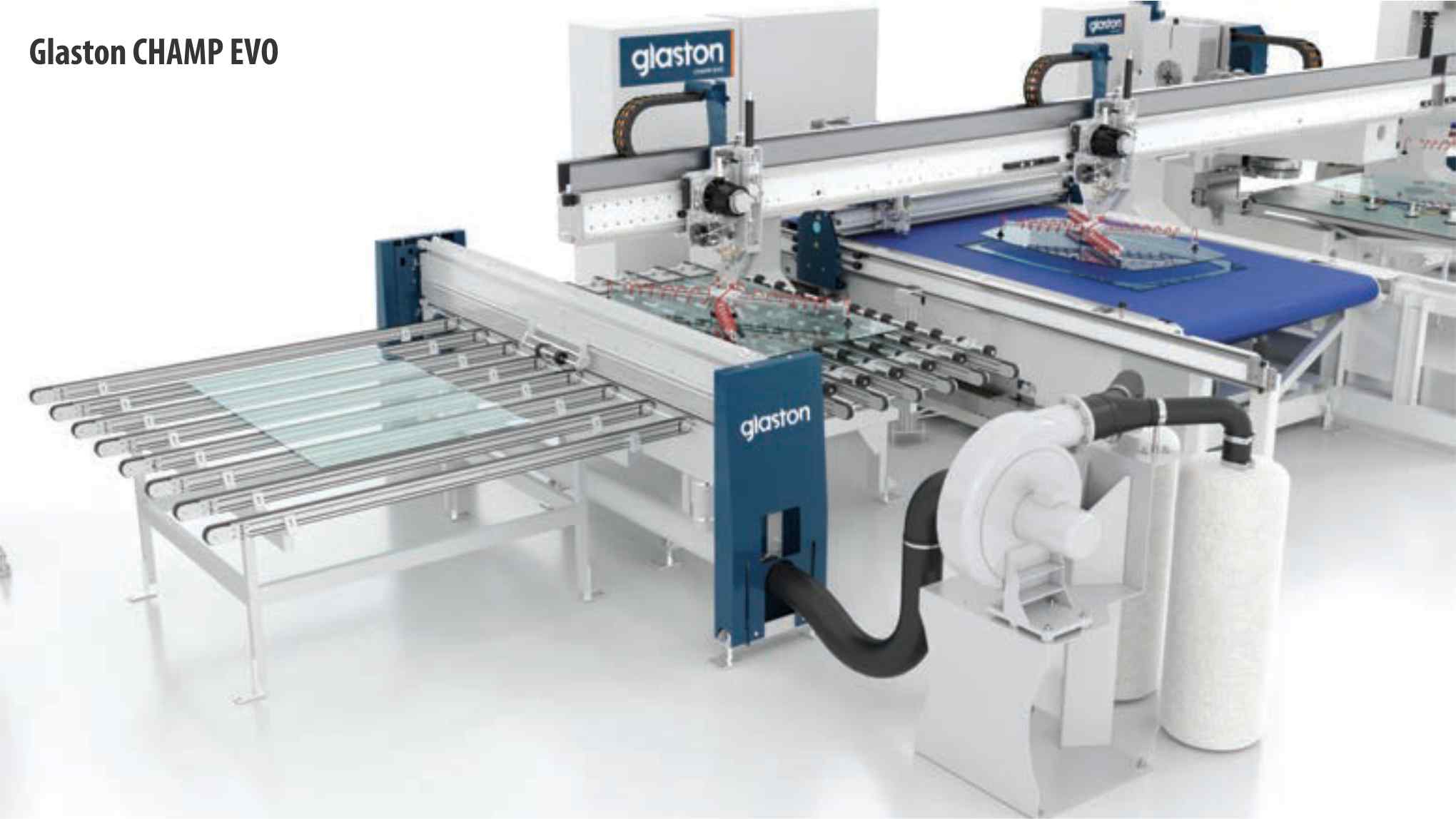
In insulating glass manufacturing:
Glaston TPS® PRO revolutionises efficiency and productivity in insulating glass manufacturing. The latest solution features a new control system and production process subsequence for as much as a 15 per cent higher yield. The Thermo Plastic Spacer (TPS®) material can be applied directly onto the glass plate to flexibly produce IG units, multilayer or solar panels. The new concept of the drum pump system leads to a higher material discharge due to the tandem operation without any time loss. Glaston triple thin IG unit production meets regulatory demands and promotes sustainable practices. Offering significant energy efficiency benefits, the solution is perfect for building renovations reusing existing window frames. Glaston MUNTIN’MASTER for TPS® lines automates the correct setting of grids in IG units. The advanced solution replaces manual work, boosting precision and efficiency with speed. Glaston ACTIVE’SEALER automates double glazing production with Glaston’s proven dosing technology. The solution shifts operations from manual sealing to automated, ensuring consistent quality and faster production times. ACTIVE’SEALER is specifically designed for markets with a high proportion of double IG units.
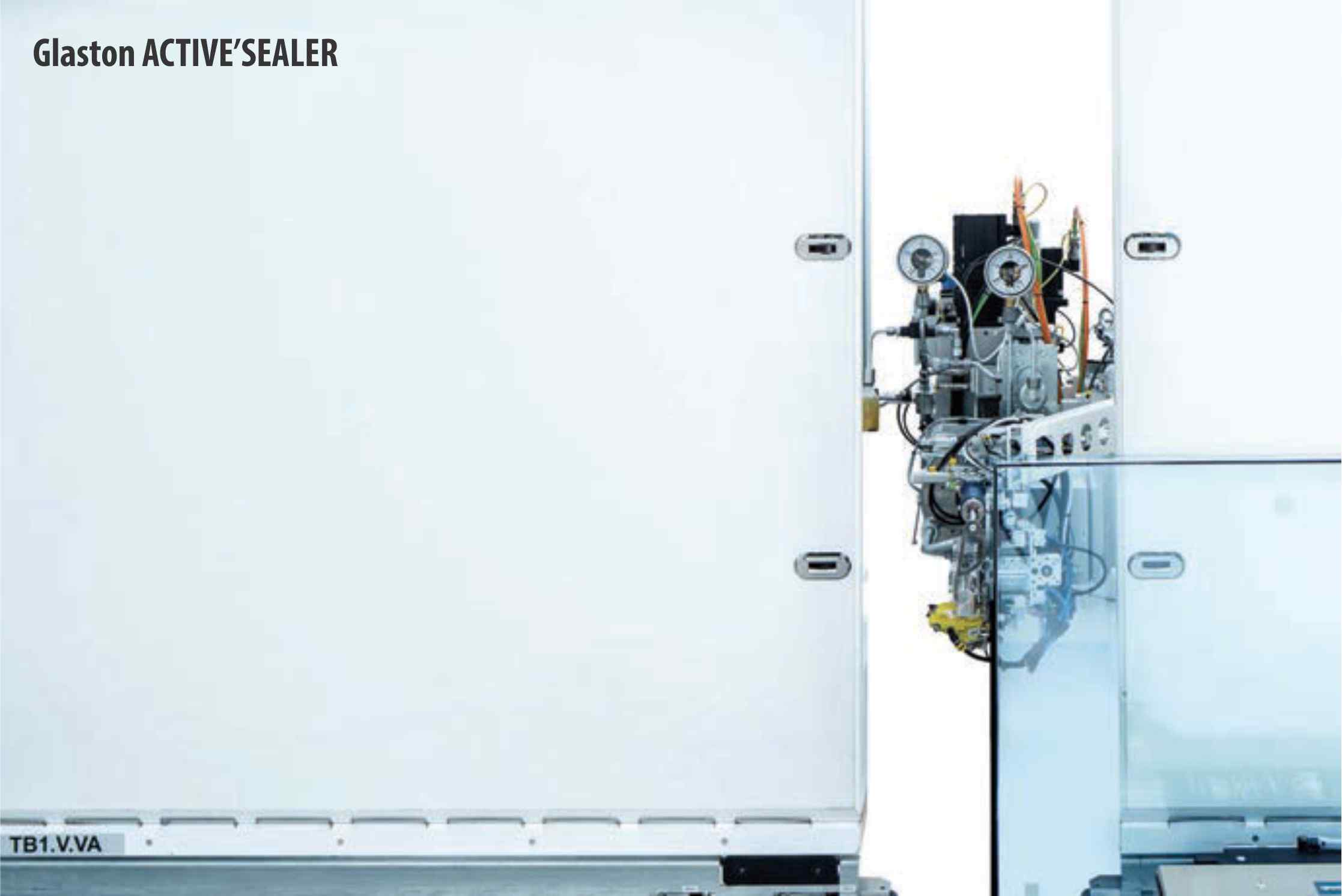
In automotive and display glass processing:
Glaston CHAMP EVO for mobility glass pre-processing automates the cutting, breaking and grinding phases, increasing performance and speed. Along with other technological advancements, the line’s freely moveable glass holding system speeds up changeover times while ensuring precision and quality. This generation offers better controllability,more dynamic movements and high grind edge quality for all shapes. The Glaston HYPERFEX grinding system revolutionizes glass edge grinding. The new HYPERFEX grinding wheels take into account all aspects of glass pre-processing for different applications and demonstrate significantly improved performance. The new Glaston MATRIX EVO automatic windshield bending furnace is designed for faster, highperformance production. The line’s new windshield press bends deep sags and wraps around corners precisely. With Glaston’s active convection technology, it speeds up heating even for coated, printed or otherwise complex glass types. MATRIX EVO is available in various sizes and configurations to meet your specific needs.
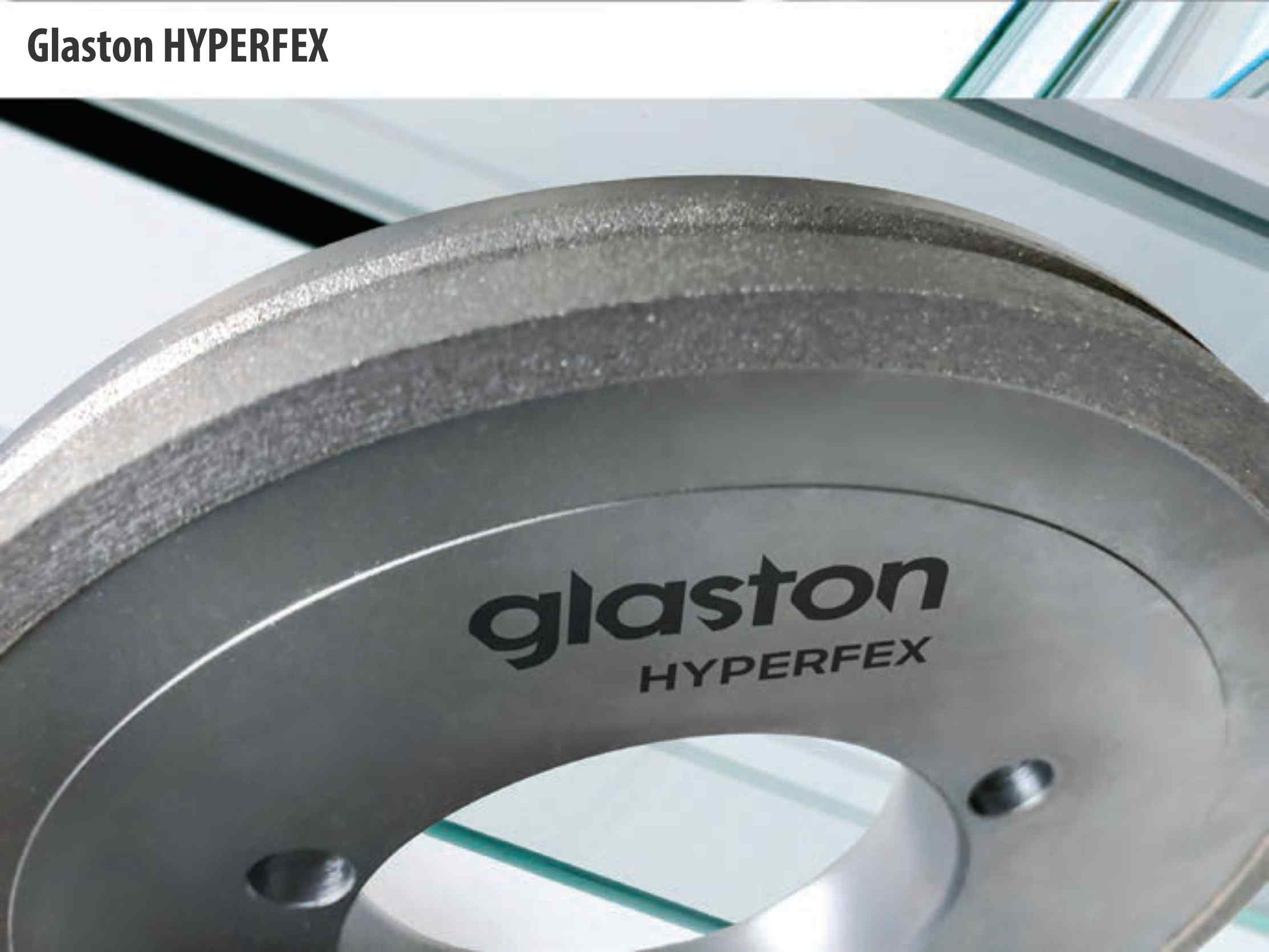
In upgrades:
Glaston’s latest development in services includes new upgrade options for glass heat treatment, insulating glass manufacturing and mobility and display glass processing. Glaston’s CNC96 upgrade kit for automotive and architectural glass cutting equipment boosts the CNC96 control system while replacing any end-of-life components. Glaston heating chamber replacements with RC or FC technology for older tempering lines improve heating and cooling, endproduct quality, energy efficiency and productivity. Extend the lifecycle of your equipment and capabilities with the latest technology. Glaston ProL-zone upgrade is designed for a quick and costefficient modification of your existing laminating line. ProL-zone speeds up the laminating process considerably. You only need to put in one parameter – and the line takes care of the rest. Its full convection technology eliminates heat loss, saving energy.
In services:
Glaston Care offers a comprehensive service agreement that guarantees the highest possible equipment reliability. Its lifecycle support minimizes downtime, reduces total cost oF ownership and extends the lifetime of your machines. Join Glaston’s live demos and meet with its industry experts at Stand A48–A49 in Hall 15.
Email: info@glaston.net
Website: www.glaston.net