HANJIANG successfully installed and completed the acceptance of a fully automated, high-speed IGU production line for refrigerator glass in Brazil. This line efficiently produces both double and triple IGUs, as well as 1 to 4-sided step IGUs (overlap IGUs). It is capable of processing both traditional rigid spacers and flexible spacers.
Leveraging HANJIANG’s extensive design and manufacturing expertise, we customized an ultra-fast IGU production line to meet the client’s high-speed production requirements. Through continuous efforts and improvements, the production cycle achieved an impressive rate of two IGUs per minute, with each unit produced in just 30 seconds. The entire line is equipped with robotic glass loading, a high-speed washing machine, and a high-speed press that processes two IGUs simultaneously, ensuring that gas-filling in each glass exceeds 90%.
However, realizing this process was with many challenges. Synchronizing the cycle time of every component in a fully automated production line—from loading to unloading, washing to frame assembly, robotic handling of Super Spacer to high-speed Argon gas-filling and pressing, and high-speed sealing—required meticulous planning. Starting with strict calculations during the design phase, followed by production, commissioning, trial runs, and final acceptance, we encountered numerous issues. These ranged from automating the glass loading process and handling different glass rack heights for customers, to preventing glass adhesion during unmanned operations, matching the number of glass racks during loading and unloading, accelerating the robotic arm’s speed under full load, and synchronizing the entire line’s speed. Each challenge was overcome through the tireless collaboration of the HANJIANG team and our Brazilian service team-NEX, who worked day and night.
Mr. Emerson, the owner of the machine, stated, “HANJIANG and NEX have truly overcome a significant challenge, which has greatly impressed us and transformed our traditional methods of processing IGUs.”
Mr. Jones from NEX added, “The HANJIANG team provided us with tremendous support, ensuring the smooth progression of this project. Both teams had to fully trust each other and overcome all on-site challenges, ultimately delivering satisfaction to the customer.”
To fulfill our initial promise, we spared no effort. Ultimately, the production line achieved full automation for Super Spacer, requiring only manual inspection for quality control and unloading. During high-speed production, we minimized labor requirements while maximizing efficiency. When producing traditional spacers, the line met the client’s high production demands with ultra-fast capabilities. The project culminated in the client’s satisfaction, successful acceptance, and prompt payment.
Every successful project marks the starting point for the next. At HANJIANG, we strive to surpass ourselves, instilling confidence and satisfaction in our clients.
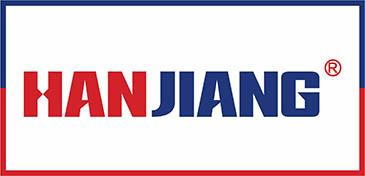
Email: Asia@hjglass.com.cn
Website: www.hjglass.com.cn