Founded about five years ago, AGP set out to manufacture insulating glass units for the APL Window Solutions group in New Zealand. With a dedicated team of around 100 employees, AGP primarily produces double and triple glass units, with 75 % of their products featuring low-e coated glass. The vast majority of their output serves the residential market in New Zealand.
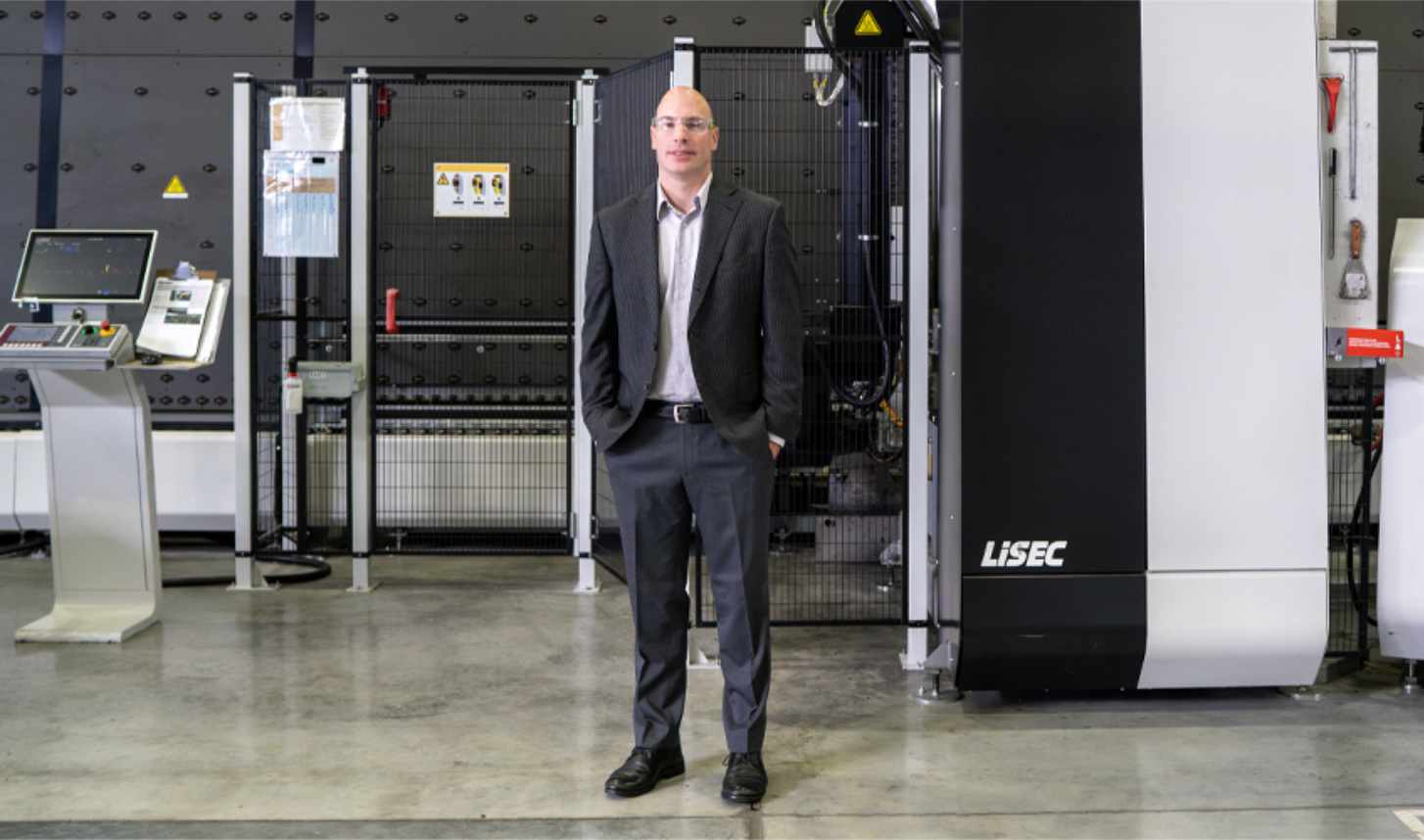
AGP is a lateral entrant into the glass business, joining it in 2018 without any prior experience in the industry. LiSEC’s excellent reputation made the company a natural contact point for AGP when it came to setting up a production plant for insulating glass. Introduced through the Glasscorp agent in New Zealand, AGP was impressed by LiSEC’s products and the comprehensive service package. The relationship between AGP and LiSEC is built on mutual benefit: “With LiSEC we innovate together, we grow together and we solve problems together.”, says David Bunting, Managing Director of AGP. So they took on the challenge to realize the perfect green field project together.
Streamlined Perfection: The LiSEC Setup at AGP in New Zealand
The LiSEC production lines, referred to as streams at AGP, are fully optimised in terms of process flow. In the 415 metre long production hall, the three LiSEC production lines extend over 335 metres in a straight line, a well-considered aspect during the planning phase that has proven a major advantage in terms of cycle time for the insulating glass producer from New Zealand. The first three streams are characterised by a linear production flow without the need for a single return or curve. Thanks to the high level of automation, the systems require relatively few operators.
The processes at AGP are highly complex, but the LiSEC sorting system is extremely well thought out, moving panes across multiple processes with unrivalled efficiency. Beyond sorting, each glass pane is identified using a laser logo and data matrix code, which enables tracking throughout the entire process.
For a seamless production process, two LiSEC PKL glass storage systems are interconnected and linked to three LiSEC cutting tables at APL in New Zealand.
The cutting system of the first stream features the LiSEC ESL-RS and ATH machines. A unique aspect of this system is the light barrier that divides the glass storage, allowing one half to be refilled by the operator while the other half is in use, ensuring the production process is not interrupted. Additionally, a remnant plate storage loaded by a movable loading table collects remnant plates for later use.

The cutting system of the third stream is also a combination line to cut float and laminated glass with the LiSEC ESL-RS for float glass cutting and a LiSEC VB for laminated glass cutting, capable of cutting jumbo sheets up to 5 meters in size.
After each of the three cutting systems, the glass is processed by the LiSEC KSR + KSV machines to seam all four sides. The glass is then washed and inspected for defects by a scanner. At this inspection station, operators can review and address any defects; if a defect cannot be fixed, the glass sheet is remade. Quick cycle times are ensured by the sorting system that collects sheets headed for the tempering furnace while allowing non-tempered sheets to pass by. The collected sheets are transported vertically to the tempering furnace, where operators place them on the tempering bed and remove them after processing.
All glass sheets, whether tempered or not, are sorted into insulating glass production sequence at the insulating glass sorting buffer. The buffer feeds three LiSEC TPA insulating glass lines, each equipped with a washing machine, scanner, and inspection station. The middle line features the LiSEC logistics solution NWLD for rotating and incline coated glass panes. The first and second lines handle glass sizes up to 3.5 meters, and the third line handles sizes up to 5.0 meters.

AGP’s highly automated and optimized setup ensures efficient production with minimal operator intervention, maintaining a continuous and streamlined process from start to finish. The systems are customised for glass sizes up to 5.0 metres, which offers a high degree of flexibility in production. The production process remains the same which facilitates the integration of new processes. The LiSEC AGP press and full sealing support round off the range and guarantee high product quality of the insulating glass units. Additionally, the spare parts situation is excellent: Using different machines from the same company enables quick and uncomplicated maintenance. Thanks to the high interchangeability of components and simple operation, the systems of LiSEC are particularly user-friendly.

AGP’s customers demand high quality, excellent service, and on-time delivery. LiSEC’s products support this vision: Their high quality is visible in the production. Using LiSEC products on a daily basis, AGP can say that they are at the cutting-edge, reliable and produce high quality products. The company also points out the strong support system of LiSEC. David Bunting, Managing Director of AGP, states, “Through the partnership with LiSEC, we are able to produce fantastic quality products and provide excellent service, which has allowed us to grow. As a result, we plan to add a fourth stream of LiSEC products, covering everything from cutting and buffering to insulating glass production.” The demand for low-e glass is increasing, driven by legislative changes making it compulsory. AGP is also seeing growth in the commercial sector. They aim to continue providing perfect quality and service to their customers, enabling them to grow. By investing in their partnership and a new project with LiSEC, AGP can maintain high production levels.
Leading the Industry: The LiSEC Advantage
For AGP LiSEC stands out in the industry by offering a complete package, from machines and software to service. Their highly capable staff can solve complex problems, think outside the box, and possess the technical knowledge needed to refine workflow processes. LiSEC’s reliability, both in technology and support, ensures that AGP can achieve the best possible outcomes. Thinking about the future Bunting says: “The industry needs to continue innovating, and I hope that companies like LiSEC will lead the way. David Bunting expects to see new innovations in the near future, ensuring that AGP remains at the forefront of the glass manufacturing industry of New Zealand in the future. In an interesting podium discussion on the LiSEC booth at glasstec 2024, Bunting once more highlighted the advantages of LiSEC’s products and AGP’s satisfaction with it.
Press Contact
Claudia Guschlbauer
Director of Marketing & Corporate Communications
Tel: +43 7477 405-1115
Mobile: +43 660 871 58 03
E-Mail: claudia.guschlbauer@lisec.com