The Era of Warm Edge Spacers is Here: Time to Redefine Insulating Glass Manufacturing
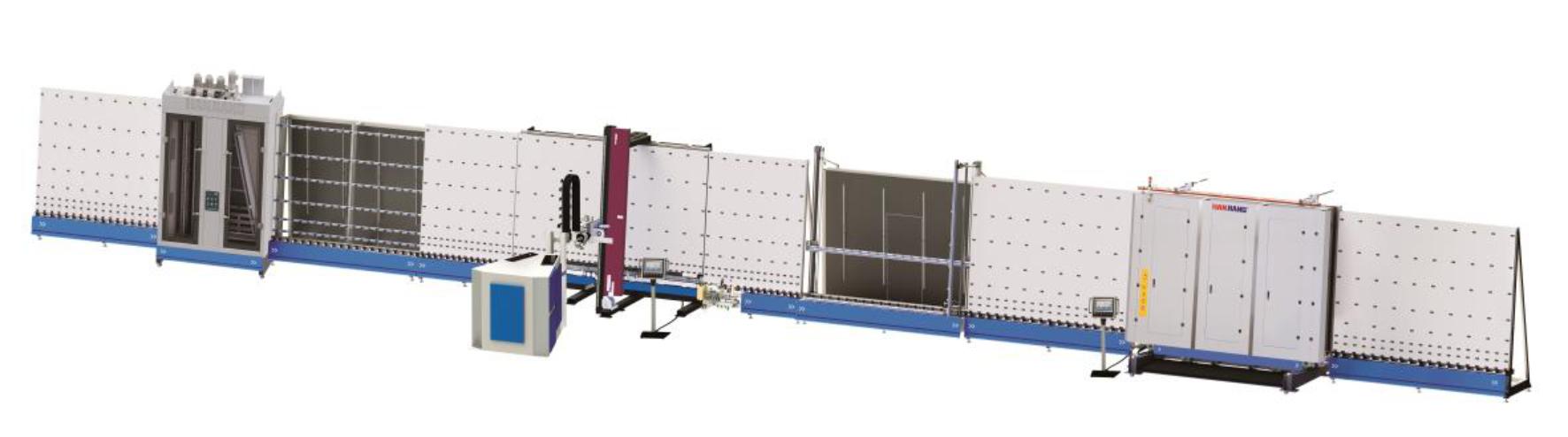
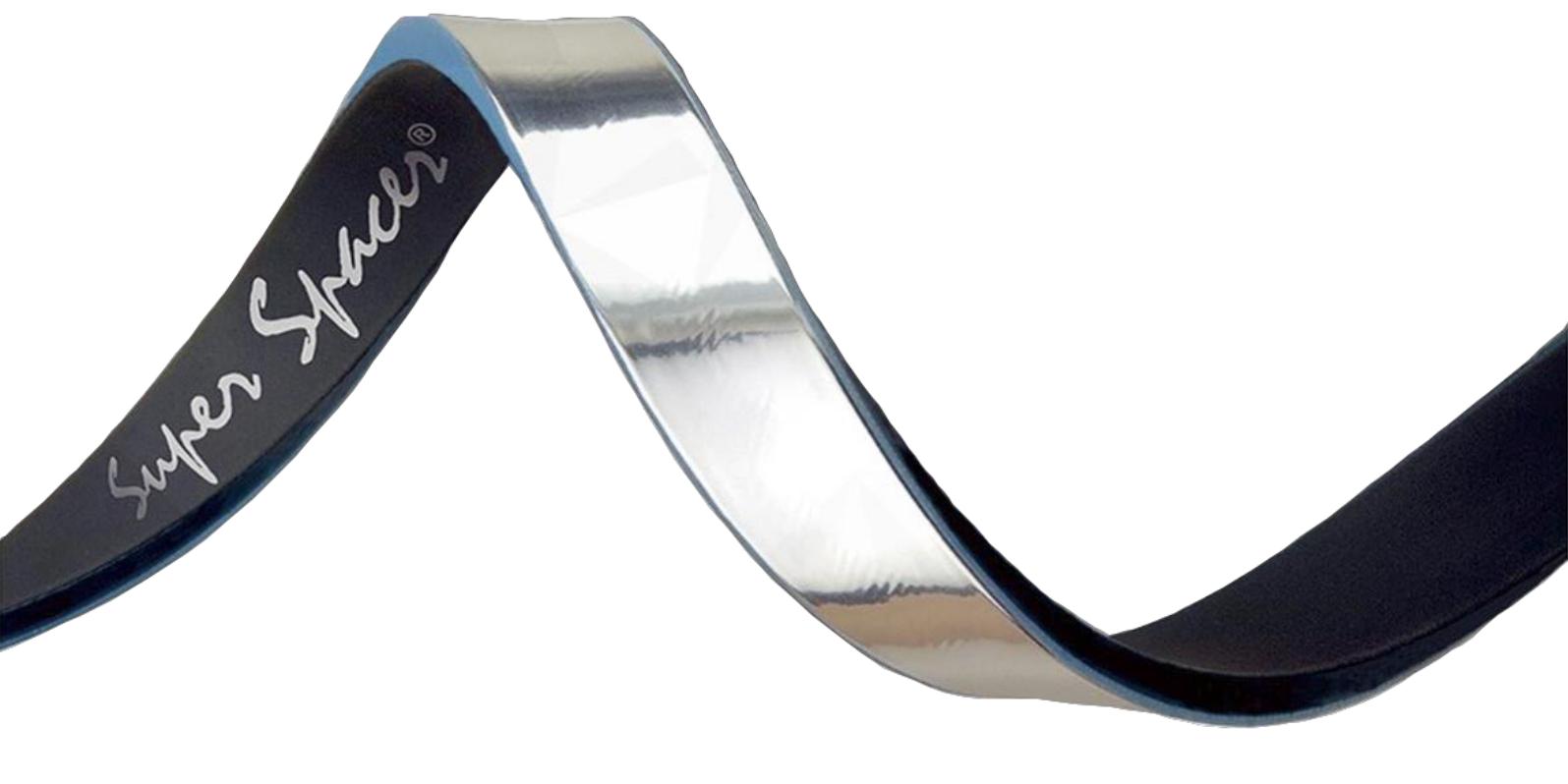
Advancements in Automation
Compared to traditional rigid spacers that require cutting/bending, desiccant filling, butyl application, and manual sticking onto glass, HANJIANG’s Super Spacer Applicator (SSA) simplifies the process by automatically applying spacers onto glass in a single step. This automation significantly reduces the number of production steps and labor involvement, leading to enhanced efficiency and a decrease in product defects due to human intervention.
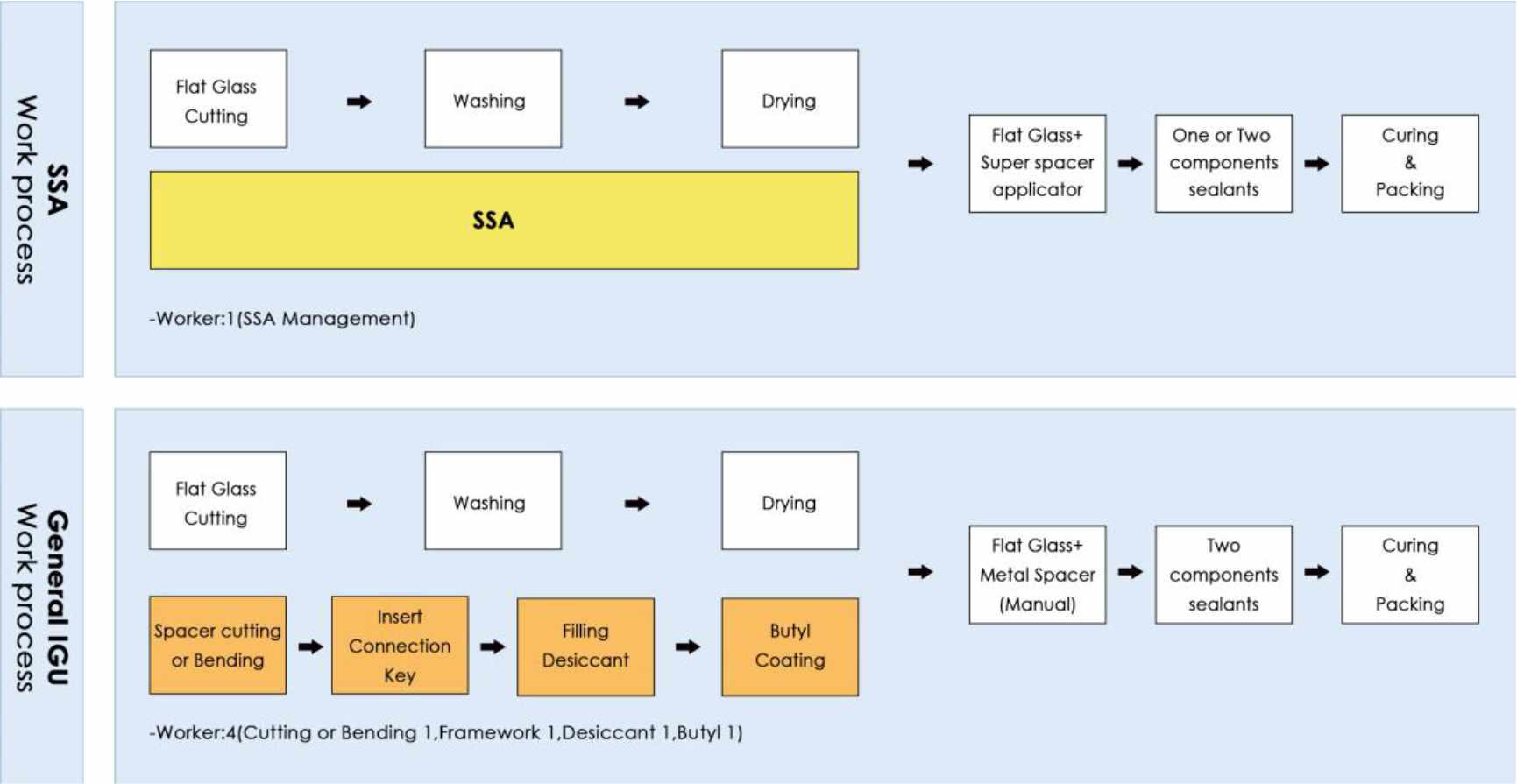
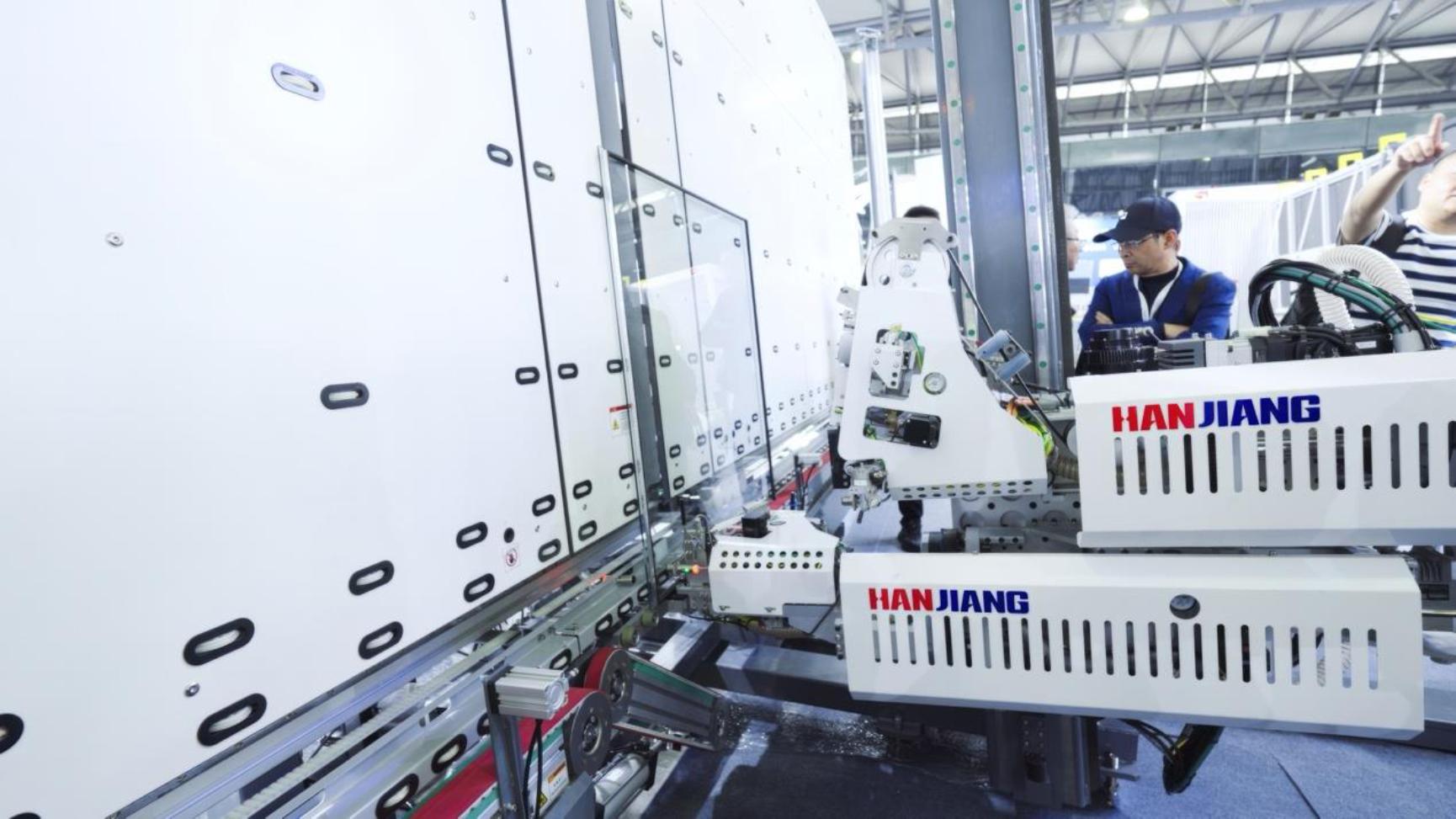
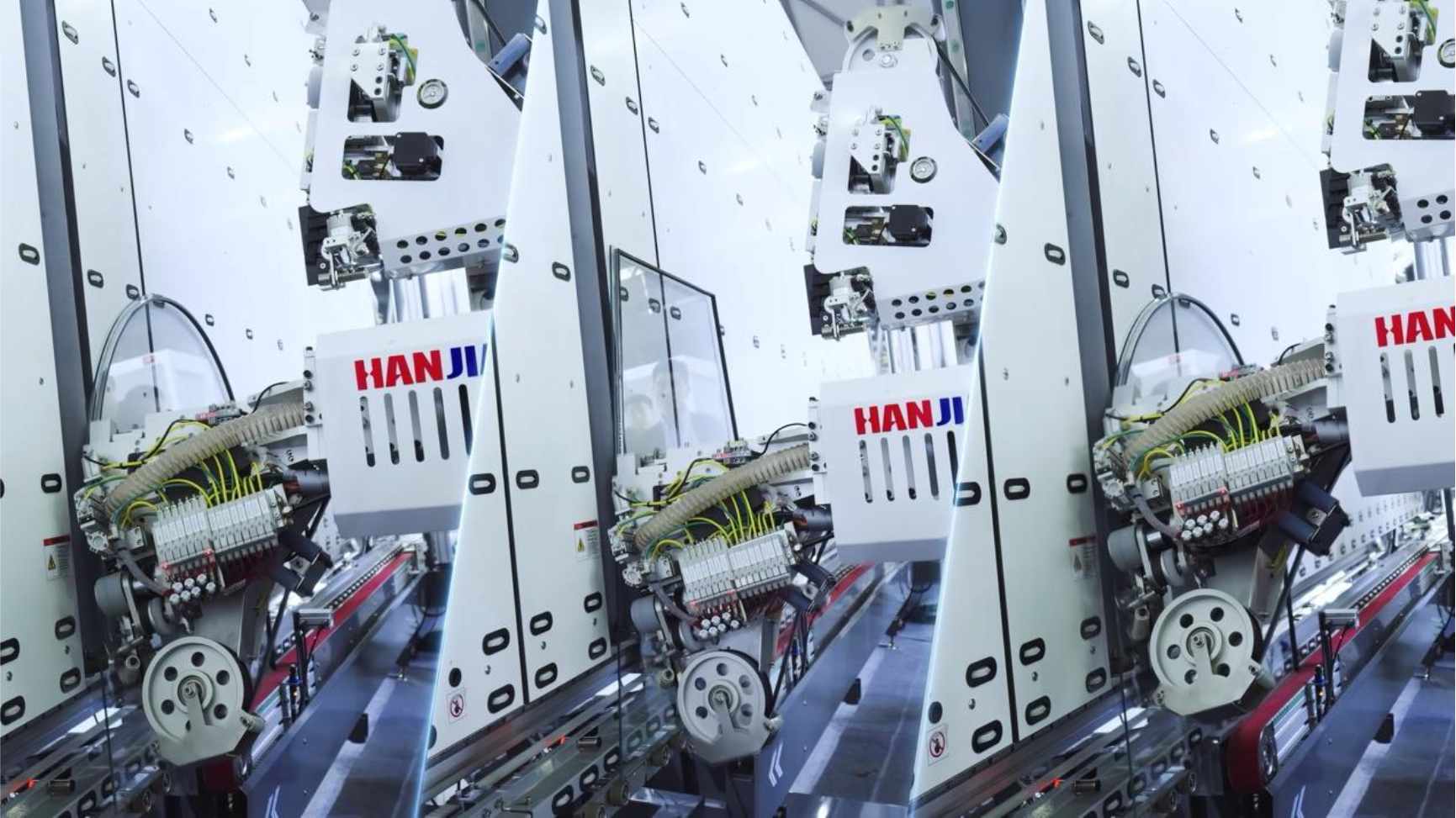
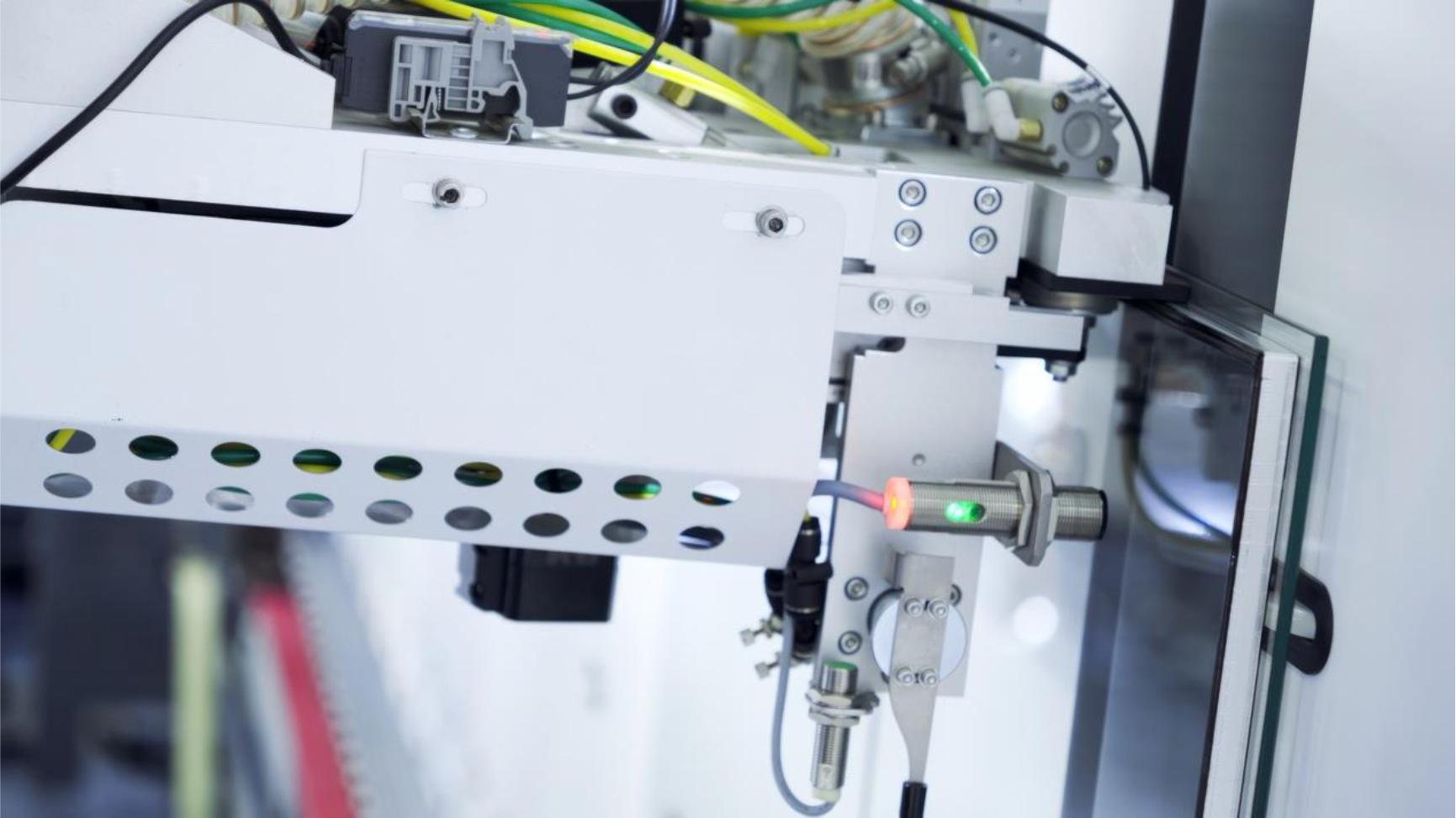
In high-end windows and curtain walls, energy efficiency is paramount. Super spacers meet the highest thermal performance standards (phA and phA+) set by Germany’s Passive House Institute (PHI) and are suitable for all climate zones worldwide. With HANJIANG’s online Argon filling IG line and defect detection system-Line Eyes, the equipment can achieve up to 90%-95% pure Argon filling, significantly lowering the U-value of IG units for optimal energy efficiency.
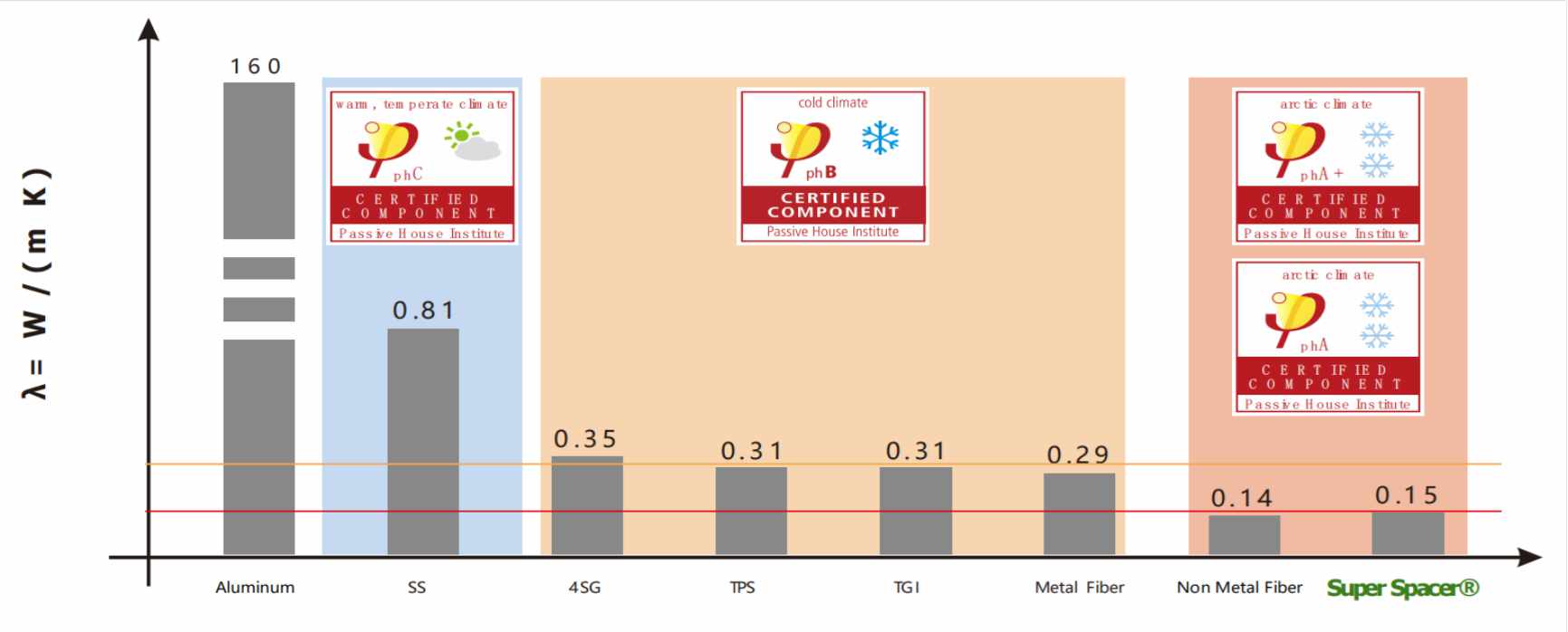
As window and curtain wall glass grows larger and thicker, the demand for high-quality, large-format IG units increases. HANJIANG’s oversized super spacer production lines support dimensions of up to 3×6 meters and even 3.6×10 meters. The system features high-load transportation, high quality washing, and precise primary sealant and spacer application to ensure both high-quality output and production speed. It is ideal for processing complex triple or four-sided jumbo IGUs.
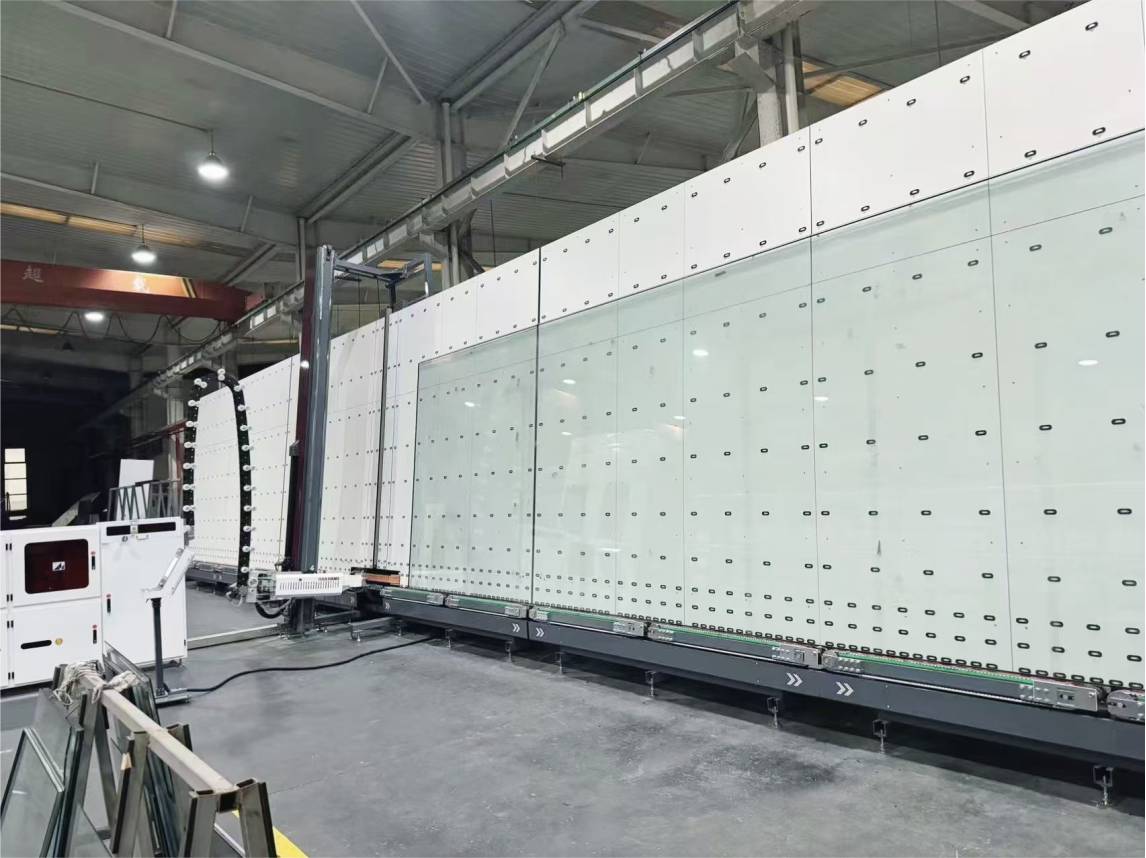
While the initial investment in SSA is higher, it brings significant efficiency and quality advantages in producing large, high-value glass products. For IGUs exceeding 2000×3000 mm, this technology offers superior cost-effectiveness and differentiation in a competitive market.
In today’s competitive landscape, HANJIANG provides more than just production equipment—it delivers a sustainable, automated, and intelligent production solution. We invite you to join us in exploring the future of warm-edge technology and smart manufacturing.