Demand-Supply Gap Soars, Prices Hit All-Time Highs; Processors Wary As No Solution In Sight
India’s glass industry is going through a very difficult time as the country looks to come out of the shadow of the COVID-19 pandemic.
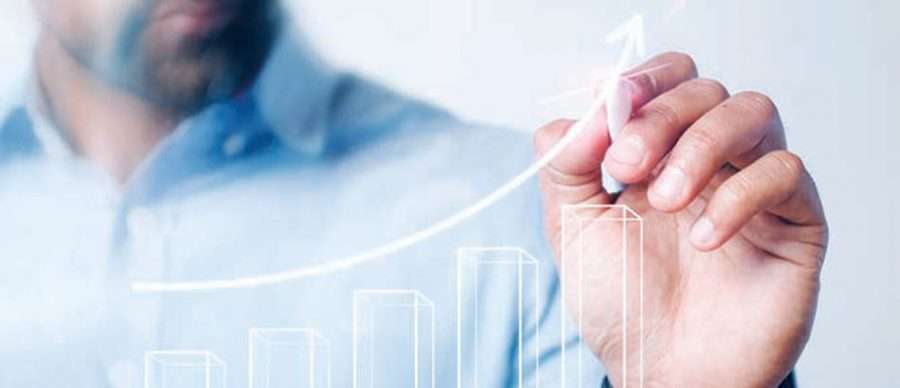
Amid a number of uncertainties, the glass industry of India also faces a historical shortage of flat glass in the market, especially clear float glass.
Glass Bulletin conducted a survey on this current situation of glass shortage among glass manufacturers, dealers, glass processors, wholesalers and retailers to understand what they think about it and also sought their feedback and suggestions to overcome the same.
During the lockdown last year, glass companies were breaking glass and recycling it to keep their furnaces running and also avoid surplus stock in their warehouses. But after the lockdown was eased, demand of glasses in various segments have increased tremendously.
But since the production capacity remained unchanged, the gap between demand and supply widened. This gap of glass in the market meant manufacturers were unable to meet the demand. But it also meant prices soared to all-time highs.
There has been no new float line set up in the last two years (after 2019). And setting up one from scratch takes at least two years before production can begin. Hence, while demand will rise, supply won’t, which essentially means the gap will persist.
As production capacity has remained unchanged, gap between demand and supply has widened, pushing prices to all-time highs.
Import of glass has fallen significantly after COVID-19 and freight has become three to four times higher than usual. So, even importing glass makes less sense now as costs will rise. The Indian government has imposed anti-dumping on the import of glass. This means prices are bound to go higher in case of imports.
The gap has grown to an extent that big and established processors are unable to get raw materials. This, in turn, is preventing new processors from entering the segment.
New glass processors who were still willing to come and start processing units are definitely the most affected.
The situation is more problematic for new entrants as they find themselves staring at no supply of raw materials to keep their units running as glass is the basic raw material to run a glass processing unit.
With the demand climbing, processors find themselves in a situation where they are unable to fulfil orders. Many are even refunding advances received for orders as they are not able to procure the raw materials required for it.
Prices of raw materials fluctuating so rapidly that processors are unsure how the change in the raw material cost will affect production cost. As a result of this, processors are also reluctant to take orders.
Manufacturers on the other hand have kept up exports. Many processors GB spoke to wanted government intervention to temporarily pause exports so that domestic market can recover from the historic shortage of raw materials.
Several companies were also of the opinion that manufacturers should understand the seriousness of the situation and make efforts to back domestic processors.
Float companies, however, said they were giving raw materials to their customers who have stood by through difficult times. Local home appliances manufacturers have approached them for glass as they are unable to procure it from China and other countries like they used to earlier due to high prices.
Float companies also said they understand the current scenario of shortage. All such companies GB spoke to assured that they are more focused on manufacturing clear float glass and are also planning capacity expansion to minimise the shortage.
These companies said they are increasing prices due to rates of raw material and fuel being at all-time highs.