Perfect For Companies Searching For Inexpensive Options To Expand Insulating Glass Production Capacity
With COMFORT BOX insulating glass manufacturing line, Glaston offers a high-quality IG line for the manufacturing of gas-filled IG units of rectangular and shaped formats.


The great advantage of the Glaston COMFORT BOX is its simple handling and uncomplicated operator guidance. The base model of the insulating glass line consists of three elements: a glass plate washing machine, an inspection station for the visual monitoring of the glass plates complete with subsequent frame positioning, and an automatic assembling, gas filling, and press robot.
With its three separate brush-pair drives, the washing machine ensures great results on sheets up to 15 millimetres in thickness. Its external, chainless brush and transport drive promises additional convenience and reassurance.
The high-contrast, well-lit inspection area complete with coloured signal lights provides a quick and reliable inspection facility for glass plates. The automatic beam setting for vertical positioning of the frame means the spacer can be applied precisely, even by inexperienced users.

The core of the Glaston COMFORT BOX is the insulating glass press that assembles the insulating glass units, fills them with inert gas, and presses them precisely in one single processing step. This works just as well with non-stepped, rectangular units as with shaped formats with steps on up to three sides and works with both double and triple insulating glass units: the customer has the choice – even when it comes to the spacer material. The inert gas filling is completed quickly, efficiently and at a high level directly into the units, while adjustable press plates ensure precise and uniform insulating glass pressing.

The line is rounded off with a tilt table to discharge the units ready for the subsequent manual standard sealing. It goes without saying that the equipment for the manual sealing – the rotating sealing table and the manual sealing unit – are also available from Glaston.
For those who do not wish to seal manually, the line can be expanded with a conveyor and an automatic sealing robot. With the aid of the sealing robot COMFORT’SEALER, the customer can upgrade their Glaston COMFORT BOX IG line from an entry-level solution for industrial glass production to an automated production line.
The main advantage of the COMFORT’SEALER is its precise dosage function which determines precisely the joint depth and then subsequently applies the exact volume of sealing material required. This level of precision cannot be achieved when sealing manually.
Glaston COMFORT BOX can also be expanded with machines for the production of spacers: a frame bending robot SPACER’BENDER, a desiccant filling station SPACER’FILLER as well as a SPACER’BUTYLEXTRUDER for the double-sided coating of rectangular and shaped frames with butyl represent ideal additions to this IG line.

Glaston COMFORT BOX technical data at a glance:
• Output: up to 800 gas-filled insulating glass units per shift
• Transport speed: 48 m/min
• Working height: 2.70 m
• Minimum glass format: 190 x 350 mm
• Maximum glass format: 2700 x 3500 mm
• Glass thickness: 3 – 15 mm
• Thickness of the insulating glass units: 12 – 60 mm
• Spacer width: 6 – 24 mm
Insulating glass types:
• Double and triple units
• Rectangular and shaped formats
• 1- up to 3-sided stepped units
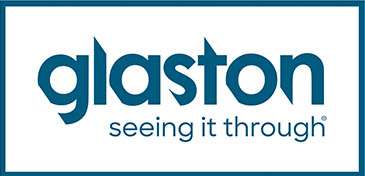
Email: info@glaston.net
Website: www.glaston.net