Today, mechanical processes are reaching their limits when it comes to many glass products. Precision cutting, drilling, coating, melting and texturing state-of-the-art specialist glass are now all performed by lasers.
Having previously taken a critical view, today the glass industry simply could not function without lasers in modern production. Because it is low-maintenance and cost-efficient, laser technology is also economically attractive. One example is when processing ultra-thin glass for displays: this glass with often tiny cut-outs cannot be cut using mechanical means. In order to allow noticeable improvement in mobile reception inside buildings, lasers help to break up coated insulating glass units with finely drawn patterns, without any significant change to how the glass looks. Lasers even enable thermal processes: glass coatings can be heated to hundreds of degrees and thus changed, without subjecting the glass itself to these temperatures. This technology offers enormous benefits when it comes to processing thermally tempered glass in particular.

Using laser technology allows processors to save CO2 or even, where alternative energies are used, eliminate its use altogether. This is because there is no need for energy-intensive treatment of process water following additional grinding, nor for producing cutting and separation equipment with high levels of material wear.
VDMA’s industrial working group Research & Technology dedicated its most recent meeting in February to the topic, with various companies presenting their applications.
Flabeg Automotive Germany GmbH from Furth im Wald offers solutions for a wide range of glass and mirror applications in glass finishing, using lasers for cutting and drilling. Laser cutting has two stages. First, the line to be cut is perforated. Then a crack is drawn along the perforation so that the glass can be split off. Stacking the filaments on top of each other makes this process possible up to a glass thickness of 12 millimetres and a speed of up to 500 mm/s, although only for flat glass.
Laser drilling, on the other hand, has just a single stage in which the laser focus is guided through the glass thickness. This process offers more design options for the glass, such as where it is slightly curved. In both processes, the energy input comes from non-linear processes. This causes structural changes to the glass, highly localised in terms of both space and time, so that the glass is not impaired outside the focus.
The Saint-Gobain Group uses various processes in its production, especially in the automotive glass and building glass segments. The glass products made there have to offer special functions, such as guaranteeing heat protection and high light transmission at the same time. Some of the layers applied also have different tasks. If they are electrical conductors, for instance, they can be heated and thus used as windscreens. Coating is usually done using a CVD or PVD process.
A silver-based low-E coating, for example, is amorphous in its untreated state. When heated, it crystallises, and its heat protection and light transmission properties increase. The challenge is to only apply the heat treatment to the low-E layer. Classic processes that heat the entire pane of glass cannot achieve this. The coated pane now passes under a laser line that is just 100 µm wide. This heats the layer to temperatures of up to 500°C, while the glass temperature rises no higher than 150°C.
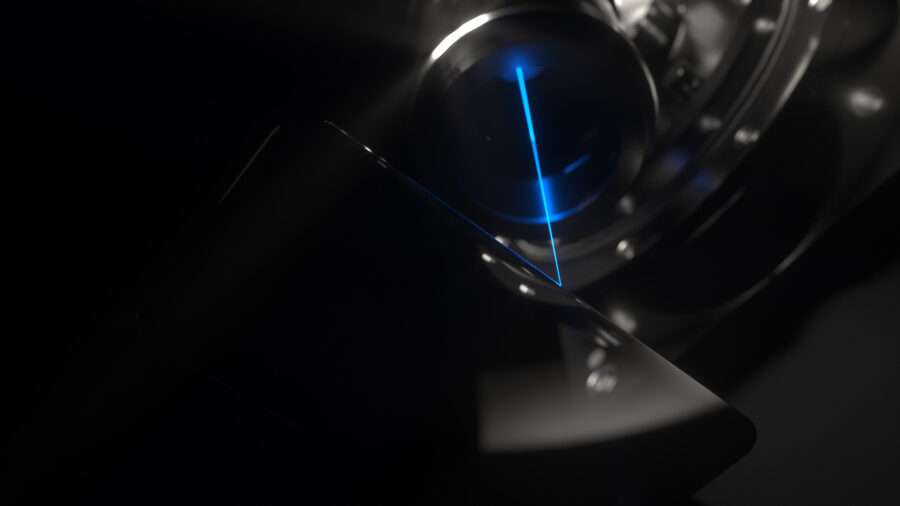
Schott AG from Mainz has also gained extensive experience with a wide range of laser processes over the last few years, especially for processing ultra-thin glass. Ultrashort pulse lasers, for example, allow the glass to be hardened, printed and coated in a larger geometry first, before being separated into numerous small items in the final step. This puts significant demands on the separation process: clean cuts with no particle contamination and an edge quality that allows the cut items to be used immediately in the end product are essential. These products are used in areas including medical diagnostics, as decorative elements or for markings used in product tracing.
Schott’s production also uses laser micro bonding – a technology used to weld different materials together, which is especially useful for miniature applications in medical and technical fields. The heat formed in the laser focus area is limited to a small space. As a result, the surrounding material is not damaged and, when different materials are welded with the glass, their different thermal expansion coefficients are not a problem.

The Fraunhofer Institute for Solar Energy Systems (ISE) conducts research into radio-transparent insulating glass. Coated glass is an integral part of modern buildings, providing light while also having a positive effect on the building’s energy budget. Unfortunately, one disadvantage of coatings across the entire glass surface is that they reflect not only heat radiation, but also the electromagnetic radiation used for mobile communications and data services – even more than reinforced concrete. In the ISE’s view, one solution would be to structure the layer in segments by using a laser to remove the coating in fine lines. The size of the segments plays a role in improving radio wave reception in the various frequency bands. The GSM standard with a frequency of 900 MHz, for example, needs segments that are significantly smaller than the wavelength of around 33 cm (l/4 = 8.3 cm). On the other hand, 5G applications at around 3.4 GHz need segments that are much smaller than 8.8 cm (l/4 = 2.2 cm). But heat protection also needs to be retained at the same time. Different segment geometries demonstrated a significant improvement in the frequency ranges relevant today. Nevertheless, radio wave transmission cannot be increased equally across all frequency ranges, as one grid size is always fixed.

Corning Laser Technologies GmbH uses a wide range of laser systems in the development of fully automated production systems, conducting a wide range of process steps. As well as ablative processes for glass and coatings, such as in drilling and chamfering applications, the company uses lasers to conduct cutting and separation steps in particular. This production technique not only impresses with high edge quality – in terms of both edge strength and surface roughness – but also enables a high absolute accuracy of the separated parts thanks to precise beam guidance. Lasers thus enhance quality in the production of glass products very effectively. Much more important, however, is the potential to unlock completely new market segments that are not possible – or take a great deal more effort – with conventional methods. Examples include processing ultra-thin glass (t < 50 μm), chemically hardened glass and glass with decorative or technical finishing and coating. Consumer electronics, augmented reality, architecture and the automotive industry are the key fields in which this is used. In order to use a laser system economically in production, however, the production machines need to be custom-built for the product in question. As well as a fundamental understanding of laser-material interaction, this also demands enormous expertise in the technical implementation of process control. To this end, systems suited for industrial applications and 24/7 use with a high level of automation and options for deep integration are needed, which achieve maximum utilisation of the laser systems and thus the shortest possible cycle times. For maximum efficiency, components for beam shaping and transportation need to be adapted to both the product and the respective laser system. Thanks to Corning’s consistent further development of the laser processing technology, it is now possible to process even three-dimensional glass workpieces reliably and to achieve further options in design and functionality.